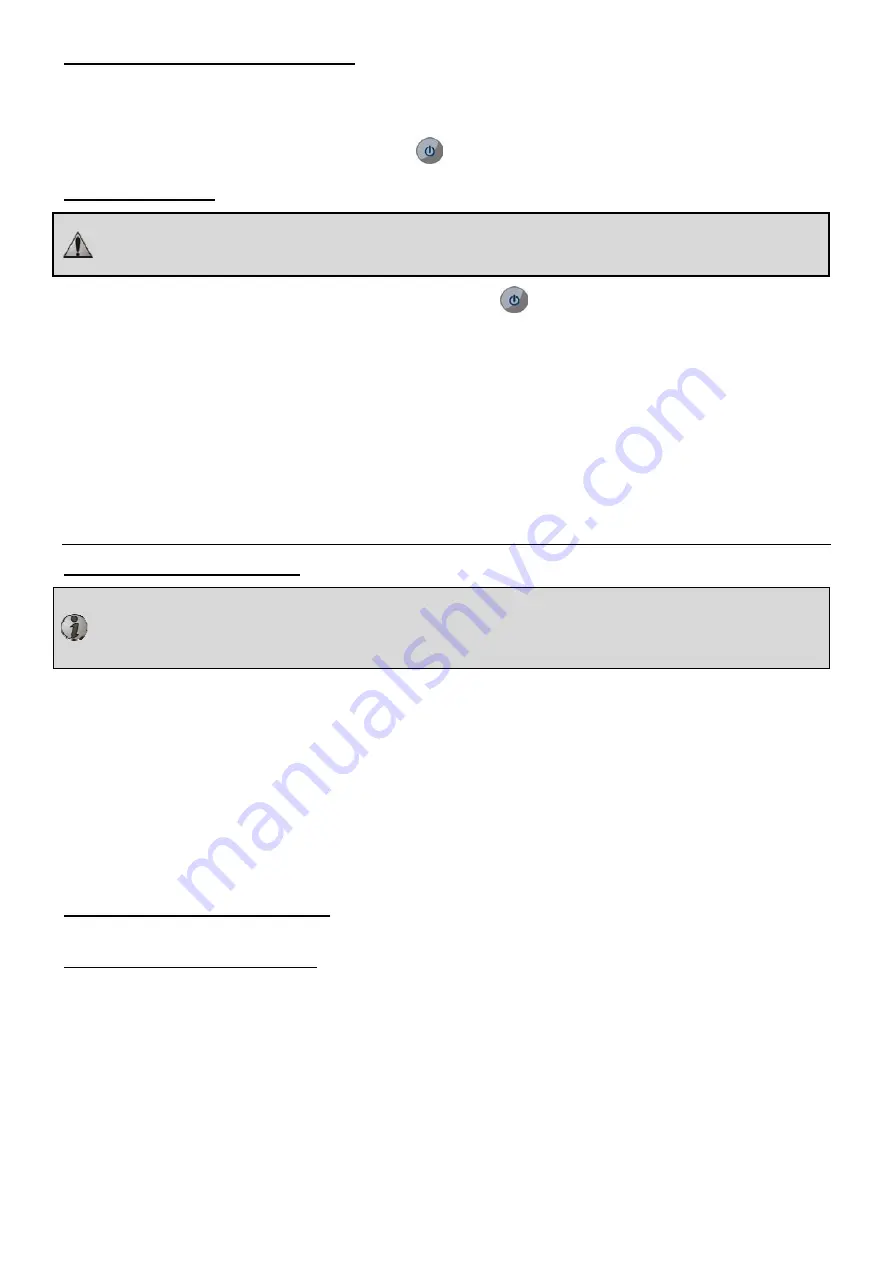
H03619
‐
00.D1.EN
–
2012/03
8
3.3
Checks
to
perform
after
start
‐
up
The
heat
pump
must
stop
when:
the
set
‐
point
temperature
is
lowered
using
the
digital
control
panel,
filtering
is
stopped
or
valve
2
or
3
is
closed
3,
the
digital
control
panel
is
turned
off
by
pressing
,
3.4
Winter
storage
Winter
storage
is
essential
due
to
the
risk
of
the
condenser
freezing
and
breaking.
This
situation
is
not
covered
by
the
warranty.
To
avoid
damaging
the
device
with
condensation,
do
not
cover
it
with
an
air
‐
tight
cover.
switch
the
digital
control
panel
to
"stand
‐
by"
mode
by
pressing
for
3
seconds,
open
valve
1,
close
valves
2
and
3,
and
open
valves
4
and
5
(if
fitted),
ensure
that
no
water
is
flowing
through
the
heat
pump,
drain
the
water
condenser
(
risk
of
freezing
)
by
unscrewing
the
two
pool
water
inlet
and
outlet
connections
at
the
back
of
the
heat
pump,
in
the
case
of
full
winter
storage
conditions
for
the
pool:
re
‐
connect
the
inlet
and
outlet
connections
to
avoid
foreign
bodies
entering
into
the
condenser,
in
the
case
of
winter
storage
for
the
heat
pump
alone:
do
not
reconnect
the
inlet
and
outlet
connectors,
instead
place
two
plugs
(supplied)
on
the
condenser
water
inlet
and
outlet.
4.
Maintenance
4.1
Maintenance
instructions
It
is
recommended
that
the
device
be
general
serviced
on
a
yearly
basis
to
ensure
proper
operation,
maintain
performance
levels
and
prevent
some
potential
failures.
This
is
the
responsibility
of
the
user
and
must
be
performed
by
a
qualified
technician.
Do
not
use
a
high
‐
pressure
water
hose.
ensure
no
foreign
bodies
obstruct
the
fan
grid.
clean
the
evaporator
with
a
soft
brush
and
a
fresh
water
jet
(disconnect
the
power
cable),
do
not
twist
or
bend
the
metal
blades,
clean
the
outside
of
the
unit
with
a
solvent
‐
free
product.
A
specific
PAC
NET
cleaning
kit
is
available
as
an
optional
extra
(see
§4.3),
check
that
the
water
condensation
flows
out
properly
during
the
operation
of
the
device.
check
the
proper
operation
of
the
regulator,
check
electrical
components,
check
that
all
metal
elements
are
grounded,
check
the
tightening
and
connections
of
electric
cables
and
the
cleanliness
of
the
electrical
compartment.
4.2
Additional
recommendations
in
relation
to
the
Pressure
Equipment
Directive
(PED
‐
97/23/EC)
4.2.1
Installation
and
maintenance
the
unit
may
not
be
installed
close
to
combustible
materials,
or
the
air
duct
inlet
of
an
adjacent
building
.
with
some
devices,
it
is
essential
to
fit
protection
grids
if
the
unit
is
installed
in
an
area
with
uncontrolled
access.
during
installation,
troubleshooting
and
maintenance,
pipes
may
not
be
used
as
steps:
the
pipe
could
break
under
the
weight,
spilling
refrigerant
and
possibly
causing
serious
burns.
when
servicing
the
appliance,
the
composition
and
state
of
heat
carrying
fluid
must
be
checked,
as
well
as
the
absence
of
any
refrigerant.
during
the
annual
unit
sealing
test
in
accordance
with
applicable
legislation,
the
high
and
low
pressure
switches
must
be
checked
to
ensure
that
they
are
securely
fastened
to
the
coolant
circuit
and
that
they
cutoff
the
electrical
circuit
when
tripped.
during
maintenance
work,
ensure
there
are
no
traces
of
corrosion
or
oil
around
cooling
components.