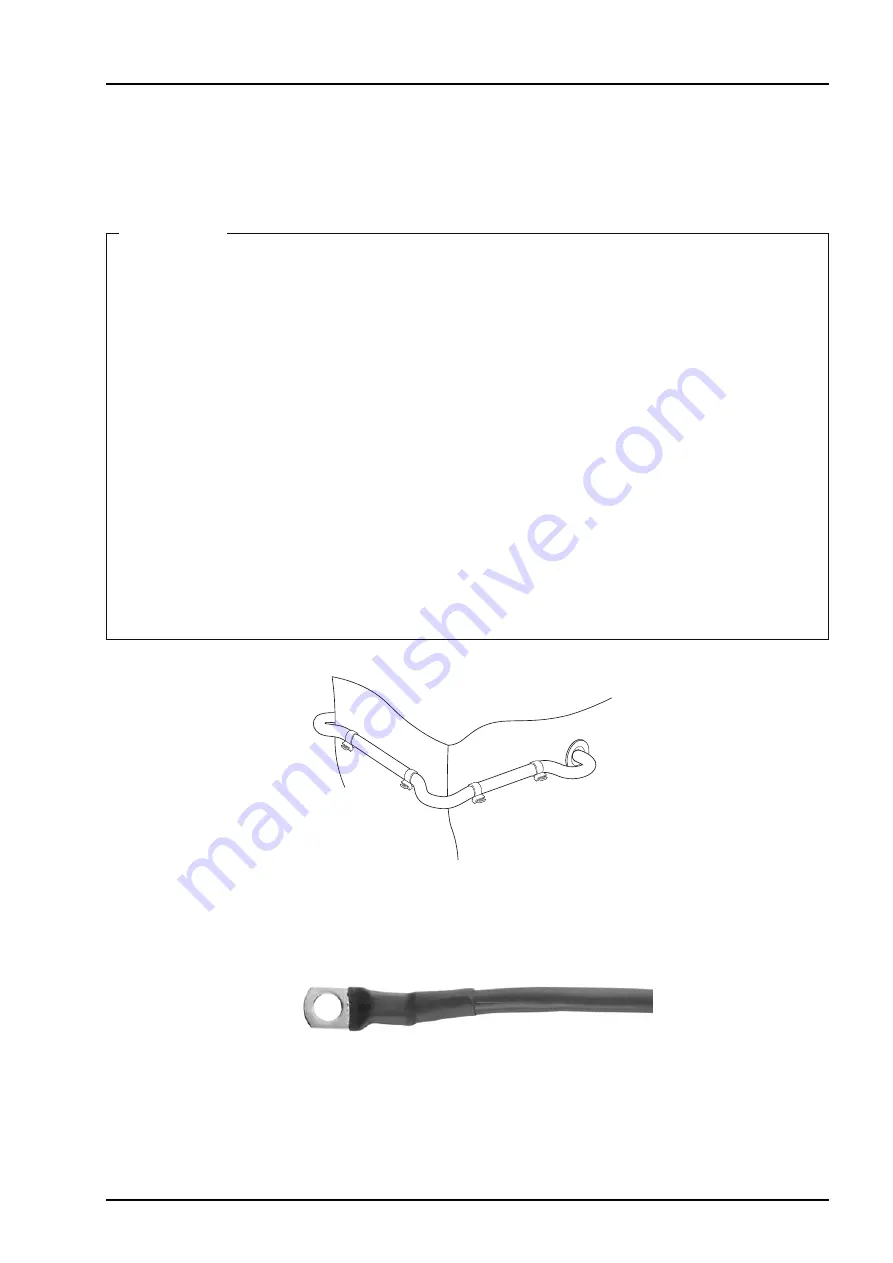
ZDK 250 135/155
Cable routing
35
www.zepro.com
5
Cable routing
5.1
General
In order to ensure a high degree of reliability for many years to come, it is important that components such as batteries, chargers,
main current and earth cables, fuses and main switches are dimensioned correctly and assembled with great accuracy. Insufficient
battery power can permanently damage the electrical components in the tail lift (solenoid, electric motor, solenoid valves, relay board/
control board and more.)
Insufficient main power and/or earth cable area may result in overheating, poor performance of the electrical system and shortened
life expectancy of the main electrical components.
Earth connection must be made primarily to the negative terminal of the battery. Alternatively, another well-protected earthing point,
which will not increase the voltage drop, can be used. The earthing point must be so well protected that increased voltage drop
due to oxidation over time can be eliminated. Risk of material damage. Warranty rights do not apply to material damage caused by
insufficient earthing.
Always install a shrink hose over the cable connection when installing cable terminals.
Pay attention and be careful during all cable routing to ensure longer cable life and reduce the risk of unnecessary downtime:
•
Cables must not be clamped to brake lines or the vehicle’s normal electrical system.
•
The cable must be protected by rubber grommets when it passes through beams or walls.
•
Cables must be installed sufficiently far
from, or be protected against, sharp edges so they cannot chafe or otherwise sustain
damage that could lead to a short-circuit and cable fires.
•
Take care not to bend cables to too tight a radius as this can cause damage.
IMPORTANT
!
Image 58. Protect the cable against sharp edges and use cable grommets
Image 59. Always use shrink hose over the cable connection when fitting cable terminals
Summary of Contents for ZDK 250 135
Page 2: ......
Page 65: ...ZDK 250 135 155 Registration 65 www zepro com...