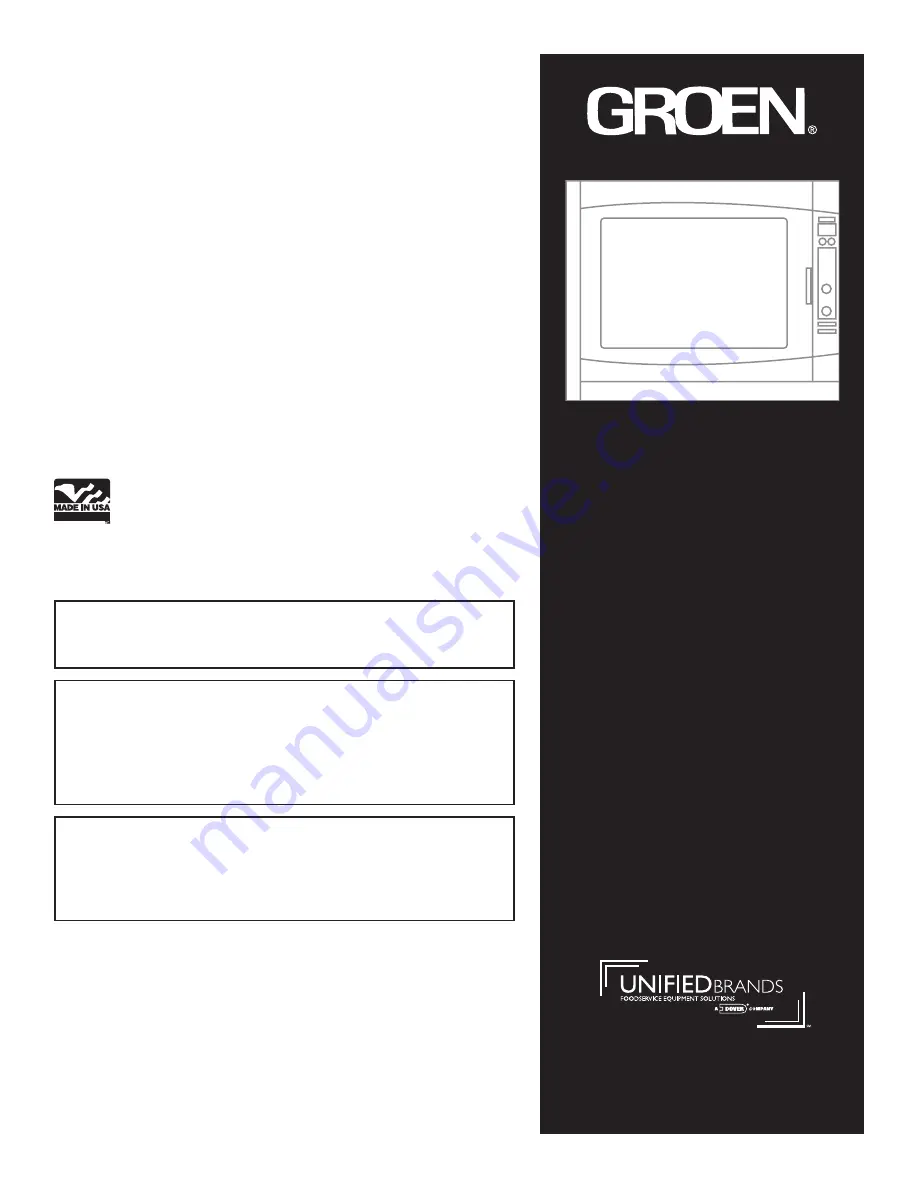
This manual provides information for:
MODELS TRI-RES-20G
& (2)TRI-RES-20G
COMBINATION OVEN
· Self Contained
· Gas Heated
· Capacity:
TRI-RES-20G = 10 Steamer Pans Per Cavity
SERVICE MANUAL
IMPORTANT INFORMATION, KEEP FOR OPERATOR
1055 Mendell Davis Drive
Jackson, MS 39272
888-994-7636, fax 888-864-7636
groen.com
PART NUMBER 152797, REVISION A
.
E
C
N
E
R
E
F
E
R
E
R
U
T
U
F
R
O
F
D
E
N
I
A
T
E
R
E
B
T
S
U
M
L
A
U
N
A
M
S
I
H
T
READ, UNDERSTAND AND FOLLOW THE INSTRUCTIONS AND
WARNINGS CONTAINED IN THIS MANUAL.
FOR YOUR SAFETY
Do not store or use gasoline or other flammable vapors
and liquids in the vicinity of this or any other appliance.
POST IN A PROMINENT LOCATION
Instructions to be followed in the event user smells gas.
This information shall be obtained by consulting your
local gas supplier. As a minimum, turn off the gas and
call your gas company and your authorized service agent.
Evacuate all personnel from the area.
WARNING
Improper installation, adjustment, alteration, service or
maintenance can cause property damage, injury or death.
Read the installation, operating and maintenance instructions
thoroughly before installing or servicing this equipment.
NOTIFY CARRIER OF DAMAGE AT ONCE
It is the responsibility of the consignee to inspect the container upon receipt of
same and to determine the possibility of any damage, including concealed dam-
age. Unified Brands suggests that if you are suspicious of damage to make a
notation on the delivery receipt. It will be the responsibility of the consignee to file
a claim with the carrier. We recommend that you do so at once.
Manufacture Service/Questions 888-994-7636.
Information contained in this document is known to be current and accurate at the time
of printing/creation. Unified Brands recommends referencing our product line websites,
unifiedbrands.net, for the most updated product information and specifications.
Summary of Contents for 2TRI-RES-20G
Page 40: ...PART NUMBER 152797 REVISION A CALL 888 994 7636 FOR TECHNICAL SUPPORT 40 Wiring Diagram ...
Page 41: ...PART NUMBER 152797 REVISION A CALL 888 994 7636 FOR TECHNICAL SUPPORT 41 Ladder Diagram ...
Page 43: ......
Page 44: ... ENDELL AVIS RIVE s ACKSON 3 s s AX GROEN COM 0 24 5 2 PART NUMBER 152797 REVISION A ...