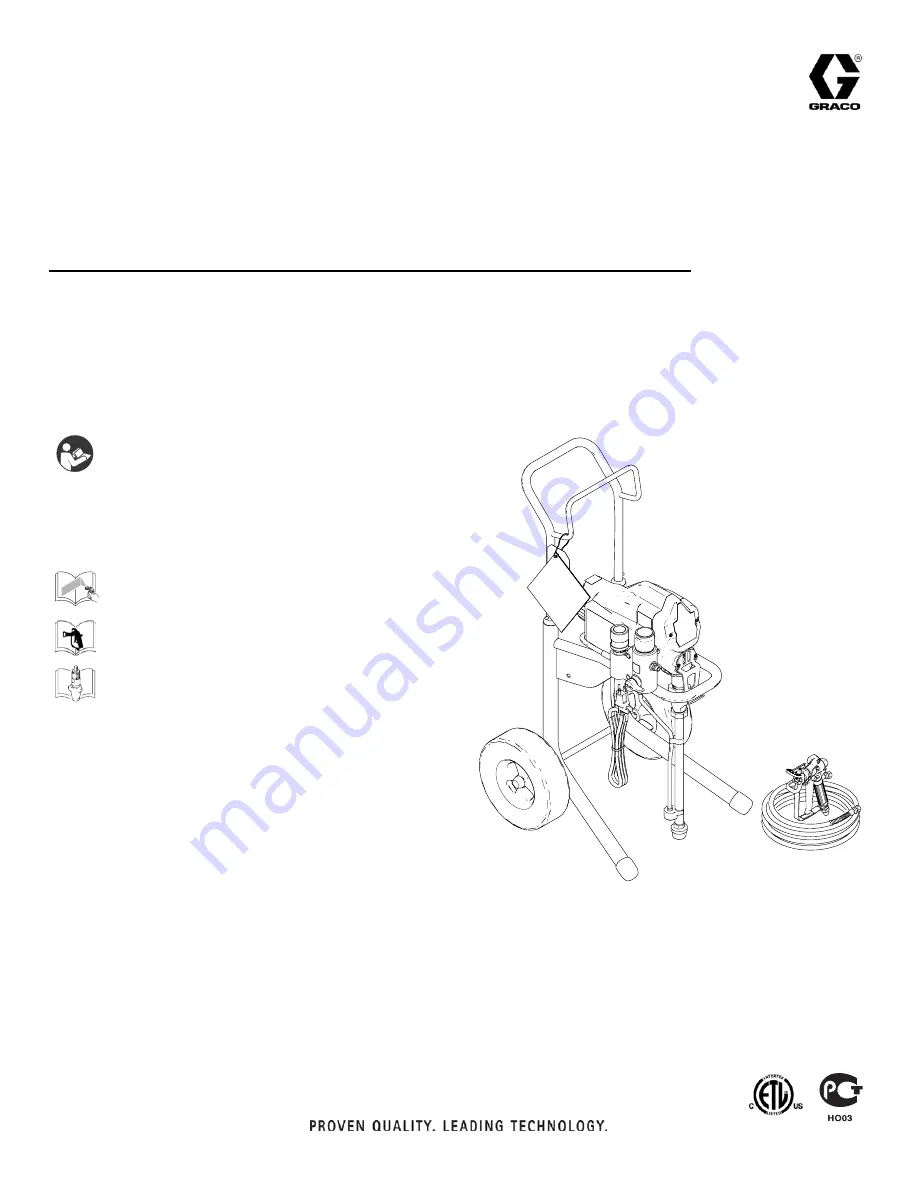
-
For portable spray application of architectural paints and coatings -
190
ES
Model: 261825
210
ES
Model: 261830
Maximum Working Pressure: 3000 psi (20.7 MPa, 207 bar)
Important Safety Instructions
Read all warnings and instructions in this
manual. Save these instructions.
Related Manuals
311988
312830
English
312831
Français
312832
Español
312015
ti16975a
311990F
Repair
190
ES
/210
ES
™
Electric Airless Sprayer
US Patent No. D580,518,S
ENG