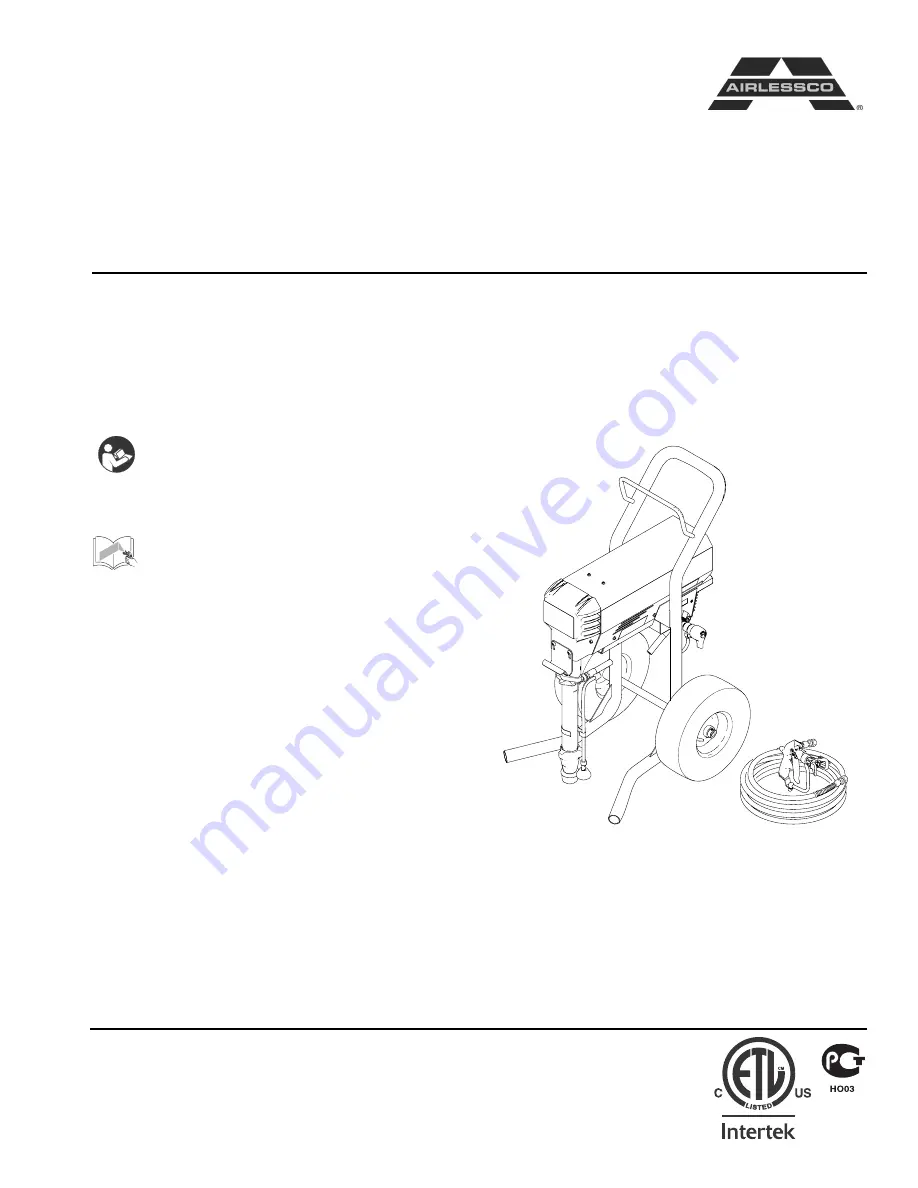
3A1183C
EN
Operation/Repair/Parts
Airless Paint Sprayer
For application of architectural paints and coatings. For professional use only.
Airlessco - TS1500 (24F573) Series B
3300 psi (22.8 MPa, 228 bar) Maximum Working Pressure
Related Manuals
Important Safety Instructions
Read all warnings and instructions in this
manual. Save these instructions.
Gun Manual 3A0413
ti17342a