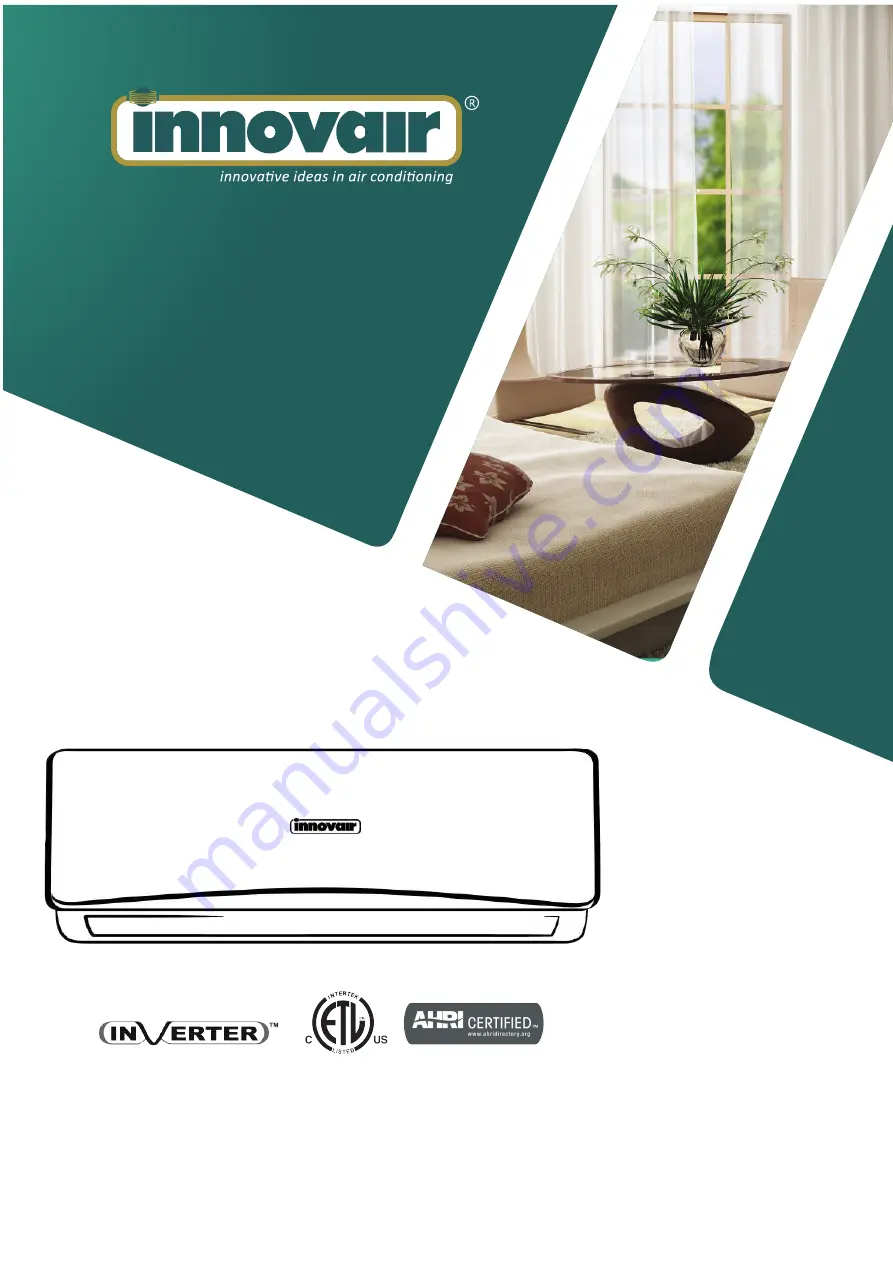
NEXXOS
INVERTER MINI SPLIT
USER
MANUAL
NIN413C2V33
NIN720C2V33
NIN728C2V33
WARNING
• The information contained in the manual is intended for use by a qualified service technician
familiar with safety procedures and equipped with the proper tools and test instruments
• Installation or repairs made by unqualified persons can result in hazards to you and others.
• Failure to carefully read and follow all instructions in this manual can result in equipment
malfunction, property damage, personal injury and/or death.
• This service is only for service engineer to use.