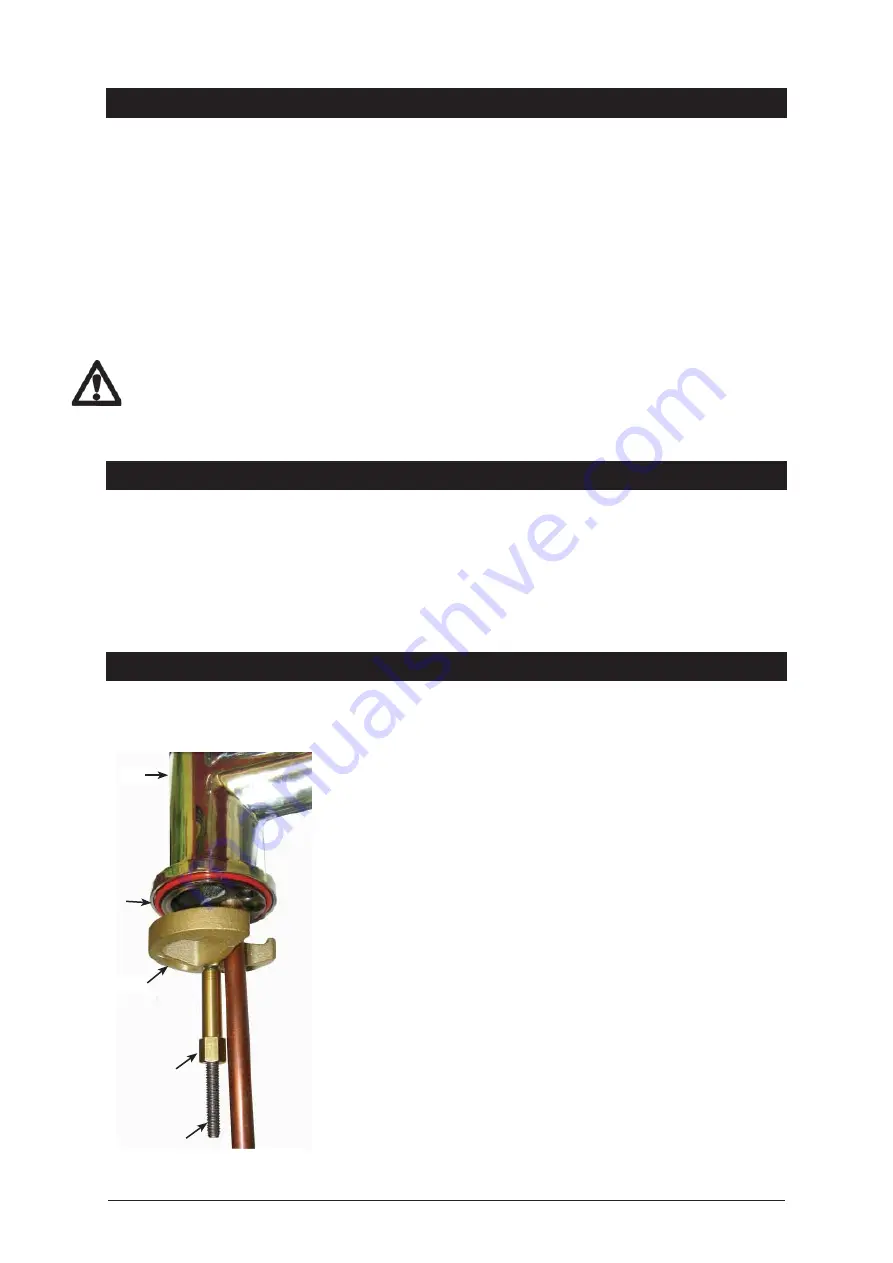
HydroTap Installation and Operating Instructions
Page 5 of 20
In addition to normal tools, the following will be required:
• 50mm diameter sheet metal hole punch for sink tops. (not supplied)
• 50mm diameter hole saw for timber bench tops. (not supplied)
• Nut runner tube spanner (supplied) for fixing tap assembly.
Special tools required
Step A - Installing the (Boiling / Chilled) HydroTap outlet
(see
P10-13)
1. Make sure that the tap location will allow the nozzle outlet, as well as the
vent outlet, to drain into the sink. (see outlet details P10)
2. Cut a 50mm hole in the bench / sink top.
3. Ensure the silicon O-Ring remains in place as this is the moisture
seal against the bench / sink top.
A light smearing of silicon sealant
on the O-Ring will ensure a watertight fit.
4. Pass all hoses through the 50mm hole and carefully locate the Head
Assembly on the bench / sink top.
5. From the underside of the bench / sink, mount the ‘base block’ by feeding
each of the tubes and electrical cable evenly in between the legs of the
‘base block spider’. Slide it up to meet the ‘all thread rod’, and pass the
‘all thread rod’ through the centre of the ‘base block’.
6. Hold the ‘all thread’ steady and fit the 6mm ‘fixing nut’ to the ‘all thread’
using the tube spanner supplied in the kit. Check the Tap Head position
before securing it tightly against the bench / sink top.
NOTE 1: The tap assembly must not be positioned more than 900mm
above the HydroTap unit.
Failure to do this may result in poor water delivery.
NOTE 2: Under no circumstances should the Tap be twisted after the
installation is complete.
Installation procedure
• Power supply 220-240 Volt AC, for connection to the heater via a 10 amp (160/125) or 15 amp (240/175) GPO.
• This switch must provide all-pole disconnection and a contact separation of at least 3mm installed in accordance
with wiring rules.
• Cold water supply with a minimum working pressure of 200 kPa and a maximum working pressure of 700 kPa
connected via an isolation valve. If pressure is likely to exceed 700 kPa, install a 500 kPa Pressure Limiting Valve.
• The fitting of an air flow vent cut into the top half of the cupboard door concealing the HydroTap requiring a cut size
of approximately 100mm circular, to provide adequate warm air displacement. In installations where high volume
draw-off will occur, the fitting of the accessory exhaust fan is essential.
Important: Do not proceed with the installation if these requirements are not met.
CAUTION:
In order to avoid a hazard due to the inadvertent resetting of the thermal cut out, this appliance must not
be supplied through an external switching device, such as a timer, or connected to a circuit that is regularly switched
on and off by the utility
Installation requirements
continued
O - Ring seal
Base Block
Fixing nut
Tap
All-thread rod