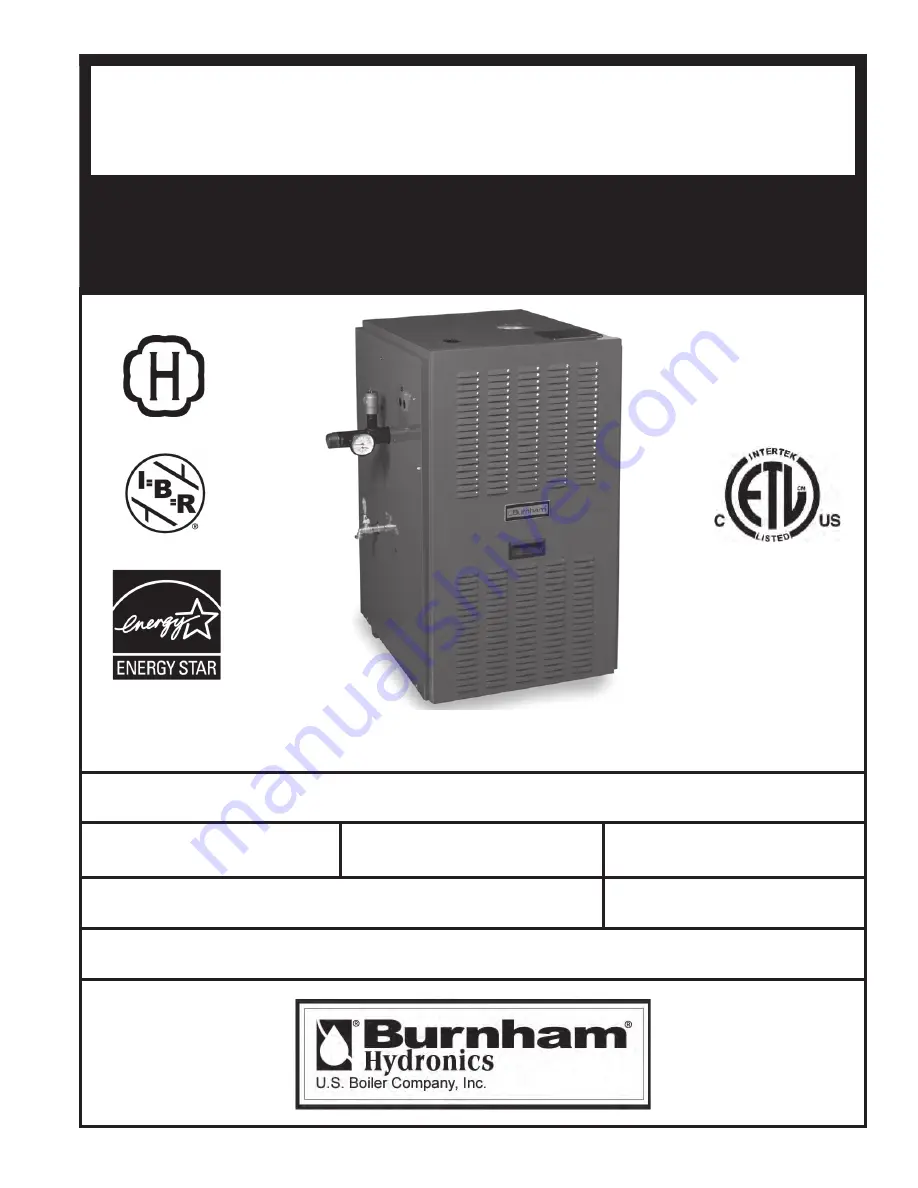
8140708R10-6/09
As an ENERGY STAR
®
Partner, Burnham Hydronics has determined that the PVG Series meets the ENERGY
STAR
®
guidelines for energy efficiency established by the United States Environmental Protection Agency (EPA).
Price - $5.00
n
o
n
o
i
t
a
m
r
o
f
n
i
g
n
i
k
e
e
s
n
e
h
W
.
r
o
t
c
a
r
t
n
o
c
g
n
i
t
a
e
h
r
u
o
y
ll
a
c
,
r
e
l
i
o
b
o
t
s
r
i
a
p
e
r
r
o
e
c
i
v
r
e
s
r
o
F
.
l
e
b
a
L
g
n
i
t
a
R
n
o
n
w
o
h
s
s
a
r
e
b
m
u
N
l
a
i
r
e
S
d
n
a
r
e
b
m
u
N
l
e
d
o
M
r
e
l
i
o
B
e
d
i
v
o
r
p
,
r
e
l
i
o
b
r
e
b
m
u
N
l
e
d
o
M
r
e
l
i
o
B
G
V
P
r
e
b
m
u
N
l
a
i
r
e
S
r
e
l
i
o
B
e
t
a
D
n
o
i
t
a
ll
a
t
s
n
I
r
o
t
c
a
r
t
n
o
C
g
n
i
t
a
e
H
r
e
b
m
u
N
e
n
o
h
P
s
s
e
r
d
d
A
D
N
A
G
N
I
T
A
R
E
P
O
,
N
O
I
T
A
L
L
A
T
S
N
I
R
O
F
S
N
O
I
T
C
U
R
T
S
N
I
E
C
I
V
R
E
S
™
G
V
P
R
E
L
I
O
B
D
E
R
I
F
-
S
A
G
Summary of Contents for PVG
Page 6: ... Figure 2 Dimensions ...
Page 14: ...14 Figure 4A Recommended Horizontal Vent Installation ...
Page 15: ...15 Figure 4B Alternate Horizontal Vent Installation ...
Page 16: ...16 Figure 5 Horizontal Vent Terminal Configuration 3 or 4 Vent ...
Page 18: ...18 Figure 7 Attic Offset Figure 6 Vertical Vent Installation ...
Page 24: ...24 Figure 11 Recommended Boiler Piping For Circulator Zoned Heating Systems ...
Page 25: ...25 Figure 12 Recommended Water Piping for Zone Valve Zoned Heating Systems ...
Page 30: ...30 Figure 14 Internal Boiler Wiring Schematic Diagram ...
Page 33: ...33 Figure 16 Single Heating Zone Only Wiring Schematic ...
Page 35: ...35 Figure 18 Circulator Zoned System Wiring Schematic ...
Page 36: ...36 Figure 19 Zone Valve Zoned System Wiring Schematic ...
Page 37: ...37 Figure 20 Different Manufacturer s Zone Valve Connections to Honeywell R8889 ...
Page 39: ...39 Figure 21 Modular Boiler Piping ...
Page 41: ...41 Figure 22 Operating Instructions ...
Page 44: ...44 Honeywell Electronic Ignition Troubleshooting Guide Figure 24 Troubleshooting Guide ...
Page 49: ...49 Figure 30 Flue and Burner Cleanout 1 Burner ...
Page 51: ...51 THIS PAGE LEFT BLANK INTENTIONALLY ...
Page 52: ...52 ...
Page 53: ...53 ...
Page 56: ...56 ...
Page 60: ...60 ...
Page 66: ...66 SERVICE RECORD DATE SERVICE PERFORMED ...