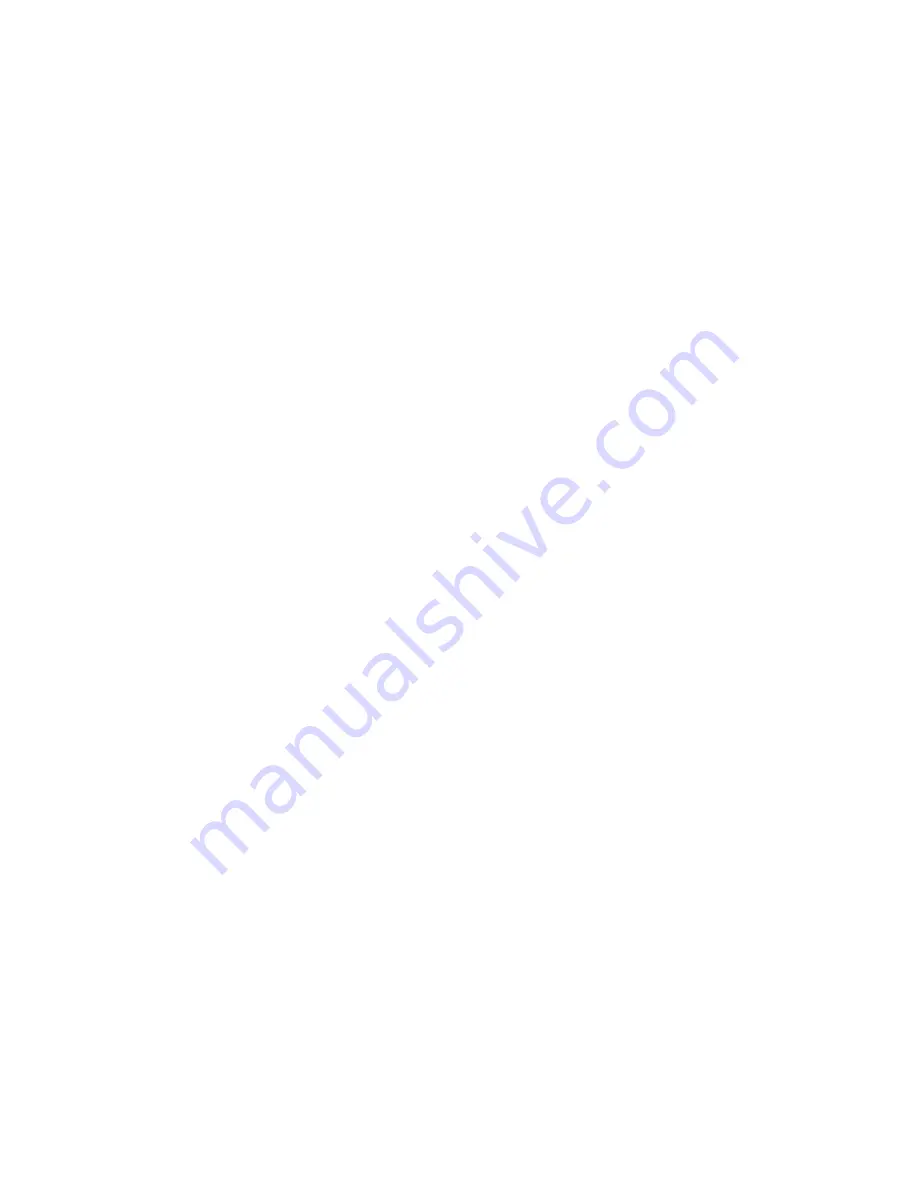
65.99892-8026A Shop Manual
Daewoo reserves the right to improve our products in a continuing process to provide the best possible
product to the market place. These improvements can be implemented at any time with no obligation to
change materials on previously sold products. It is recommended that consumers periodically contact their
distributors for recent documentation on purchased equipment.
This documentation may include attachments and optional equipment that is not available in your
machine’s package. Please call your distributor for additional items that you may require.
Illustrations used throughout this manual are used only as a representation of the actual piece of
equipment, and may vary from the actual item.
Shop Manual
65.99892-8026A
DB58, DB58T &
DB58TI DIESEL
ENGINE
Summary of Contents for DB58
Page 8: ...Cylinder Block Unit kg m 5 5 3 1 2 6 0 5 2 6 0 5 2 6 0 5 2 1 0 5 24 1 1 EJM1002S...
Page 9: ...Oil Pan and Dipstick Unit kg m 6 2 6 0 5 8 0 1 0 2 9 0 3 EJM1003S...
Page 12: ...Thermostat and Thermostat Housing Unit kg m 9 EJM1006S 5 3 1 5 3 1 2 6 0 5...
Page 13: ...Intake and Exhaust Manifold DB58 Unit kg m 10 2 9 0 3 2 6 0 5 EJM1007S...
Page 14: ...Intake and Exhaust Manifold DB58T Unit kg m 11 5 3 1 0 2 6 0 5 EJM1008S...
Page 15: ...Intake and Exhaust Manifold DB58TI Unit kg m 12 EJM1009S 2 9 0 3 2 6 0 5...
Page 18: ...Fuel System DB58 DB58T Unit kg m 15 EJM1012S 1 9 0 2 1 3 0 2 3 1 0 2 1 7 0 1 4 2 0 8 4 2 0 8...
Page 19: ...Fuel System DB58TI Unit kg m 16 EJM1013S 1 9 0 2 1 3 0 2 3 1 0 2 1 7 0 2 4 2 0 8...
Page 34: ...2 ENGINE DISASSEMBLY AND ASSEMBLY 2 1 Engine External Parts DB58 31 EJM2001I...
Page 35: ...DB58T 32 EJM2002I...
Page 36: ...DB58TI 33 EJM2003I...
Page 49: ...46 DB 58T EJM2025S DB 58TI EJM2026S 7 8 9 2 11 3 4 5 10 1 6 7 8 9 2 11 12 3 4 5 10 1 6...
Page 120: ...7 TURBO CHARGER General Description 122 EJM7001S EJM7002S RHB6A RHB7...