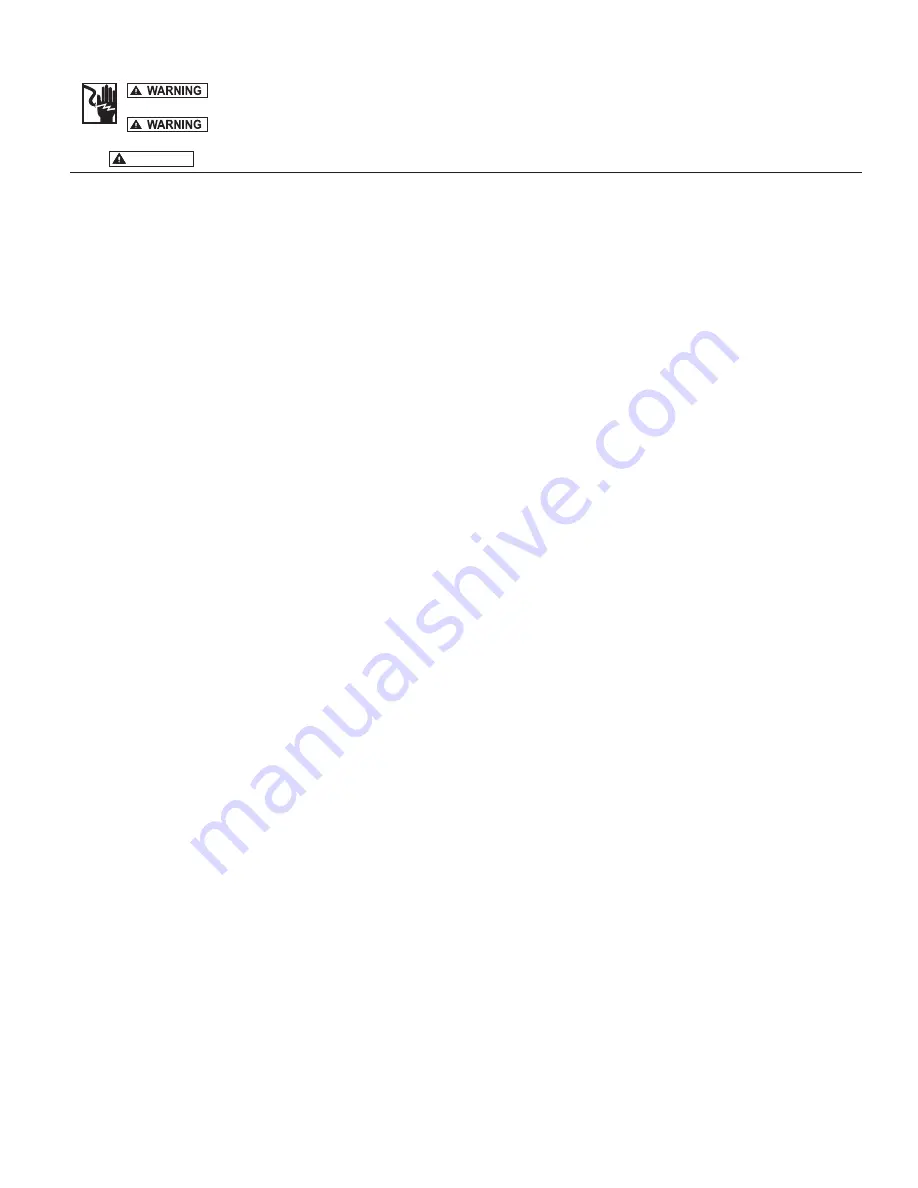
5
© Copyright 2019 Zoeller
®
Co. All rights reserved.
Installation and checking of electrical circuits and hardware should be performed by a qualified licensed electrician.
RISK OF ELECTRICAL SHOCK
Do not remove power supply cord and strain relief or connect conduit directly to the pump.
CAUTION
Power cords, sensor cords, and float cords all must be sealed to prevent gases from the basin entering the control panel.
INSTRUCTIONS FOR CHECKING ROTATION OF THREE PHASE UNITS
It is very important that these units be connected for proper rotation. Since no rotating parts are visible without removing the pump
from the pit, the rotation on 3 phase units should be checked before installation into the pit as follows:
After the proper electrical connections are made, momentarily energize the pump observing the direction of kick back due to
starting torque. The rotation is correct if the kick back is in the opposite direction of the rotation arrow. If the rotation is not
correct, disconnect power and switch any two power leads. Turn power back on and retest for proper rotation. If uncertain, the
pump will draw the fewest amps when rotating in the proper direction. Directional arrows are also found on the pump housing.
MOISTURE SENSORS (OPTIONAL FEATURE)
(1) Pumps with moisture sensors will have a separate small diameter sensor cord in addition to the power cord.
(2) Sensor cord conductor wires are connected to sensor probes in the lower seal cavity and cap assembly. The conductor
wires are terminated in the control panel for activating an indicator light when moisture is present in the lower seal cavity,
motor cavity or cord cap assembly.
(3) When the moisture indicator light is activated the pump should be serviced within 30 days to avoid damage to the motor
and bearings.
(4) Oil in the motor housing and lower seal cavity should be checked when pump is serviced. If oil from the motor housing
contains water or other contamination, both seals should be replaced during maintenance. Always replace with new factory
recommended oil and service parts. All warranty repairs must be made by Zoeller Authorized Service Stations.
(5) On existing applications where the control panel only has one moisture sensor hookup per pump, one moisture sensor lead
from the pump should be hooked to the moisture sensor lead in the panel, the other moisture sensor lead from the pump
should be hooked to ground to complete the circuit.
(6) The moisture sensor circuit can be checked for continuity (complete circuit) with a (Volt-OHM-Meter). Set the VOM to read
resistance and connect the VOM leads to the sensor cord black and white wires. The VOM should read approximately 330k
Ohms when the pump is moisture free. Resistance readings significantly lower indicates that moisture has entered into
the pump assembly. If VOM reading is open, a problem exists with moisture sensor circuit. Check resistance between the
green ground conductor of the pump power cord and the sensor cord black and white wires where the resistance reading
should indicate an open circuit. If VOM reading returns a reading other than open, then a problem exists and the pump
should be taken to a Zoeller Authorized Service Station.
PUMPS WITHOUT MOISTURE SENSORS
(1) Double seal pumps offer additional motor protection, but sensor probes are optional.
(2) Pumps without sensor probes should be inspected on a periodic preventative maintenance schedule.
(3) The oil in the motor housing and lower seal cavity should be checked when pump is serviced. If oil contains water or other
contaminations, both seals and oil should be replaced during maintenance. Always replace with new factory recommended
oil and service parts. All warranty repairs must be made by Zoeller Authorized Service Stations.
CONTROL PANELS
These pumps are nonautomatic. They require a control panel. A motor starter circuit, control circuit, and alarm circuit within
the panel are
standard features. Outdoor enclosures and alternating relays are often required. Variable level float switches are
the most common level sensing device. The following should be noted:
3 phase pumps require overload protection in panel. Use with approved motor control that matches motor input in full load amperes with
overload element(s) selected or adjusted in accordance with control instructions.
PUMP WIRING INSTRUCTIONS