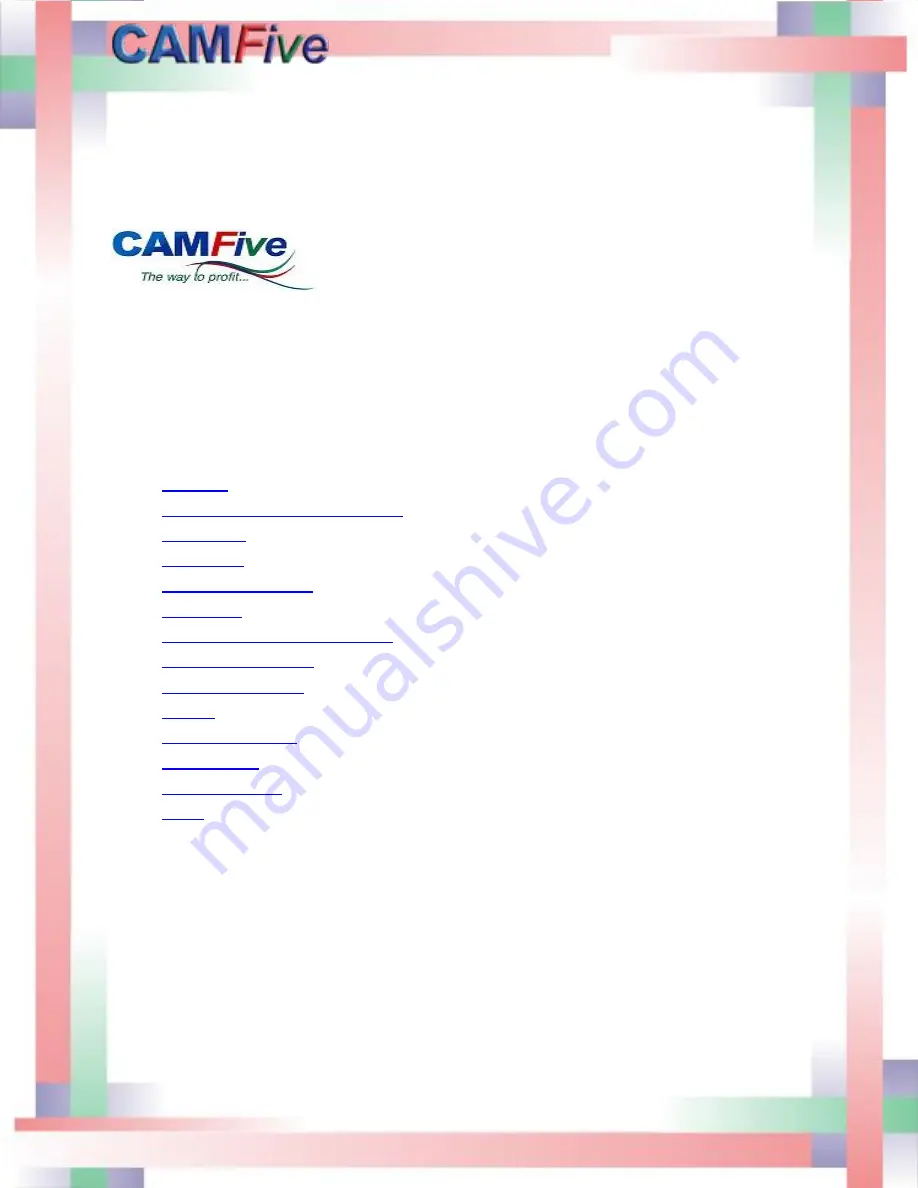
1
USER MANUAL CMA SERIES
INDEX
1.
…………………………………………………………………………………………………..1
2.
Introducctions and requirements
3.
……………………………………………………………………………………………….3
4.
………………………………………………………………………………………………14
5.
……………………………………………………………………………….18
6.
………………………………………………………………………………………………19
7.
Rotary Attacthment installation
8.
……………………………………………………………………………….28
9.
…………………………………………………………………………………33
10.
……………………………………………………………………………………………………37
11.
………………………………………………………………………………….41
12.
………………………………………………………………………………………….44
13.
…………………………………………………………………………………….51
14.
……………………………………………………………………………………………………..55
Summary of Contents for CFL-CMA1610T
Page 4: ...4 ...
Page 6: ...6 ...
Page 12: ...12 The pictures below show the X and the Y step motors ...
Page 29: ...29 Press Next to continue on the following window ...
Page 30: ...30 Proceed to install software ...
Page 31: ...31 Press Finish to complete the software installation Select your language and then click OK ...
Page 32: ...32 The software has been successfully installed the following screen will appear in the PC ...
Page 34: ...34 On the next menu select controller 1 1 1 Next click the CDM20813_Setup option ...
Page 36: ...36 Double click on the SM icon to open the software ...
Page 39: ...39 Send the job to the laser machine with the carve out option Laser at work ...
Page 40: ...40 Final Product ...
Page 45: ...45 Maintenance and replacement of the mirrors ...
Page 46: ...46 Maintenance and replacement of the laser lens First removed the air hose and the nozzle ...
Page 47: ...47 Loosen the adjustment to remove the laser pen ...
Page 48: ...48 Using the ruler provided remove the nut and the o ring that hold the lens in place ...