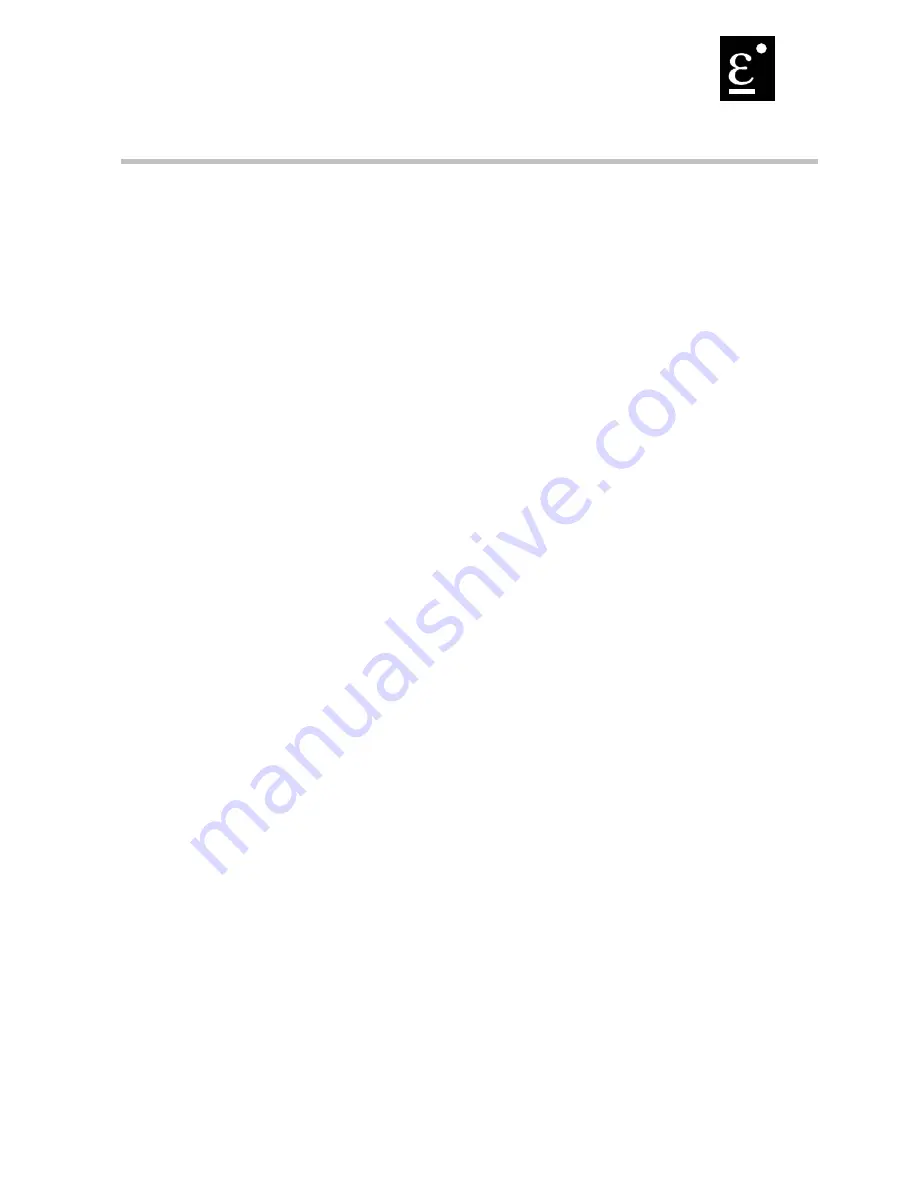
EUROTHERM
DRIVES
605 Series
Frequency
Inverter
Product Manual
HA463550U001 Issue 3
Copyright Eurotherm Drives Limited 2001
All rights strictly reserved. No part of this document may be stored in a retrieval system, or transmitted in any form or
by any means to persons not employed by a Eurotherm group company without written permission from Eurotherm
Drives Ltd.
Although every effort has been taken to ensure the accuracy of this document it may be necessary, without notice, to
make amendments or correct omissions. Eurotherm Drives cannot accept responsibility for damage, injury, or expenses
resulting therefrom.
Compatible with Version 5.x Software
Summary of Contents for 605 Series
Page 16: ...1 4 Getting Started 605 Series Frequency Inverter ...
Page 22: ...2 6 An Overview of the Inverter 605 Series Frequency Inverter ...
Page 34: ...3 12 Installing the Inverter 605 Series Frequency Inverter ...
Page 48: ...4 14 Operating the Inverter 605 Series Frequency Inverter ...
Page 156: ...8 2 Routine Maintenance and Repair 605 Series Frequency Inverter ...
Page 198: ...12 12 Certification for the Inverter 605 Series Frequency Inverter ...
Page 202: ...13 4 Application Notes 605 Series Frequency Inverter ...
Page 204: ...14 2 Serial Communications 605 Series Frequency Inverter ...