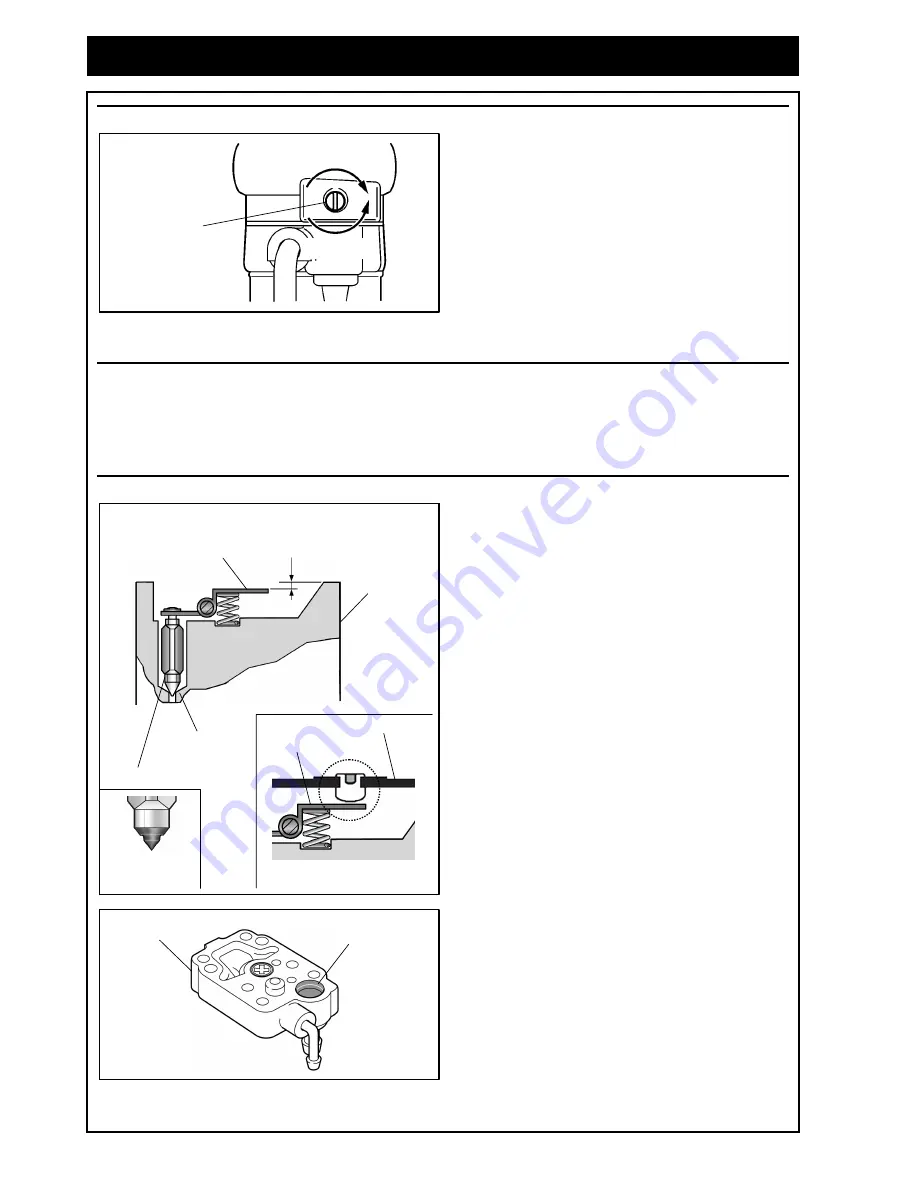
45
6. Carburetor
High Speed Adjustment
【
【【
【
USA/ HBZ2601 only
】
】】
】
High speed revolutions are adjusted by a H-needle.
Clockwise (CW):
Fuel mixture becomes lean. (Speed increases.)
Counterclockwise (CCW):
Fuel mixture becomes rich. (Speed decreases.)
6-6 Carburetor Inspection
Inlet Valve Leaking Test
Connect a leak tester to the fuel inlet port of the carburetor.
After filling the metering chamber with fuel, apply pressure to the inlet valve and read the opening pressure
and the reseating pressure.
a. Body assembly normality check
●
Measure the metering lever height using a depth
gauge or scale.
The appropriate value is 1.5
±
0.16 mm (0.059
±
0.006 in.)
●
Check that no wear exists on the metering lever or
diaphragm contacting areas.
If wear exists, replace it with a new one.
●
Remove the inlet valve and check for dirt, sludge,
rusting and/or step-wear.
Replace the inlet valve if a step is found on the
rubber tip.
●
Check that no alien matter adheres to the valve
sheet part. If any alien matter exists, dip the valve
sheet in gasoline for about 10 minutes and remove
it, or use the carburetor conditioner (Carburetor
Conditioner: 699-90345) to clean it.
●
Check that no alien matter has accumulated on the
screen.
If screen is clogged with alien matter, remove the
screen and clean it.
H-needle
Increases
Decreases
Metering Lever
Inlet Valve
Rubber Tip
1.5
±
0.16 mm
(0.059
±
0.006 in.)
Body
Assembly
Metering Lever
Main Diaphragm
Valve Sheet
Screen
Body Assembly