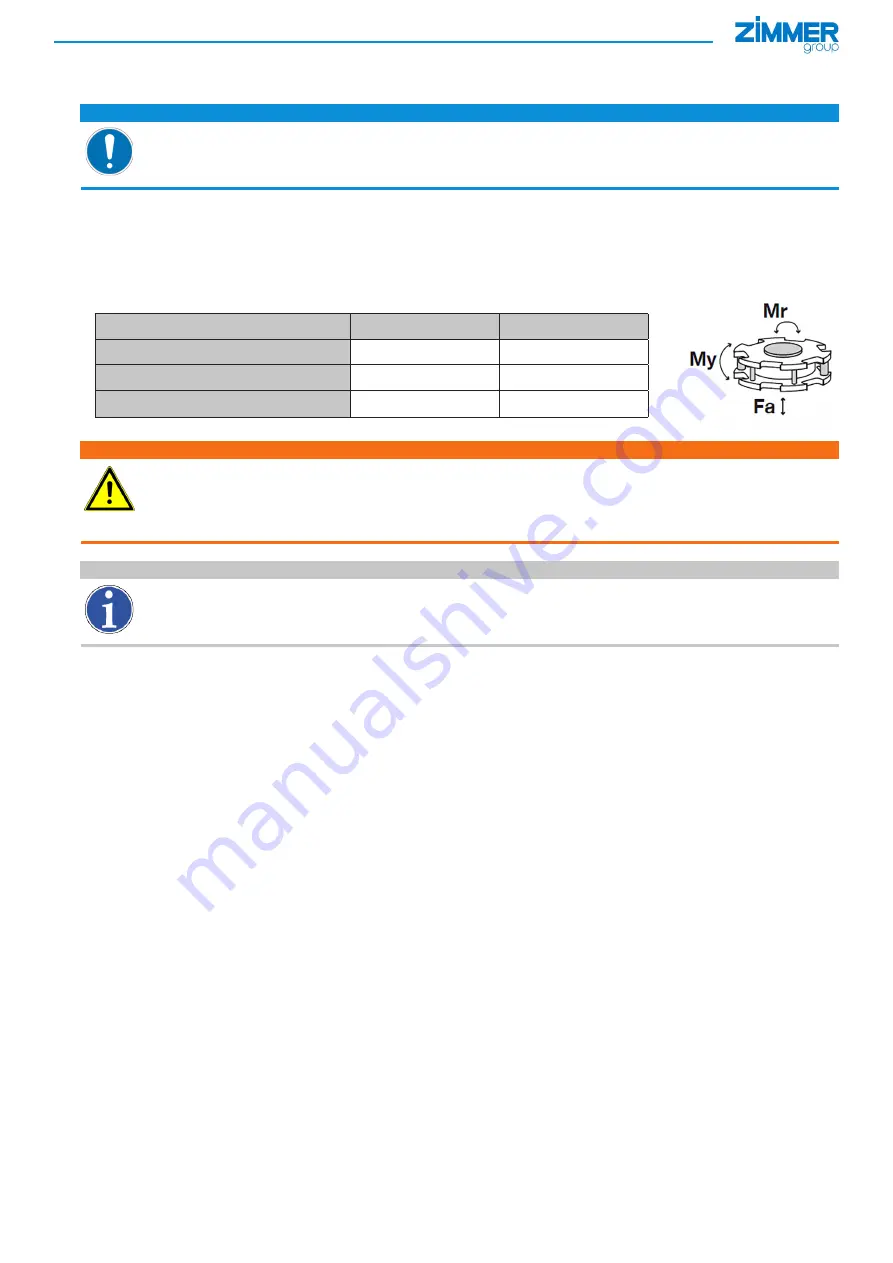
INSTALLATION AND OPERATING INSTRUCTIONS:
Tool changer, pneumatic, WWR1000 series
Zimmer GmbH
●
Im Salmenkopf 5
●
77866 Rheinau, Germany
●
Phone: +49 7844 9138-0
●
Fax: +49 7844 9138-80
●
www.zimmer-group.de
4
DDOC00291 / 0
EN / 2018-09-1
1
3 Proper use
NOTE:
The WWR1000 series element is only to be used in its original state with its original accessories, with no
unauthorized changes and within the scope of its defined parameters for use.
ZIMMER GmbH shall accept no liability for any damage caused by improper use.
The element is designed for operation with compressed air only. It is not suited for operation with other media such as
liquids or gases.
The fixed part of the element is intended to be used in closed rooms for handling and holding tool changer loose parts
with tools mounted thereon.
Static forces and torques that the element has to absorb must not exceed the recommended parameters.
WARNING:
• Danger of injury if the element is not operated as intended!
• The element must never be operated without compressed air. The built-in spring is used exclusively for
locking the device in case of power loss.
Always operate the element with an operating pressure between 6 and 8 bar!
Information:
Depending on the model, there are several transmission options available for transmitting pneumatic
and electronic actuators. Optionally, the media transmission can be set up with transmission elements at
corresponding interfaces on the element.
4 Personnel qualification
Installation, commissioning and maintenance may only be performed by qualified personnel. They must have read and
understood the installation and operating instructions in full.
Models (loose part & fixed part)
WWR1160F
WWR1200F
Torsional moment
Mr [Nm]
6000
12000
Tilting moment
My [Nm]
6000
12000
Max. permitted force Fa [N]
35000
75000