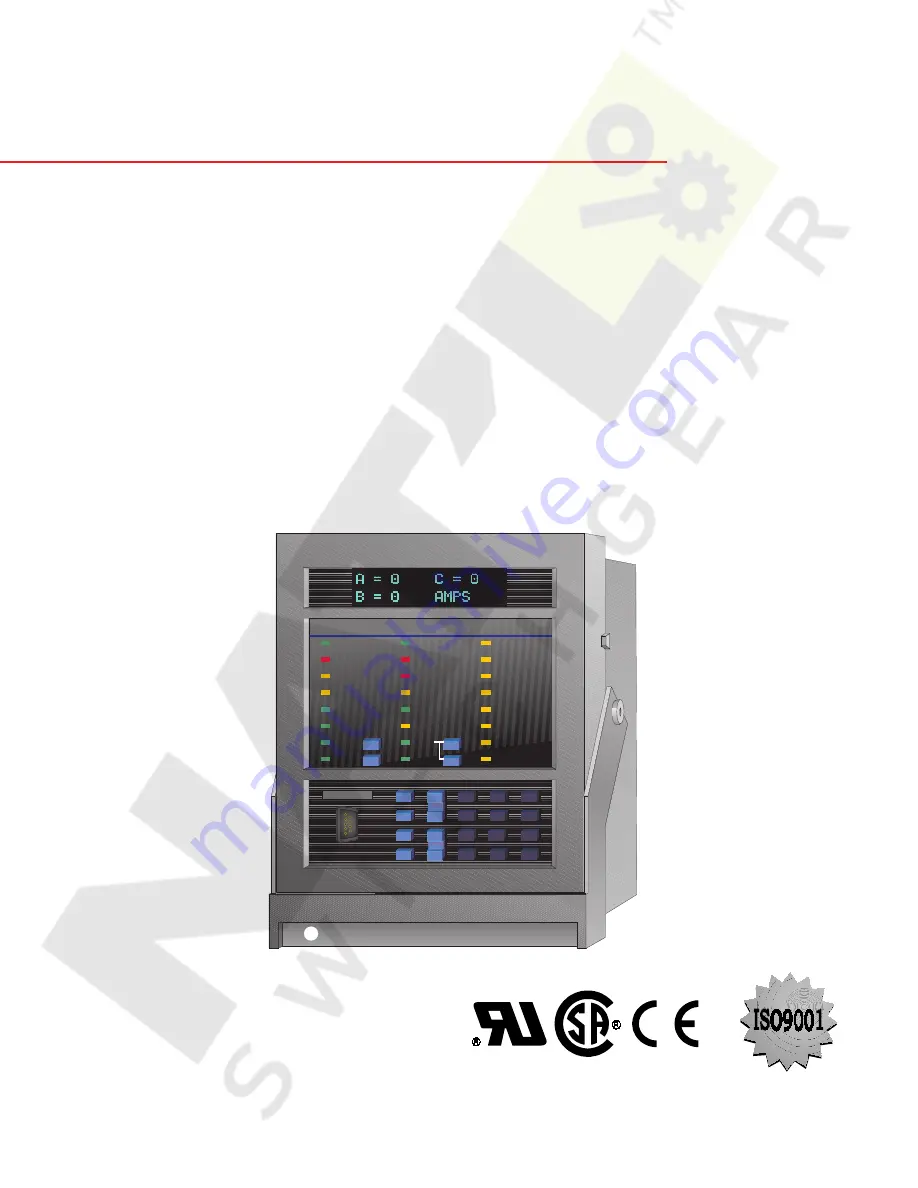
R
E G
I S T E R
E D
750/760
FEEDER MANAGEMENT RELAY
®
Instruction Manual
Firmware Rev.: 402-000
Analog Rev.: 27H402A4.000
Control Rev.: 27H402C4.000
Manual P/N: 1601-0044-AL (GEK-106293A)
Copyright © 2002 GE Power Management
GE Power Management
215 Anderson Avenue, Markham, Ontario
Canada L6E 1B3
Tel: (905) 294-6222 Fax: (905) 294-8512
Internet: http://www.GEindustrial.com/pm
Manufactured under an
ISO9001 Registered system.
g
GE Power Management
760
Feeder Management
®
818789A3.CDR
RELAY IN SERVICE
760 STATUS
SYSTEM STATUS
OUTPUT STATUS
BREAKER OPEN
1 TRIP
TRIP
BREAKER CLOSED
2 CLOSE
ALARM
RECLOSURE
ENABLED
3 AUXILIARY
PICKUP
RECLOSURE
DISABLED
4 AUXILIARY
SETPOINT
GROUP 1
SETPOINT
GROUP 2
SETPOINT
GROUP 3
SETPOINT
GROUP 4
RECLOSURE
IN PROGRESS
5 AUXILIARY
RESET
OPEN
NEXT
SETPOINT
MESSAGE
VALUE
ACTUAL
CLEAR
STORE
CLOSE
RECLOSURE
LOCKOUT
6 AUXILIARY
LOCAL
7 AUXILIARY
8
PROGRAM PORT
PROGRAM PORT
REMOTE
BREAKER
SELF-TEST
WARNING
7
8
9
4
5
6
1
2
0
3
HELP
.
g
Summary of Contents for 750
Page 2: ......
Page 4: ......
Page 124: ...8 14 750 760 Feeder Management Relay GE Power Management 8 12 INSTALLATION 8 S1 RELAY SETUP 8 ...
Page 488: ...A 4 750 760 Feeder Management Relay GE Power Management A 1 FIGURES AND TABLES APPENDIXA A ...
Page 492: ...C 2 750 760 Feeder Management Relay GE Power Management C 1 WARRANTY INFORMATION APPENDIXC C ...
Page 502: ...x 750 760 Feeder Management Relay GE Power Management INDEX ...
Page 503: ...GE Power Management 750 760 Feeder Management Relay NOTES ...