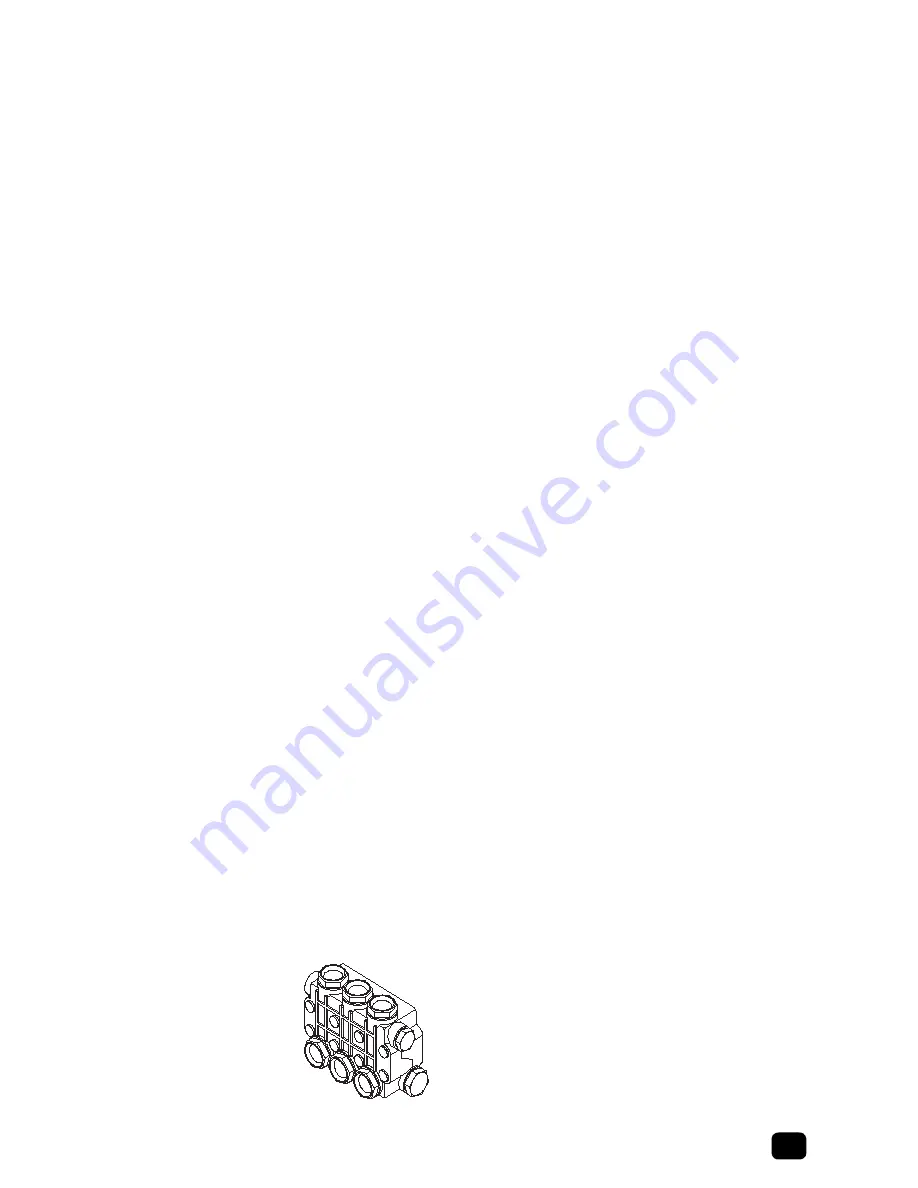
Pump Maintenance
Packing Service
1. Remove the head per PUMP HEAD REMOVAL.
2. Remove any packings and female adapters left on the plungers by pulling them straight off. Insert
proper packing extractor onto the extractor hammer. Insert packing extractor and tool through the
packings and adapters remaining in the head. Tighten the hammer and remove the remaining
items in the head. Remove packings and o-rings from adapters. Discard the o-rings and
packings.
3. Clean the packing canities in the head and rinse with clean water.
4. Clean exposed plungers. Clean male and female adapters with soap and water and allow it to
dry.
5. Examine male and female adapters, discard worn items. Trial fit the female adapters into the
head checking for binding or damage. Discard and replace damaged items
6. Lubricate packing cavities in the head and all packings and adapters with pump crankcase oil.
7. Lay head on the bench with packing cavities up. Install one male adapter in each cavity with the
flat side down.
8. Install one v-packing into each cavity with the lips pointing down. A packing insertion tool of the
appropriate size is recommended for this operation.
9. Install the re-stop ring with the lips pointing down.
10. Install a front female adapter into each cavity with the flat side up. Make certain the adapter goes
all the way down into the cavity.
11. Install the low pressure packing with the flat side down.
12. Install the rear female adapter into each cavity with the lips pointing down.
13. Lubricate o-rings with pump crankcase oil and install one into the groove of each adapter.
14. Install one adapter and o-ring into each cavity with the flat side up. Each adapter and o-ring
assembly should push into the head to approximately 1/16 inch of being flush with the surface of
the head. Only hand pressure should be required to perform this operation. This step is VERY
IMPORTANT. If the rear female adapter does not fit is obtained, proceed to step 16. If a proper
fit is not obtained, remove the female adapters from the offending cavity and reinstall items per
steps 8 through 15.
15. Install head per HEAD INSTALLATION.
Head Installation
1. Prepare pump head per instructions in PACKING SERVICE.
2. Rotate the plungers so the outer plungers are projecting the same distance from the crankcase.
3. Lubricate the exposed plungers with crankcase oil.
4. Start the head onto the plungers and, using a soft mallet, tap the head evenly until it comes in
contact with the crankcase.
5. Start the cap screws through the head and into the crankcase. Do not forget the lock washer on
each screw.
6. Tighten all cap screws by hand.
7. Torque the cap screws to the value indicated in the TORQUE section of PUMP
SPECIFICATIONS. Torque the cap screws in the order listed below.
5
3
1
7
6
4
2
8
7
Summary of Contents for N83701
Page 1: ...Servic e Manua l Servic e Manua l g distribu c com 6...
Page 5: ...Final Assembly...
Page 9: ...Burner Assembly...
Page 11: ...10 Burner Assembly...