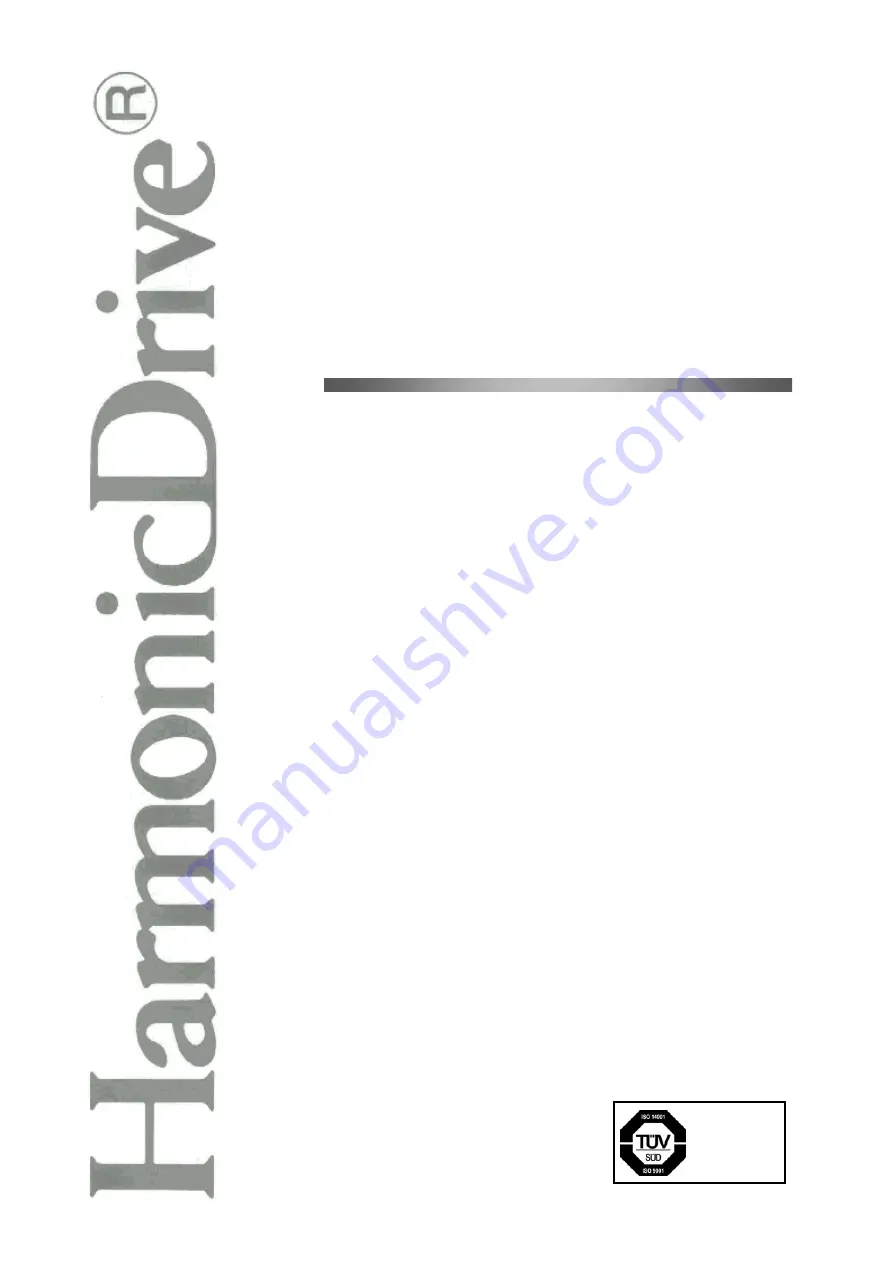
DC Servo Driver
HS-360 Series Technical Manual
●
Thank you very much for your purchasing our HS-360 series
servo driver.
●
Be sure to use sufficient safety measures when installing
and operating the equipment so as to prevent an accident
resulting in a serious physical injury damaged by a
malfunction or improper operation.
●
Product specifications are subject to change without notice
for improvement purposes.
●
Keep this manual in a convenient location and refer to it
whenever necessary in operating or maintaining the units.
●
End user of the driver should have a copy of this manual.
ISO14001
(
HOTAKA Plant
)
ISO9001