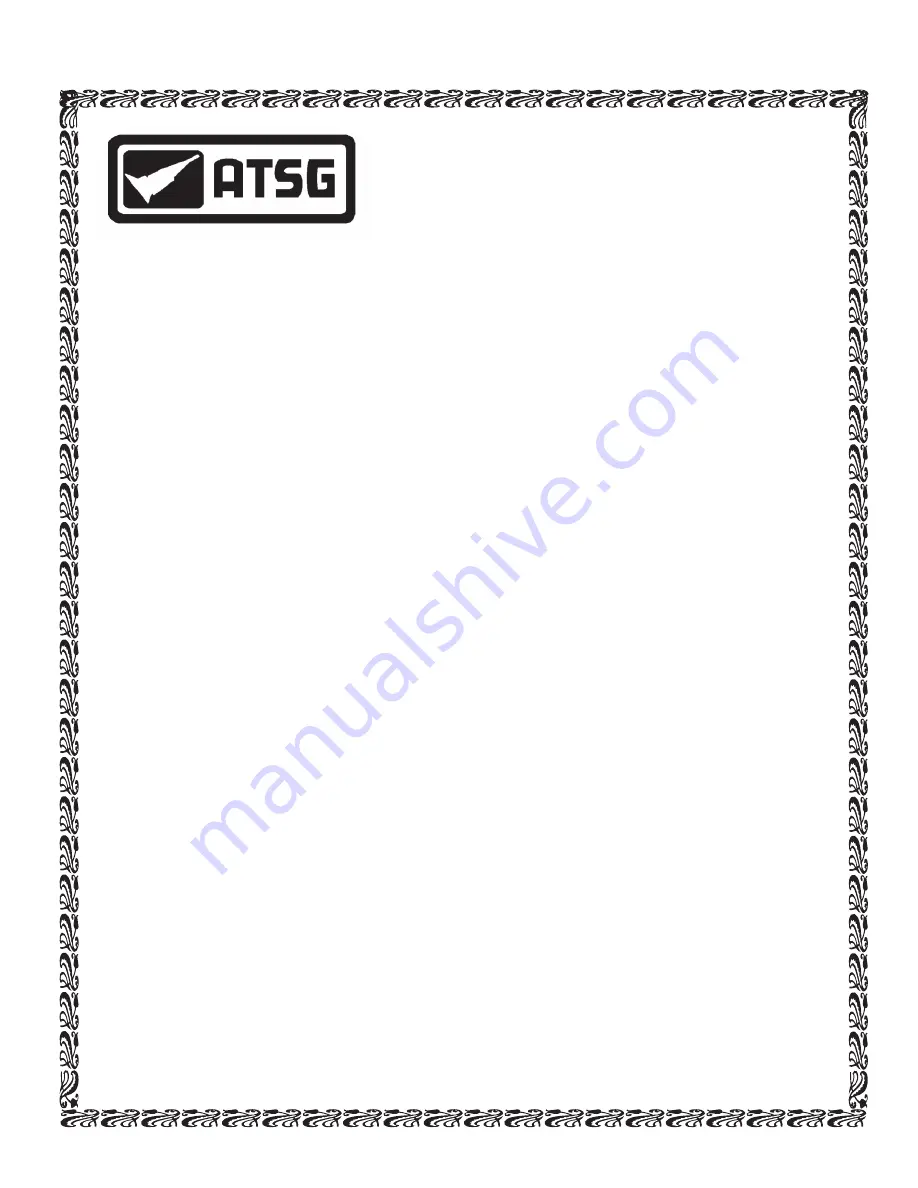
INDEX
Copyright © ATSG 2003
F O R D 4 R 1 0 0
IDENTIFICATION TAG LOCATION AND INFORMATION ............................................................... 3
GENERAL DESCRIPTION AND OPERATION ..................................................................................... 4
COMPONENT AND SOLENOID APPLICATION CHART ................................................................... 5
"PTO" GENERAL REQUIREMENTS .................................................................................................... 6
ELECTRICAL COMPONENT DIAGNOSIS ........................................................................................... 8
FLUID REQUIREMENTS ....................................................................................................................... 12
SOLENOID PACK TESTING .................................................................................................................. 12
ABBREVIATION DESCRIPTION .......................................................................................................... 14
DIAGNOSTIC TROUBLE CODE CHART AND DESCRIPTION ........................................................ 15
LINE PRESSURE TEST .......................................................................................................................... 21
NON-PTO AND PTO HYDRAULIC DIFFERENCES ........................................................................... 22
PWM AND NON-PWM OIL PUMP DIFFERENCES ........................................................................... 34
CASE CHECKBALL LOCATIONS ......................................................................................................... 38
VALVE BODY CHECKBALL LOCATIONS ........................................................................................... 39
AIR PRESSURE CHECKS ...................................................................................................................... 40
TRANSMISSION DISASSEMBLY ......................................................................................................... 41
COMPONENT REBUILD SECTION
TRANSMISSION CASE ASSEMBLY ................................................................................................ 55
FRONT AND REAR PLANETARY CARRIERS ............................................................................... 64
FORWARD CLUTCH HOUSING ...................................................................................................... 66
DIRECT CLUTCH HOUSING ........................................................................................................... 69
FORWARD, DIRECT, SUN SHELL SUB-ASSEMBLY .................................................................... 76
CENTER SUPPORT ASSEMBLY ...................................................................................................... 80
INTERMEDIATE/OVERDRIVE CYLINDER ASSEMBLY ............................................................. 82
OVERDRIVE GEARSET ASSEMBLY ............................................................................................... 84
COAST CLUTCH HOUSING DIFFERENCES ................................................................................ 88
COAST CLUTCH HOUSING ASSEMBLY ........................................................................................ 90
OIL PUMP ASSEMBLY ...................................................................................................................... 94
VALVE BODY ASSEMBLY ............................................................................................................... 100
TRANSMISSION FINAL ASSEMBLY ................................................................................................. 102
MANUAL VALVE CHECK .................................................................................................................... 111
MANUAL SHIFT LEVER DIFFERENCES ........................................................................................ 112
TORQUE SPECIFICATIONS ............................................................................................................... 115
VALVE BODY BOLT CHART AND IDENTIFICATION .................................................................... 116
BOLT CHART AND IDENTIFICATION ............................................................................................. 117
SPECIAL SERVICE TOOLS ................................................................................................................. 118
AUTOMATIC
TRANSMISSION
SERVICE
GROUP
18639 S.W. 107TH AVENUE
MIAMI, FLORIDA 33157
(305) 670-4161
Summary of Contents for FORD 4R100
Page 118: ...AUTOMATIC TRANSMISSION SERVICE GROUP Technical Service Information 118 Copyright 2003 ATSG...
Page 119: ...AUTOMATIC TRANSMISSION SERVICE GROUP Technical Service Information 119 Copyright 2003 ATSG...
Page 120: ...AUTOMATIC TRANSMISSION SERVICE GROUP Technical Service Information 120 Copyright 2003 ATSG...