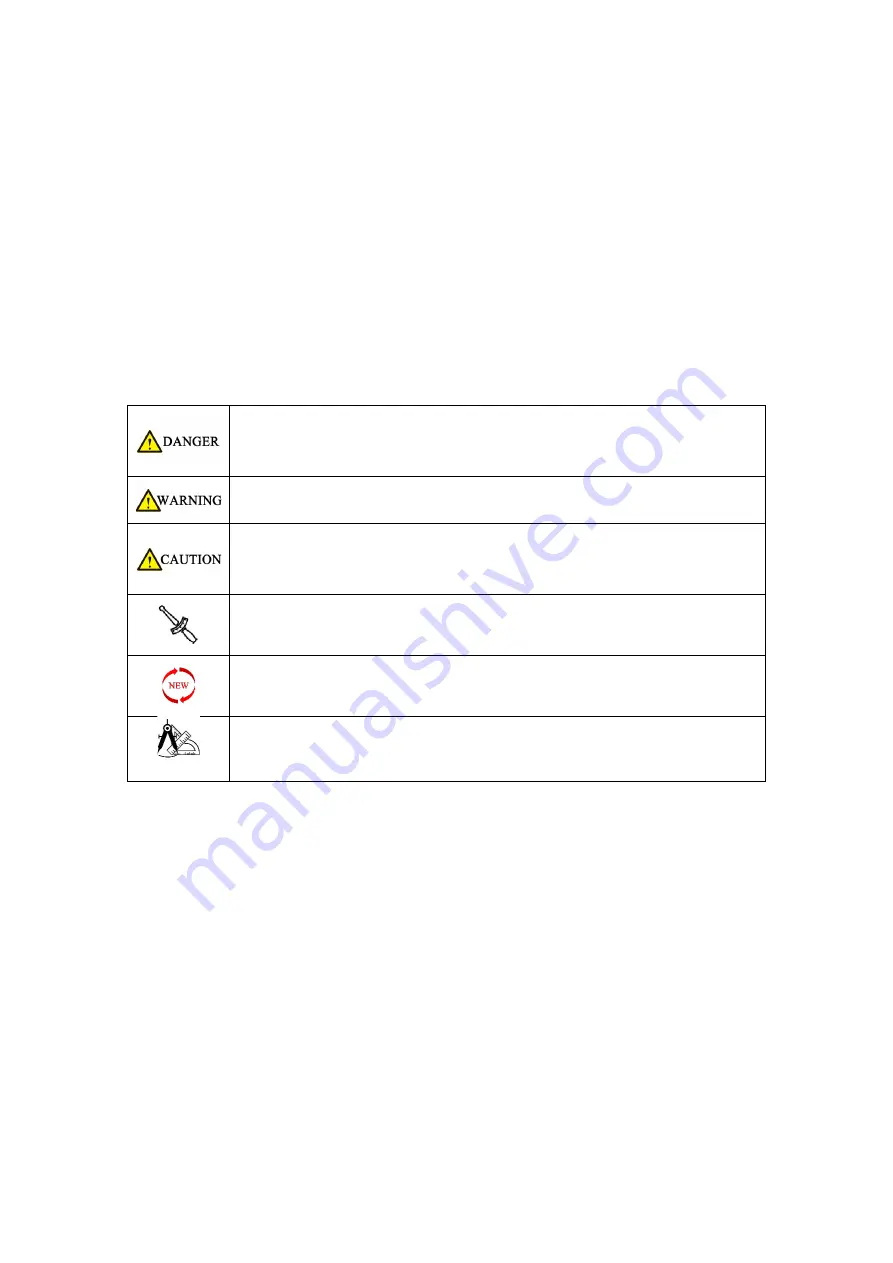
User notice
This manual is compiled by Guangdong Tayo Motorcycle Technology Co., Ltd. to guide dealers or service
personnel to use it. This manual cannot provide more detailed knowledge about motorcycles, and is only for reference
for maintenance. If you do not have the corresponding knowledge such as electrician, machine repair, etc., improper
assembly or repair failure may occur during repair.
If you need to clean or wash the body parts of the vehicle, you should use neutral car wash fluid or tap water,
diesel, kerosene, etc. Acidic or alkaline car wash liquid will cause irreversible corrosion of the surface paint,
electroplating surface, and anodized surface of the parts; gasoline will cause premature aging or hardening of
sealants, gaskets, and rubber parts, reducing the service life. Non-woven fabrics should be used for wiping with no
residue. Ordinary rags may leave cloth scraps or wool, etc., which may affect the assembly or cause other adverse
effects.
Our company will update this manual as soon as possible after the product changes.
The following is the meaning of the icons marked in this manual
:
Failure to observe will cause personal injury or death of the driver or
maintenance personnel; or cause serious damage to parts and shorten the
service life, etc.
Failure to comply may result in personal injury or death of the driver or
maintenance personnel; or damage to parts, abnormalities, etc.
Failure to observe the warning will cause personal injury to the driver or
maintenance personnel; or matters requiring special attention during
disassembly and assembly
Indicates that there is a requirement for torque there
Indicates that the piece needs to be replaced after disassembly
Indicates that a measurement is required at this location
Summary of Contents for ZT310M 2022
Page 1: ...ZT310T M Engine maintenance Manual 2022 02 11...
Page 6: ...Lubrication system One Lubrication system diagram...
Page 7: ......
Page 31: ...Cylinder piston One System components 6 7 5 8 9 10 3 2 1 4 11 12 13...
Page 56: ...Right crankcase cover magneto One System components Part information...
Page 70: ...Gearbox One System Components 12 1 3 2 4 6 9 10 5 7 8 13 14 15 16 17 19 18 11 20...