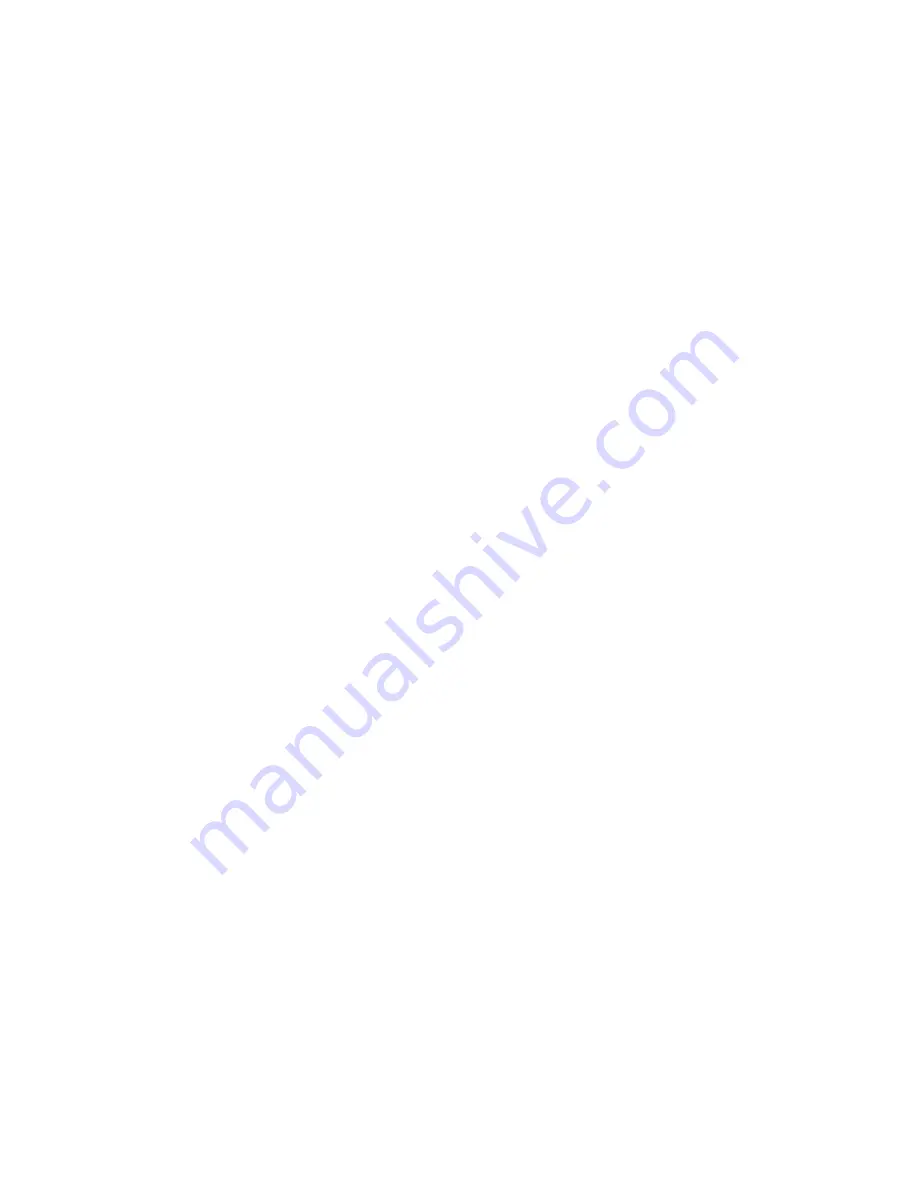
14
A differential pressure (DP) switch situated on the side of the filter monitors the filter’s
common inlet and discharge pressures. The Phoenix will initiate an automatic backwash
sequence once the DP switch reaches a predetermined set point adjusted by the operator.
The filter controls are contained within the filter and comprise a printed circuit board, timing
disk, optical sensors, a 24 VDC motor and gearbox assembly, and a pneumatically operated
ball valve on the filter’s backwash line.
Upon backwash initiation, the 24 VDC motor and gearbox assembly rotates a proprietary
diverting valve located in the inlet chamber. The rotation of the diverting valve indexes a
‘shoe’ through 360º during the backwash process. During backwash all six-filter elements
are backwashed sequentially by the indexing of the shoe allowing uninterrupted flow during
backwash. The slots in the timing disk determine the position of the valve.
The backwash sequence indexes the shoe such that it is positioned over the inlet to pod 1.
The flow of liquid into pod 1 has now been shut-off. The pneumatic ball valve is then
opened. By opening the backwash valve to atmosphere, a portion of clean filtered liquid is
allowed to travel in a reverse direction from the inside to the outside of the filter element.
This reverse supply of clean liquid will cause the filter element to open along its entire length
while ‘shimmering’ at the same time. The combination of the filter element opening and
‘shimmering’ allows for a very quick and efficient backwash.
In this way, all debris is removed from the outside of the filter element, even debris that may
be lodged on the surface of the filter element. This results in a very efficient backwash with
very little fluid required. The backwash sequence to clean each pod is normally 2 seconds.
When one pod has been backwashed, the next pod is then selected and so on until all six
pods have been backwashed. Once the backwash has been completed, the filter will return
to its clean differential pressure every time.
2.2 Differential Pressure (DP) Switch
The difference in pressure between the filter’s inlet and discharge operates a diaphragm,
which in turn will open the normally closed electrical contacts within the switch. This in turn
provides a signal to the control system (circuit board) which then initiates a backwash.