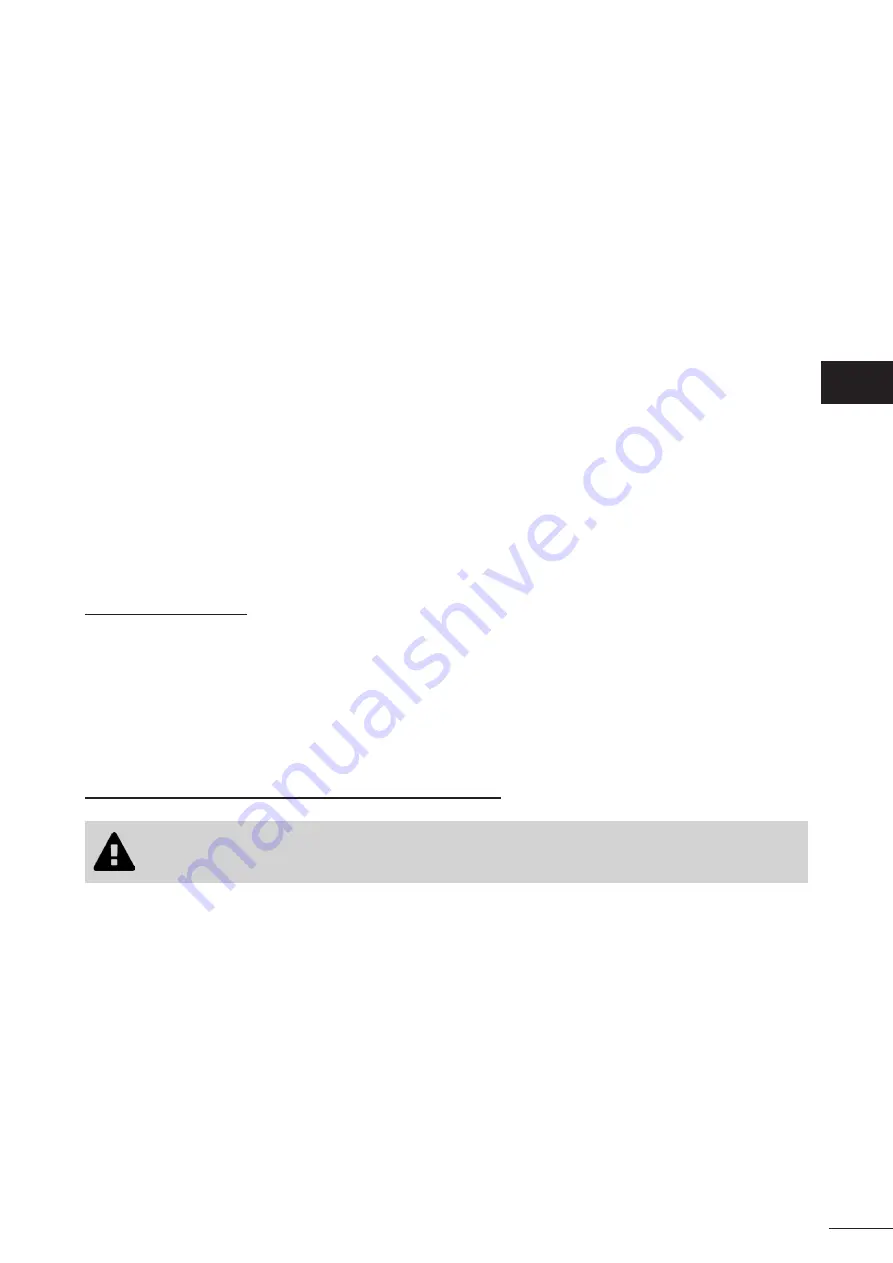
17
•
In addition to conventional charging procedures, the following requirements apply.
- Check that there is no possibility of cross-contamination between the different refrigerants when using charging
equipment. Hoses or lines must be as short as possible to reduce the quantity of refrigerant contained therein.
- Cylinders must be kept in an appropriate position, in accordance with the instructions.
- Check that the cooling system is grounded before charging the system with refrigerant.
- Label the system once charging is complete (if this is not already the case).
- Pay close attention to not overfilling the cooling system.
•
Before recharging the system, carry out a pressure test using a suitable purge gas. The system must be examined to
make sure there are no leaks after the charging operation and before commissioning. A follow-up leak test must be
carried out before leaving the site.
Dismantling
•
Before dismantling, the technician must familiarise himself/herself with the equipment and its specifications. We
highly recommend carefully recovering all refrigerants. Before this, oil and refrigerant samples must be taken if
analyses are to be carried out before any other use of the recovered refrigerant. Check for the presence of a power
supply before starting work.
1. Familiarise yourself with the equipment and how it operates.
2. Electrically isolate the system.
3. Before starting work, check the following points:
- mechanical handling equipment is available if needed to handle the refrigerant cylinders;
- all personal protective equipment is available and used correctly;
- the recovery process is monitored at all times by a cognisant person;
- the recovery cylinders and equipment comply with the relevant standards.
4. Drain the cooling system where possible.
5. If a vacuum cannot be created, install a manifold in order to be able to remove the refrigerant from various locations
within the system.
6. Make sure that the cylinder is located on the scales before starting recovery operations.
7. Start the recovery unit and operate as per its instructions.
8. Do not overfill the cylinders (no more than 80% of the volume must be filled with liquid).
9. Do not exceed the maximum working pressure of the cylinder, even temporarily.
10. When the cylinders have been filled correctly and the process is complete, check that the cylinders and the
equipment are quickly removed from the site and that the alternative shut-off valves on the equipment are closed.
11. The recovered refrigerant must not be charged in another cooling system, unless it has been cleaned and inspected.
4.2.2 User maintenance
•
Make sure that the filter is not blocked by any foreign bodies.
•
Clean the evaporator (for location see § “1.3 I Dimensions and marking”) using a soft brush and a fresh water spray
(disconnect the power cable); do not fold over the metal wings, then clean the condensation drainage pipe to remove
any impurities that may be blocking it.
•
Do not use a high pressure jet. Do not spray with rain water, salt water or water which is full of minerals.
•
Clean the outside of the device; do not use any solvent-based products. We can provide you with a specific cleaning
kit as an accessory: the PAC NET, see § “1.1 I Description”.
4.2.3 Maintenance to be carried out by a qualified technician
•
Please read the safety instructions provided in the chapter entitled «4.2.1 Safety instructions
for appliances containing R32 refrigerant» before performing any of the maintenance
operations described below.
•
Check that the regulation is operating correctly connected.
•
Check that the condensation flows correctly when the device is operating.
•
Check the safety mechanisms.
•
Check the connection of the metal masses to the earth.
•
Check that the electrical cables are correctly tightened and connected and that the electrical unit is clean.
EN