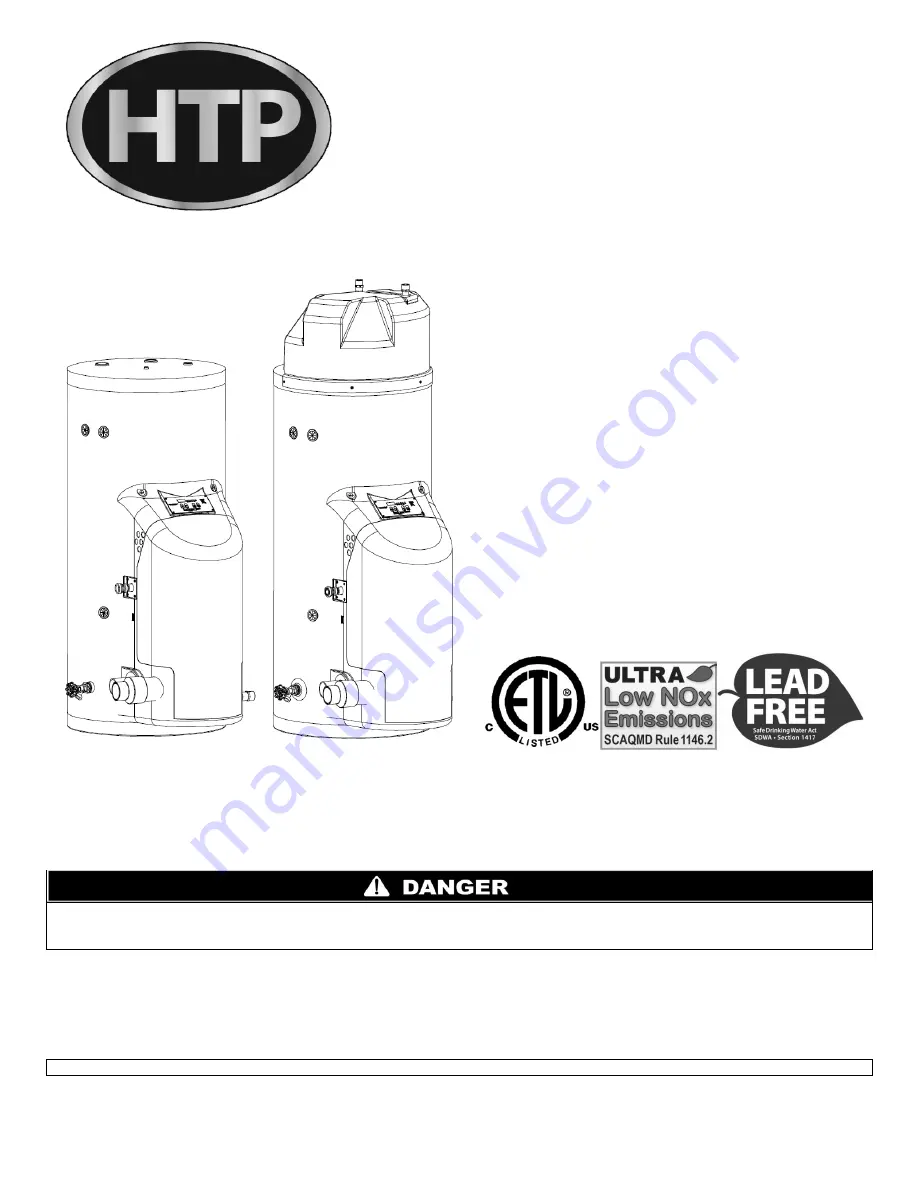
120 Braley Rd. P.O. Box 429 East Freetown, MA 02717-04 www.htproducts.com
LP- 325 REV. 3.3.15
Pioneer
Versa-Flame
INSTALLATION
START-UP
MAINTENANCE
PARTS
Pioneer Appliance Models*
Versa-Flame** Combination Appliance Models*
PHR100-55 / 130-55 / 160-55 / 199-55
PHR130-55C / 160-55C / 199-55C
*A su
ffix of “LP” denotes propane gas
NOTICE:
HTP reserves the right to make product changes or updates without notice and will not be held liable for typographical errors
in literature.
**The surfaces of these products contacted by consumable water contain less than 0.25% lead by weight, as required by the Safe
Drinking Water Act, Section 1417.
NOTE TO CONSUMER: PLEASE KEEP ALL INSTRUCTIONS FOR FUTURE REFERENCE.
This manual must only be used by a qualified heating installer/service technician. Read and understand all instructions in this manual
before installing. Perform steps in the order given. Failure to comply will result in substantial property damage, severe personal injury,
or death.
Summary of Contents for Pioneer
Page 17: ...17 LP 325 REV 3 3 15 Figure 3 Dimensions ...
Page 28: ...28 LP 325 REV 3 3 15 Figure 9 DHW Pack Performance on 199K BTU Models ...
Page 44: ...44 LP 325 REV 3 3 15 Figure 20 ...
Page 47: ...47 LP 325 REV 3 3 15 Figure 22 Internal Wiring Diagram ...
Page 67: ...67 LP 325 REV 3 3 15 Figure 30 Pioneer and Versa Flame ...
Page 68: ...68 LP 325 REV 3 3 15 Figure 31 Pioneer and Versa Flame ...
Page 71: ...71 LP 325 REV 3 3 15 ...
Page 72: ...72 LP 325 REV 3 3 15 ...