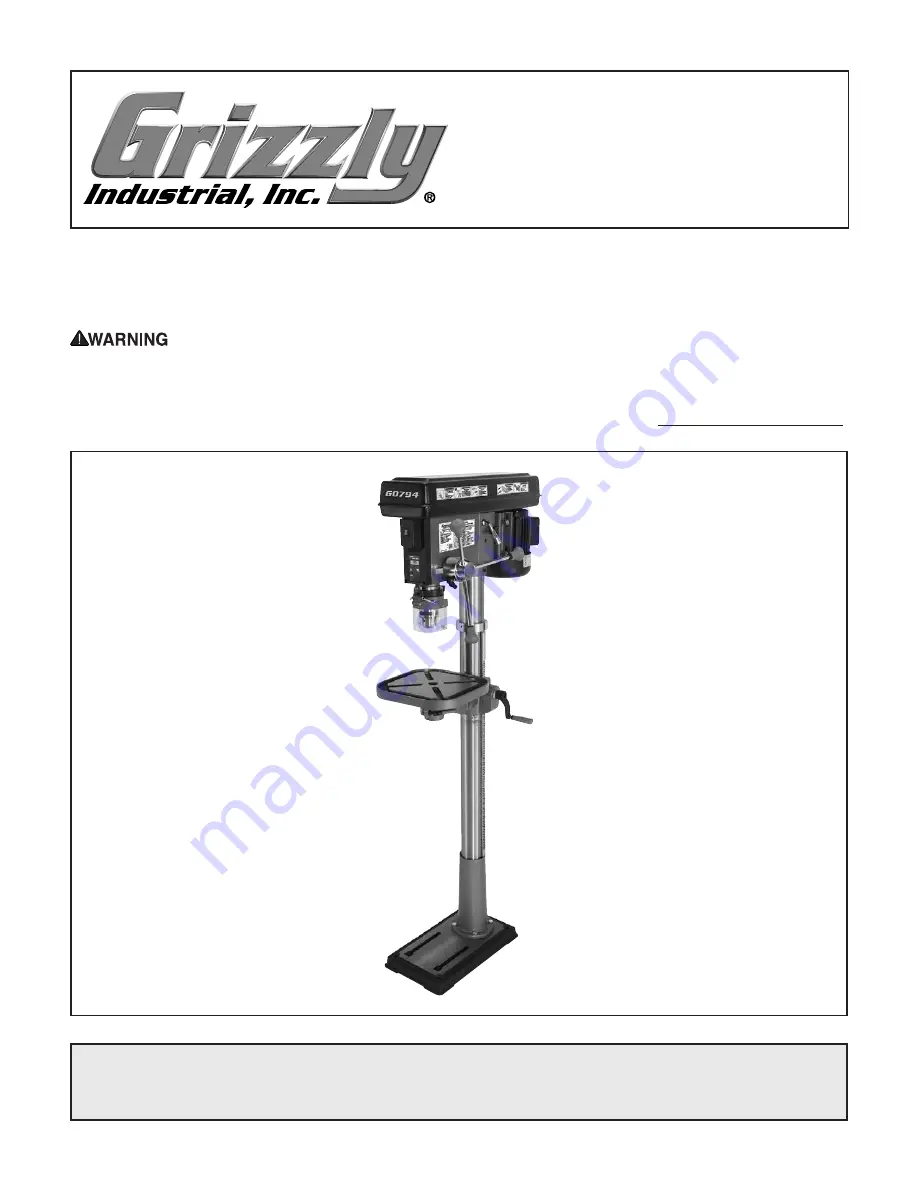
COPYRIGHT © DECEMBER, 2014 BY GRIZZLY INDUSTRIAL, INC. REVISED MARCH, 2019 (KB)
WARNING: NO PORTION OF THIS MANUAL MAY BE REPRODUCED IN ANY SHAPE
OR FORM WITHOUT THE WRITTEN APPROVAL OF GRIZZLY INDUSTRIAL, INC.
(FOR MODELS MANUFACTURED SINCE 05/18) #WK16957 PRINTED IN CHINA
The Model G0794 is the same machine as the Model G7944, except the G0794 has a digital readout for
spindle downfeed, and it is equipped with a laser drilling guide in place of the work light. Aside from the dif-
ferences noted in this insert, all other content in the Model G7944 owner's manual applies to this machine.
:
To reduce the risk of serious injury, you MUST read and understand this insert—and
the entire Model G7944 manual—BEFORE assembling, installing, or operating this machine!
If you have any further questions about this manual insert or the differences between the Model G0794
and the Model G7944, contact our Technical Support at (570) 546-9663 or email [email protected].
MODEL G0794
FLOOR DRILL PRESS
WITH LASER AND DRO
MANUAL INSERT
Summary of Contents for G7943
Page 12: ... 12 Model G0794 Mfd Since 05 18 ...
Page 64: ......