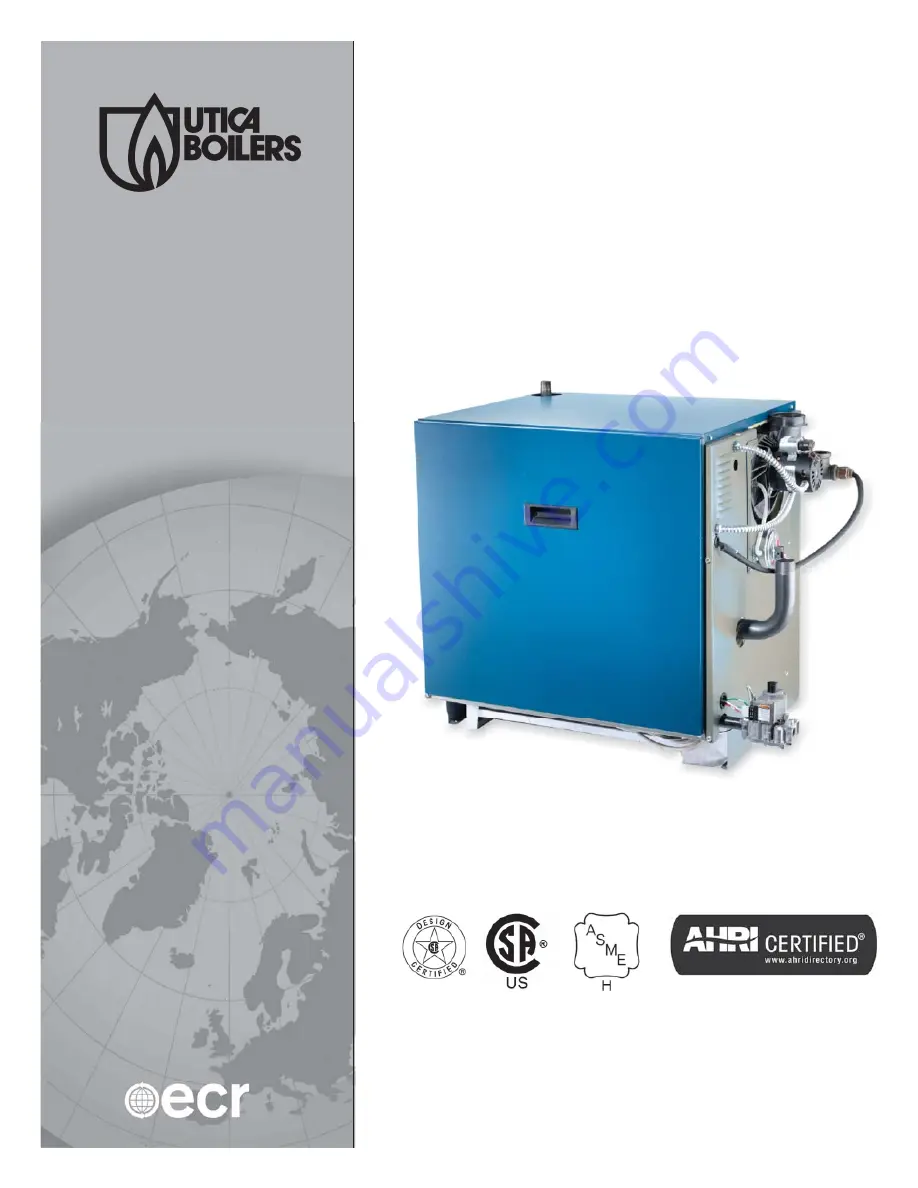
P/N
240009132
, Rev. B [04/2012]
SVB SERIES
II
Gas-Fired Hot Water
Induced Draft Boilers
INSTALLATION, OPERATION &
MAINTENANCE MANUAL
An ISO 9001-2008 Certified Company
Tested for 100 psi. ASME
Working Pressure
C.S.A. Certifi ed for
Natural gas or Propane
Manufactured by:
ECR International, Inc.
2201 Dwyer Avenue, Utica NY 13501
web site: www.ecrinternational.com
Models
SVB-2
SVB-3
SVB-4
SVB-5
SVB-6
SVB-7
Summary of Contents for UTICA BOILERS SVB II Series
Page 23: ...23 WIRING DIAGRAMS Figure 12 Control Module Damper is not an option ...
Page 37: ...Date Service Performed Company Name Tech Initials Company Address Phone ...
Page 38: ...NOTES ...
Page 39: ...Date Service Performed Company Name Tech Initials Company Address Phone ...
Page 40: ...UTICA BOILERS 2201 Dwyer Avenue Utica NY 13501 web site www ecrinternational com ...