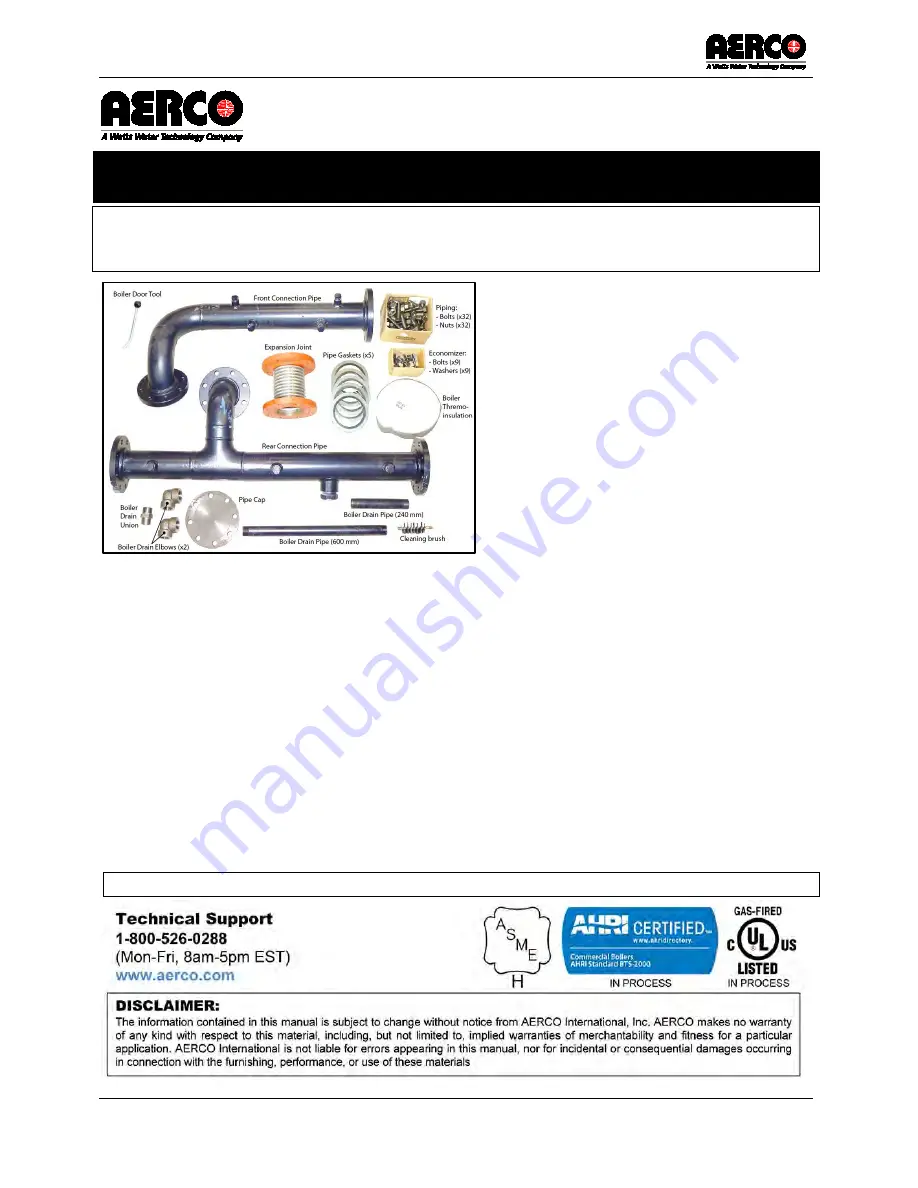
MFC Series Boilers Installation Manual
INSTALLATION MANUAL
For Preliminary Assembly and Installation of:
MFC Series
Multi-Fuel Condensing Boilers
Applies to MFC Series Models:
•
MFC 3000
•
MFC 4000
•
MFC 5000
•
MFC 6000
•
MFC 8000
•
MFC 10000
NOTE:
Refer to the AERCO
MFC Series User Manual, GF-146
, for complete Installation,
Operation, and Maintenance instructions and information.
Latest Update: 12/15/2015
OMM-0108_0A
AERCO International, Inc.
•
100 Oritani Dr.
•
Blauvelt, NY 10913
Page
1
of
32
GF-146-IN
Ph.: 800-526-0288
12/15/2015