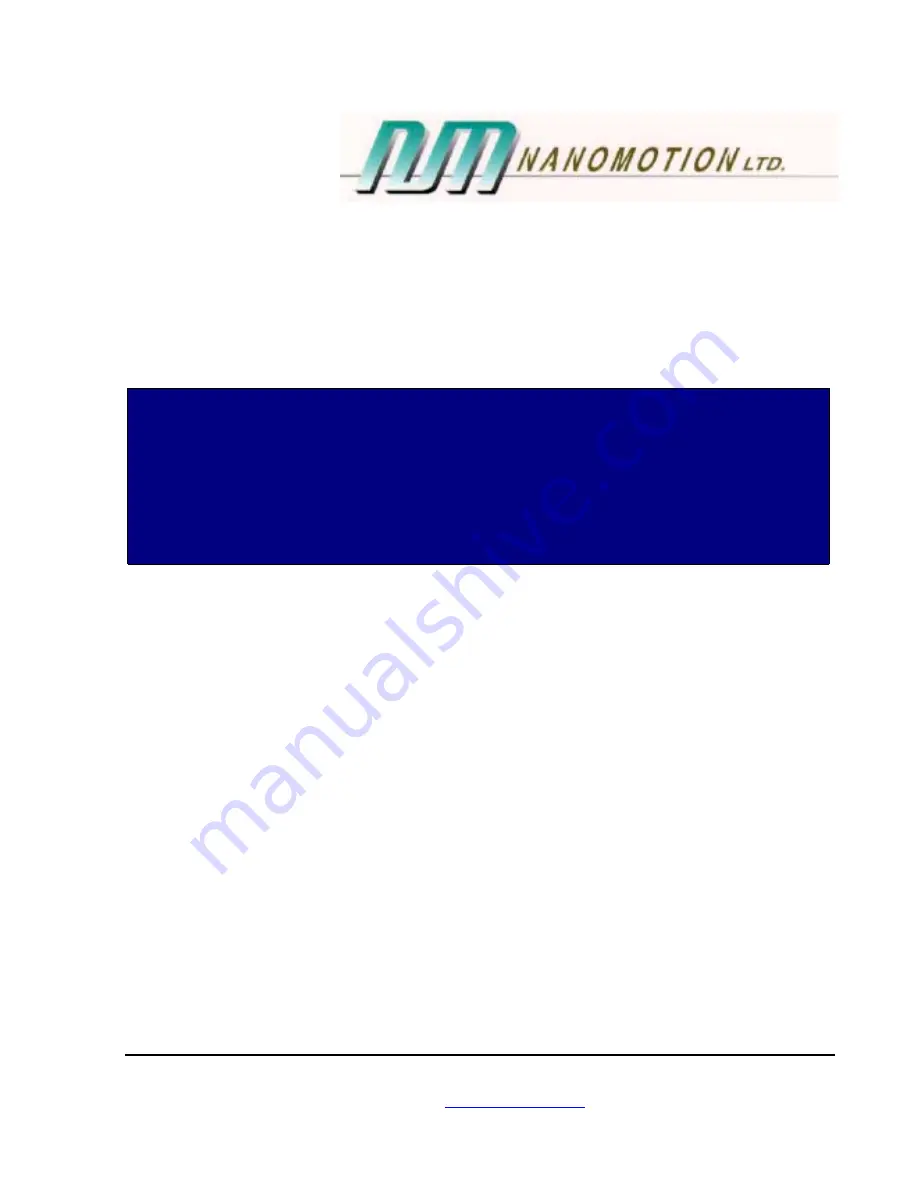
Nanomotion Ltd. POB 223, Yokneam 20692, Israel
Tel: 972-4-959-0862 Fax: 972-4959-0995
Web Site:
www.nanomotion.net
E-mail: [email protected]
HR8
Ultrasonic Motor
User M a n u a l
P/N MSP8-M00-M00-40
Nanomotion Ltd. POB 223, Yokneam 20692, Israel
Tel: 972-4-959-0862 Fax: 972-4959-0995
Web Site:
www.nanomotion.net
E-mail: [email protected]
HR8
Ultrasonic Motor
User M a n u a l
P/N MSP8-M00-M00-40