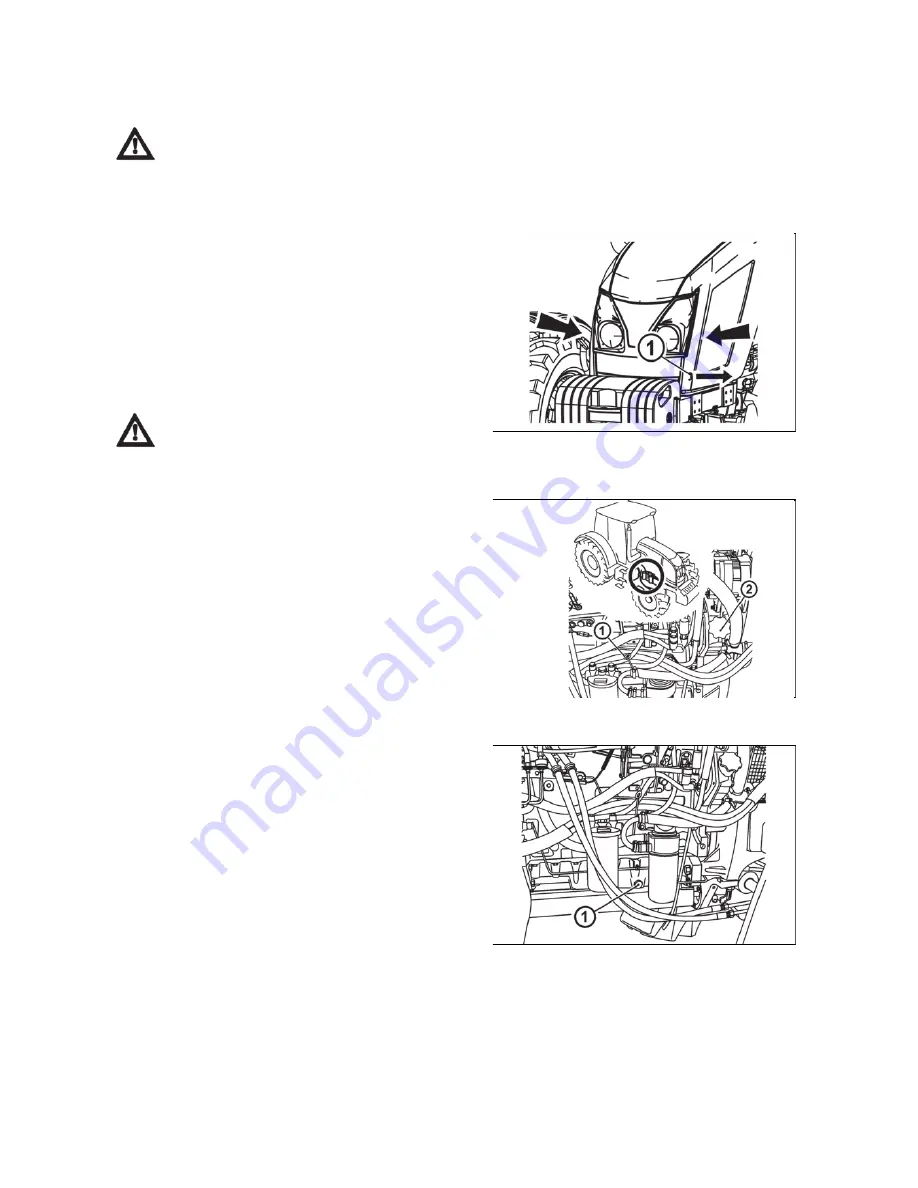
Most of operations of planned maintenance may be carried out by the driver or other user of the tractor. In
case you do not have sufficient technical equipment, let the difficult operations carried out by a specialised
repair shop.
All works, connected with cleaning, lubrication and adjustments of the tractor or coupled
mechanisms may only be carried out after stopping of the engine and other movable components
except checks of brakes, recharging and hydraulic system
.
Front bonnet opening
Checking oil levels in engine
Draining oil from engine
Opening the bonnet:
Unlock the bonnet by pulling the draw bar (1) in the
direction of an arrow, grip where the arrows are and
heave.
The bonnet is locked in the heaved position by a gas-fluid
prop.
Closing the bonnet:
Pull the bonnet by means of a belt, grip where the arrows
are and snap in the downward direction so that the lock of
bonnet snaps down.
Rapid closing of the bonnet may damage
filaments of bulbs in headlights in the front mask.
NM13N107
Check daily before starting the operation with the tractor
standing horizontally. Engine oil dipstick (1) and filling hole
(2) are placed on the rights side of the engine. Unscrew
the dipstick (1), wipe off with a cloth and screw back in.
When you unscrew the dipstick again, the level must not
drop below the bottom gauge. If necessary, refill oil by
a filling hole (2).
X903
1. unscrew the drain plug (1), best immediately after
terminating the drive or after heating the engine to working
temperature
2. drain oil
3. clean the drain plug
4. screw the drain plug (1) back in
E703
MAINTENANCE INSTRUCTIONS
133
Summary of Contents for Proxima GP 80
Page 1: ...Tractor is Zetor Since 1946 PROXIMA GP 80 OPERATOR S MANUAL 07 2017 90...
Page 3: ...2...
Page 21: ...NOTES 20...
Page 40: ...NOTES 39...
Page 51: ...NOTES 50...
Page 67: ...NOTES 66...
Page 71: ...NOTES 70...
Page 77: ...NOTES 76...
Page 101: ...NOTES 100...
Page 113: ...NOTES 112...
Page 117: ...NOTES 116...
Page 171: ...NOTES 170...