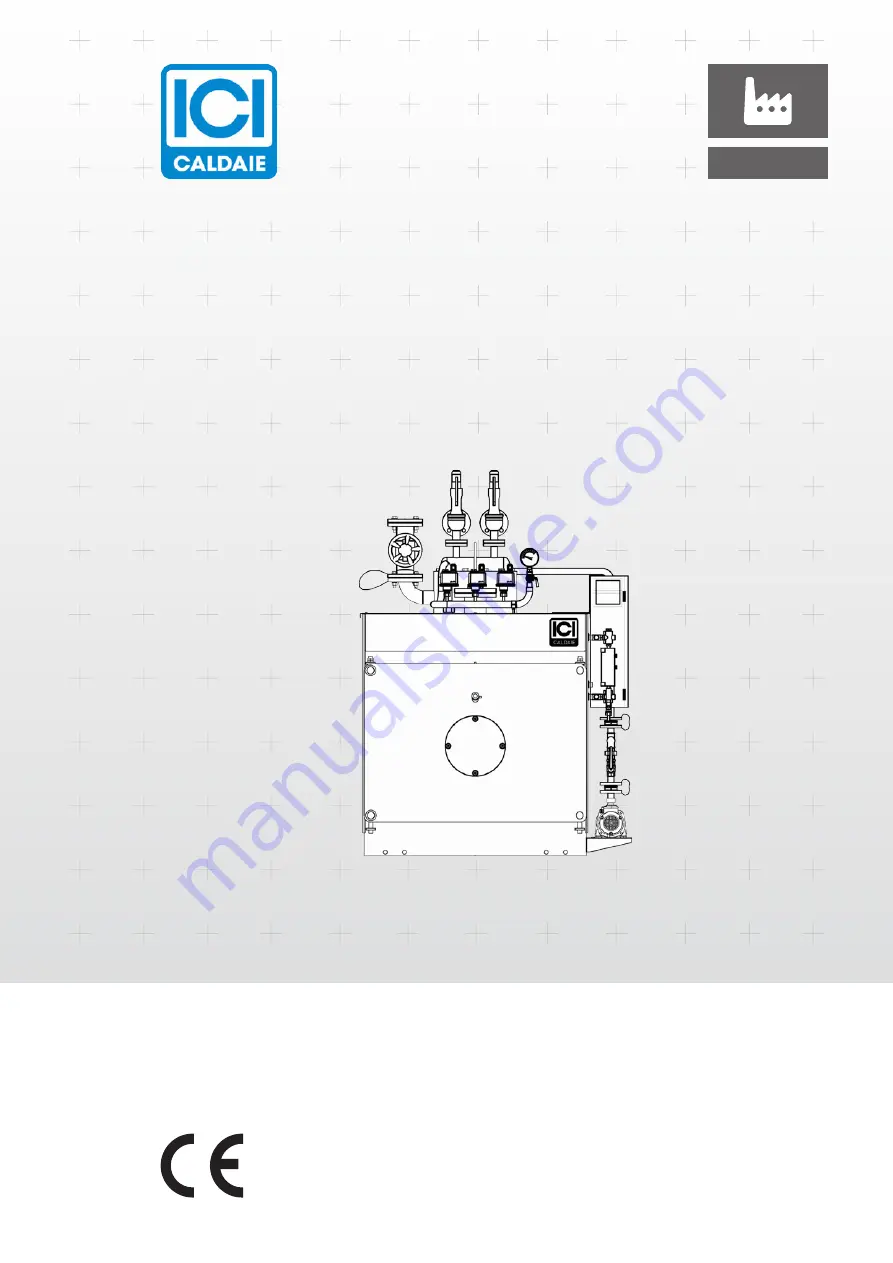
BNX_100_3000_EN Ed. 08 - 03/2019
EN
Low-pressure reverse flame steam boiler
BNX
INSTALLATION, USE AND MAINTENANCE MANUAL
Cooke Industries - Phone: +64 9 579 2185 Email: [email protected] Web: www.cookeindustries.co.nz
BNX_100_3000_EN Ed. 08 - 03/2019
EN
Low-pressure reverse flame steam boiler
BNX
INSTALLATION, USE AND MAINTENANCE MANUAL
Cooke Industries - Phone: +64 9 579 2185 Email: [email protected] Web: www.cookeindustries.co.nz