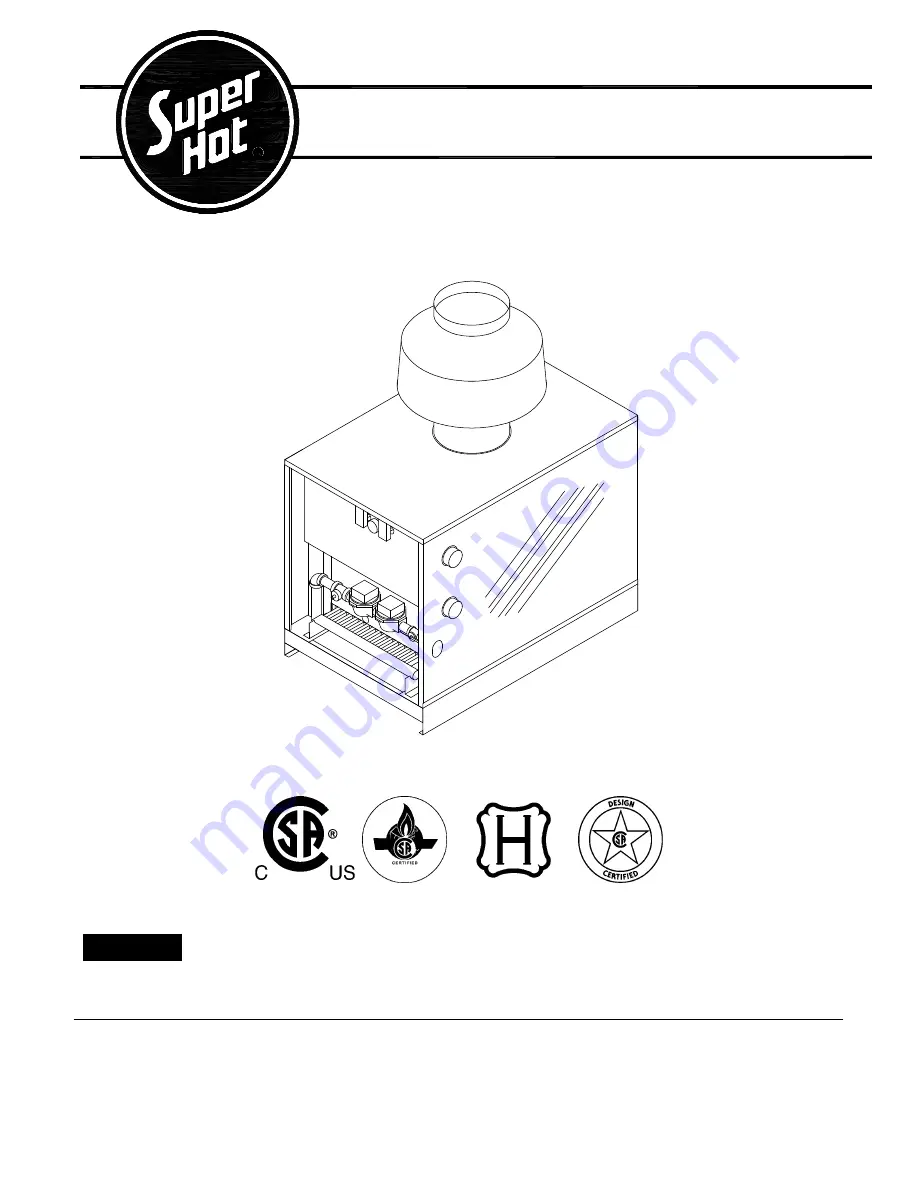
PN3362421
AAA SERIES GAS BOILERS
INSTALLATION AND SERVICE MANUAL
FOR MODELS AAA-480 TO AAA-3000
Featuring the BTC SERIES Controller on 1 & 2 stage models
See rear cover for Index
Manufactured by
Allied Engineering Company
Division of E-Z-Rect Manufacturing Ltd.
Manufacturers of Gas and Electric Boilers, Stainless Steel Tanks, Heat Exchangers and Electric Boosters
94 Riverside Drive, North Vancouver, B.C. V7H 2M6
•
Telephone (604) 929-1214
•
www.alliedboilers.com
Branches: Calgary
•
Edmonton
•
Toronto
Improper installation, adjustment, alteration, service or maintenance can cause property
damage, injury, or loss of life
.
Please carefully read this manual. For assistance or
additional information, consult a qualified installer, service agency or the gas supplier.
WARNING
Summary of Contents for AAA-3000 series
Page 28: ...AAA Series Gas Boiler Installation and Service Manual 28 ...
Page 29: ...AAA Series Gas Boiler Installation and Service Manual 29 Wiring Diagrams Section 7 ...
Page 30: ...AAA Series Gas Boiler Installation and Service Manual 30 ...
Page 31: ...AAA Series Gas Boiler Installation and Service Manual 31 ...
Page 34: ...AAA Series Gas Boiler Installation and Service Manual 34 NOTES Section 9 ...
Page 35: ...AAA Series Gas Boiler Installation and Service Manual 35 NOTES Section 9 ...