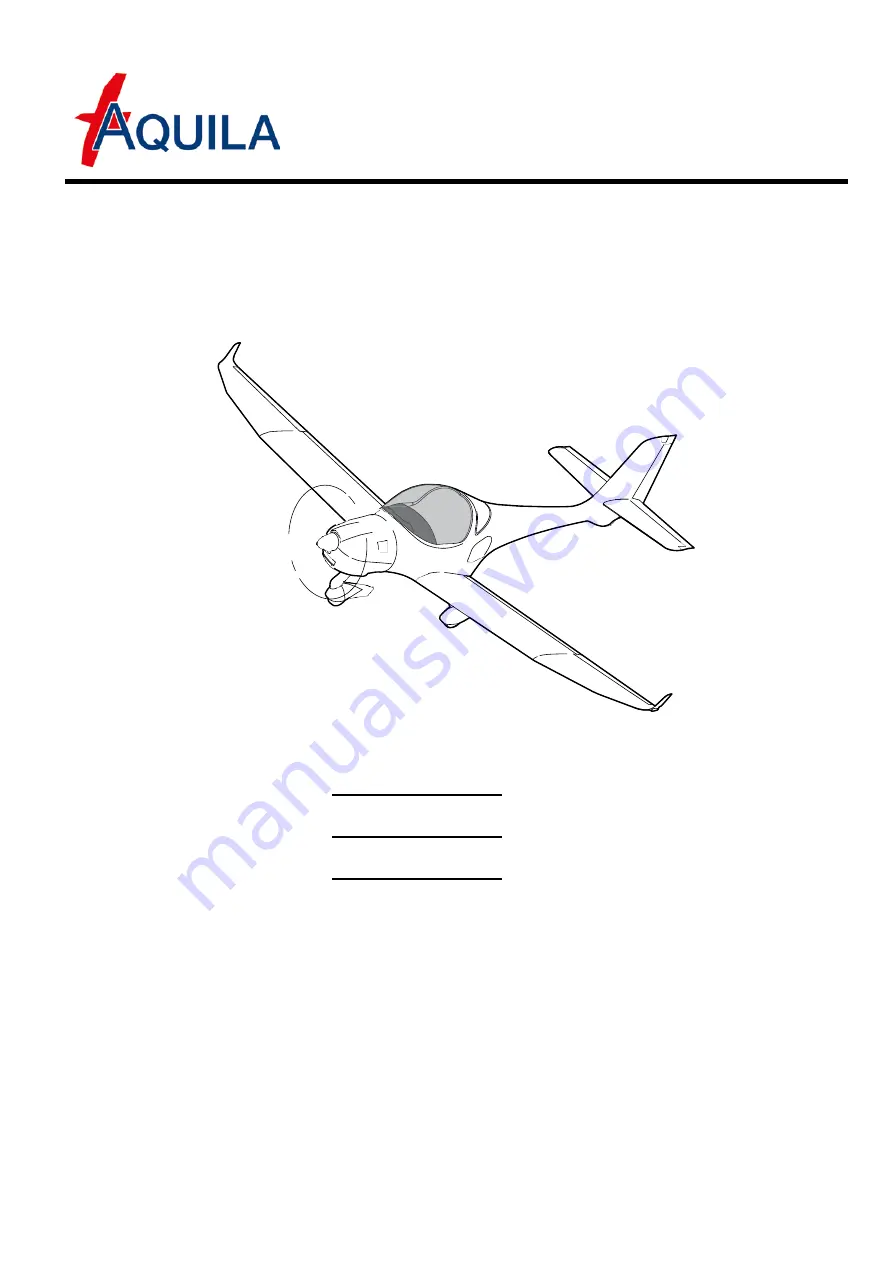
PILOT’S OPERATING HANDBOOK
AQUILA A212 GX
Type / Model:
AQUILA AT01-200
Serial Number:
AT01-200C-
Registration:
Document Number:
FM-AT01-1010-106
First Issue:
02.03.2020
Certified according to:
JAR-VLA
This Pilot's Operating Handbook (POH) must be carried on board the aircraft at all times.
The amendment history and revision status are provided in the list of effective pages and in
the list of revisions.
The aircraft must be operated in compliance with the procedures and operating limits stated
herein.