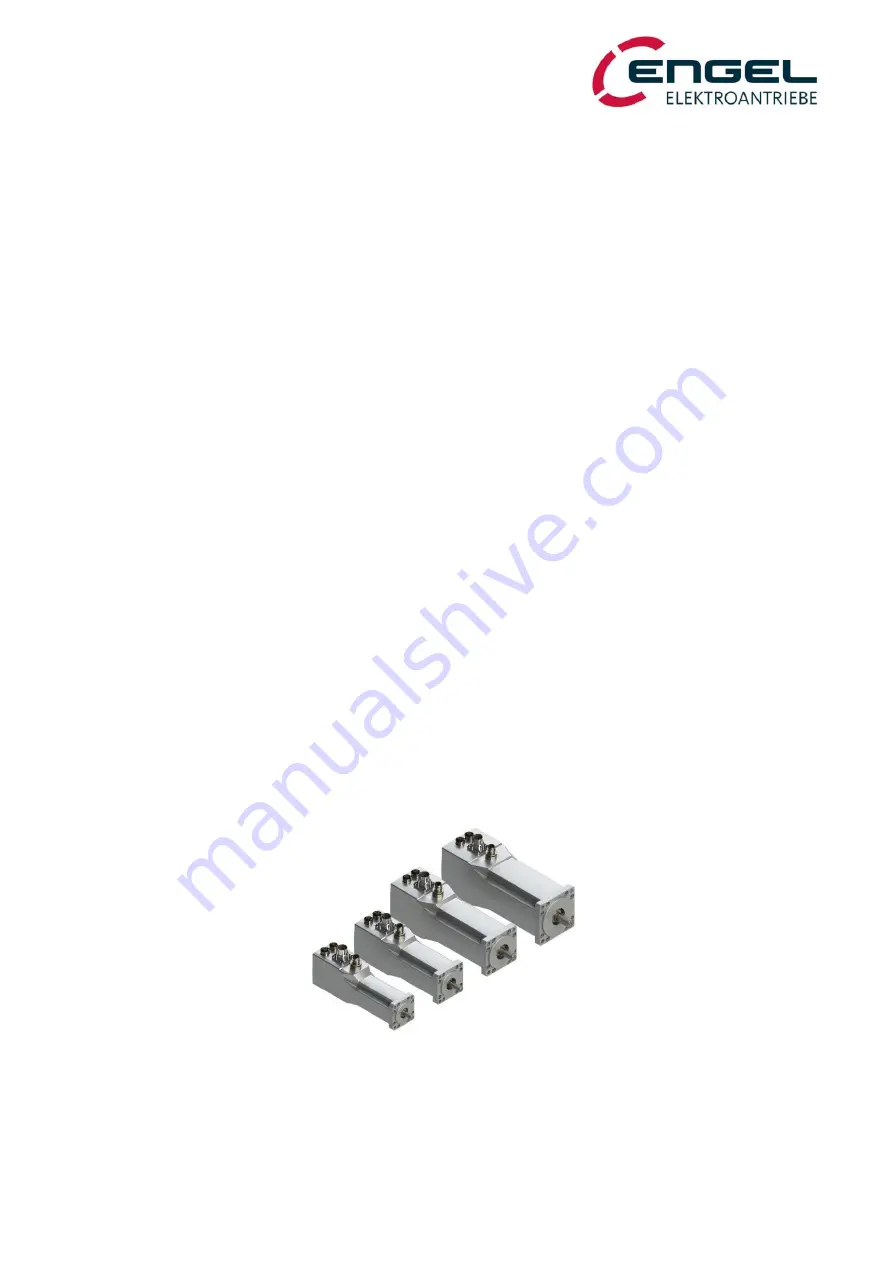
ENGEL Elektroantriebe GmbH ·
Am Klingenweg 10 · D-65396 Walluf
Telefon
+49 6123 9942-0 ·
Telefax
+49 6123 9942-50 · [email protected] · www.engelantriebe.de
Operating Manual
Rev. 1.3
Integrated Synchronous Servo Drives
HFI22xx / HFI26xx
HFI32xx / HFI37xx