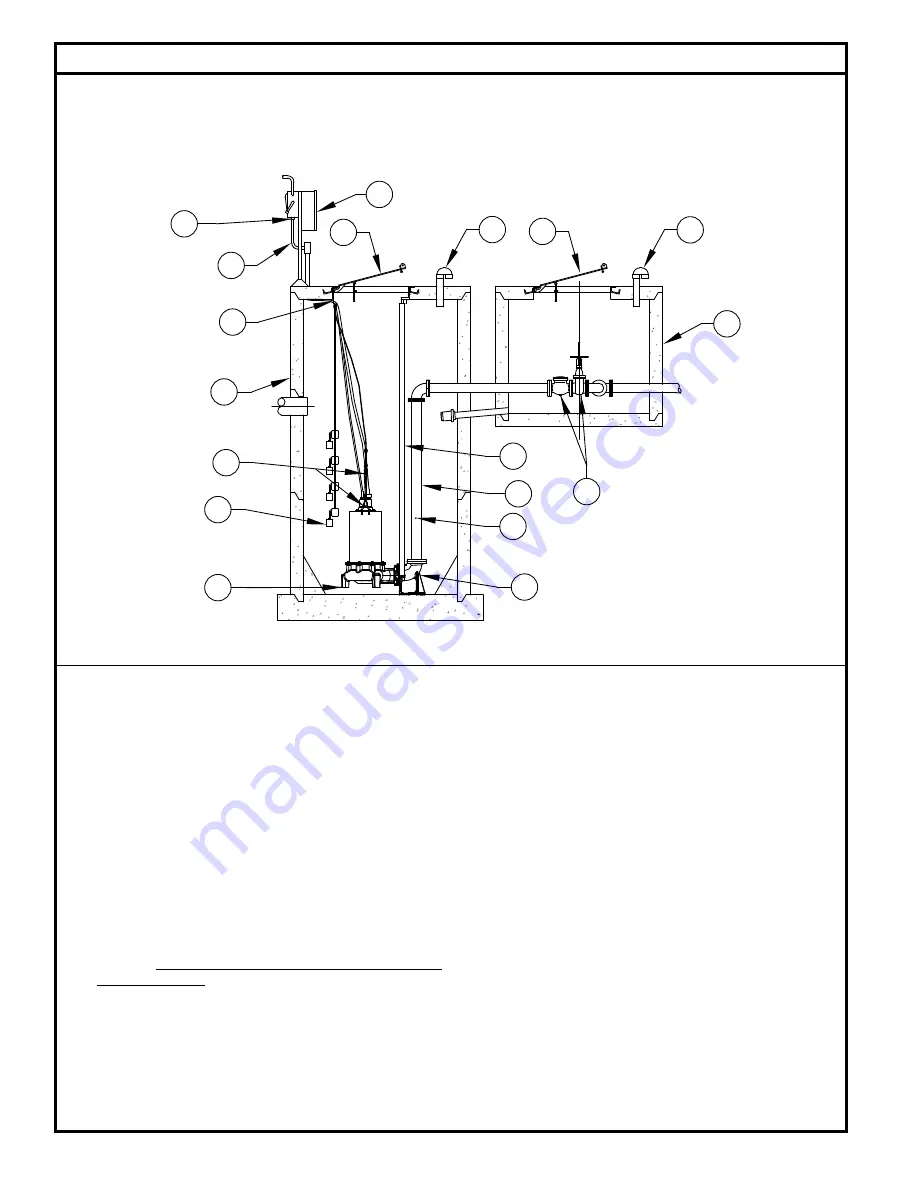
4
© Copyright 2017 Zoeller
®
Co. All rights reserved.
All installations must comply with all applicable electrical and plumbing codes, including, but not limited to, National Electrical Code,
local, regional, and/or state plumbing codes, etc.
TYPICAL OUTDOOR CONCRETE BASIN WITH VALVE BOX AND HINGED ACCESS COVERS
Typical Sewage/Waste Pumping System Installation
(1) Electrical wiring and protection
must
be in accordance with the
National Electrical Code, and any other applicable state and local
electrical requirements.
(2) Install proper full flow check and shut-off valve.
(3) Install proper controls. (Outdoor panels
require
NEMA 3R or 4X
enclosure)
(4) All installations
require
a basin cover to prevent debris from falling
into the basin and to prevent accidental injury.
(5) Gas tight seals are
required in all indoor sewage installations
to contain gases and odors.
(6)
When check valve is installed, drill a 3/16” diameter hole in
the discharge pipe below the check valve even with the top of
the pump. NOTE: The hole must be below the basin cover and
cleaned periodically. Water stream will be visible from this hole
during pump run periods. Also a vent hole is drilled in the pump
housing. Be sure that this hole is cleared during any servicing.
(7) Vent gases and odors to the atmosphere through vent pipe per
Local and State codes.
(8) Secure power cord to avoid entanglement with variable level float
switch mechanism.
(9)
Do not reduce pump discharge pipe below 4” IPS size.
(10) Basin
must
be in accordance with all applicable codes
and specifications. Basin must be sized to allow a minimum 3
minute lapse time between starts.
(11) Pump must be level and the tethered variable level float switch
must be free and not hang up on pump or pit peculiarities.
(12)
If
a rail system is used, discharge elbow
must be firmly anchored
to the bottom of basin. In fiberglass basin, the bottom will need
to be reinforced if the discharge elbow is used.
(13)
If a rail system is used, the guide rails are 2” schedule 40 pipe
for flanged horizontal discharge units. Brass, stainless steel or
galvanized steel is recommended.
(14) Install ring and cable for lifting pump from pit.
(15) Basin must be clean and free of debris after installation.
(16) Cords must be properly sealed to prevent moisture and gases
from entering the control panel.
ZEPA0071_6680
9
10
16
1
8
4
3
4
7
10
7
15
14
11
12
13
2
6