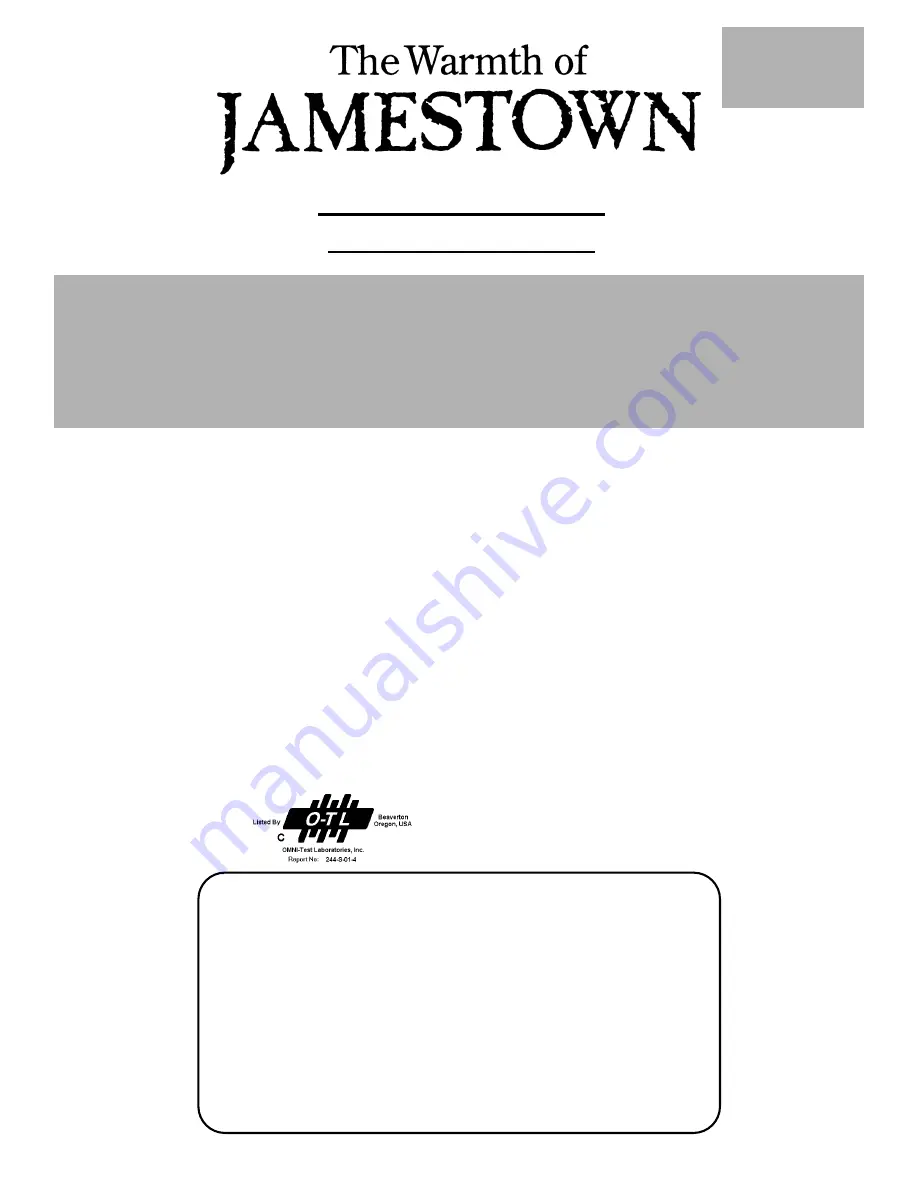
Pellet Stove Owner’s Manual
Models J1000B and J2000T
Listed by OMNI-Test Laboratories, Inc.
to
UL 1482-1994, ASTM E 1509-95, ULC-S627-M93 and ULC-S628-M93
E.P.A. Rated
For use with 1/4 in. (6mm.) to 3/8 in. (10 mm.) Wood Pellet Fuel
Also For Use In Mobile Homes
Please read this entire manual before installation and use of this pellet fuel-
burning room heater. Failure to follow these instructions could result in property
damage, bodily injury or even death.
Contact local building or fire officials about restrictions and installation inspection
requirements in your area.
Save this manual for future reference.
Pellet Stoves
First in Quality, First in Value
2006
EDITION
P.O. Box 400, Vermilion Bay, Ontario, Canada POV 2V0
Phone: (807) 227-2745 Fax: (807) 227-2172
www.jamestownpelletstoves.ca
Certified for Canada and USA
Summary of Contents for J1000B
Page 2: ......
Page 8: ...Page vi 1998 2006 Edition ...
Page 16: ...Page 8 1998 2006 Edition ...
Page 20: ...Page 12 1998 2006 Edition ...
Page 36: ...Page 28 1998 2006 Edition ...
Page 44: ...Page 36 1998 2006 Edition ...
Page 45: ...Page 37 1998 2006 Edition ...
Page 46: ...VIII 5 Jamestown Control Panel Page 38 1998 2006 Edition ...
Page 61: ...Page 53 1998 2006 Edition ...
Page 62: ...Page 54 1998 2006 Edition ...
Page 63: ...Page 55 1998 2006 Edition ...
Page 64: ...Page 56 1998 2006 Edition ...
Page 69: ...Page 61 1998 2006 Edition ...
Page 70: ...Page 62 1998 2006 Edition ...
Page 79: ...Appendix A 3 1998 2006 Edition ...
Page 80: ...Appendix A 4 1998 2006 Edition ...
Page 81: ...Appendix A 5 1998 2006 Edition ...
Page 82: ...Appendix A 6 1998 2006 Edition ...
Page 84: ...Appendix B 2 1998 2006 Edition ...
Page 87: ...APPENDIX E AUGER MOTOR BRACKET INSTALLATION Appendix E 1 1998 2006 Edition ...
Page 90: ...Appendix F 3 1998 2006 Edition ...
Page 93: ...APPENDIX H J1000 CROSSFLOW FAN Part 07EEG Appendix H 1 1998 2006 Edition ...
Page 94: ...APPENDIX I 1 EXHAUST BLOWER ASSEMBLY MODEL J1000 Appendix I 1 1998 2006 Edition ...