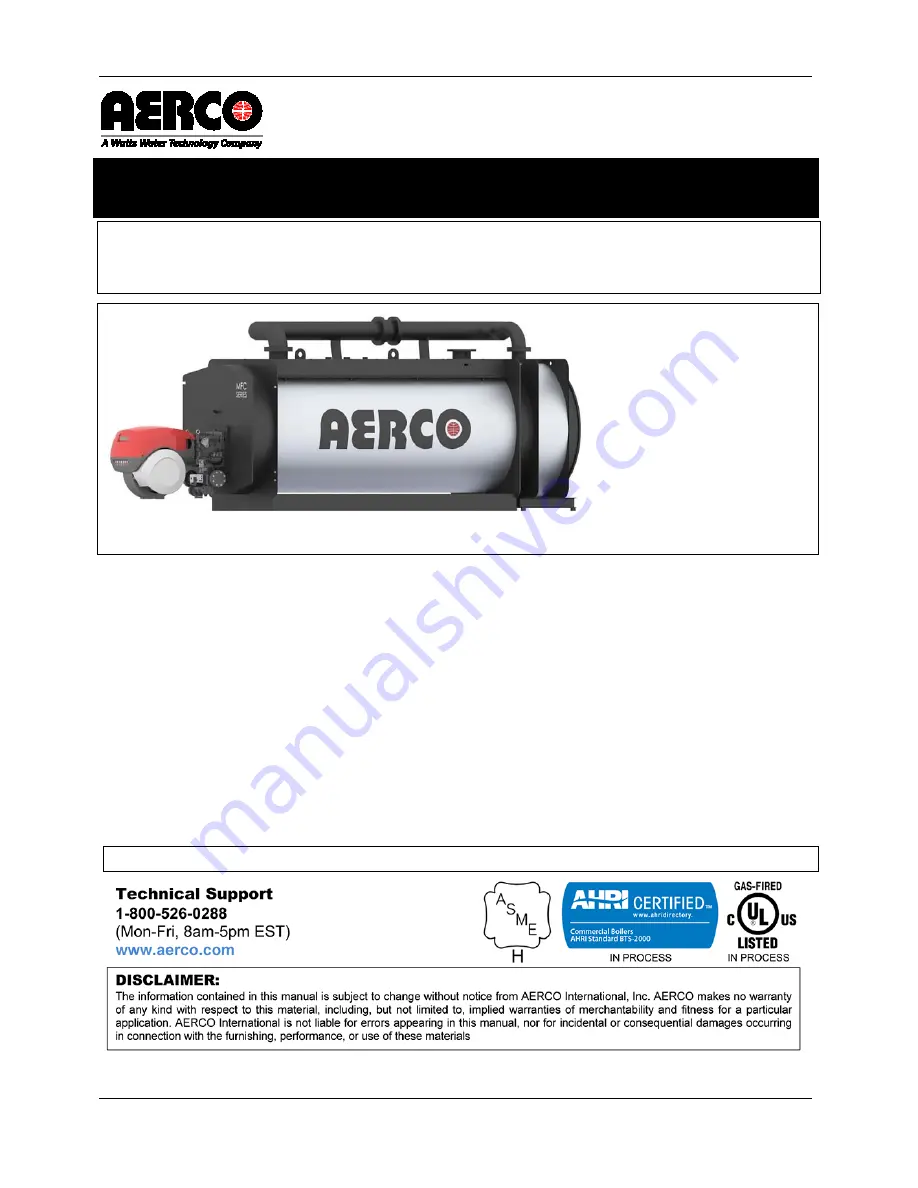
MFC Series Boilers User Manual
OMM-0104_94
AERCO International, Inc.
•
100 Oritani Dr.
•
Blauvelt, NY 10913
Page
1
of
170
GF-146
Ph.: 800-526-0288
12/29/2015
USER MANUAL
Installation, Operation and Maintenance of:
MFC Series
Multi-Fuel Condensing Boilers
MFC 10000
Applies to MFC Series Models:
•
MFC 3000
•
MFC 4000
•
MFC 5000
•
MFC 6000
•
MFC 8000
•
MFC 10000
NOTE:
Refer to the AERCO
MFC Series Installation Manual, GF-146-IN
, for preliminary
assembly and installation instructions and information.
Latest Update: 12/29/2015