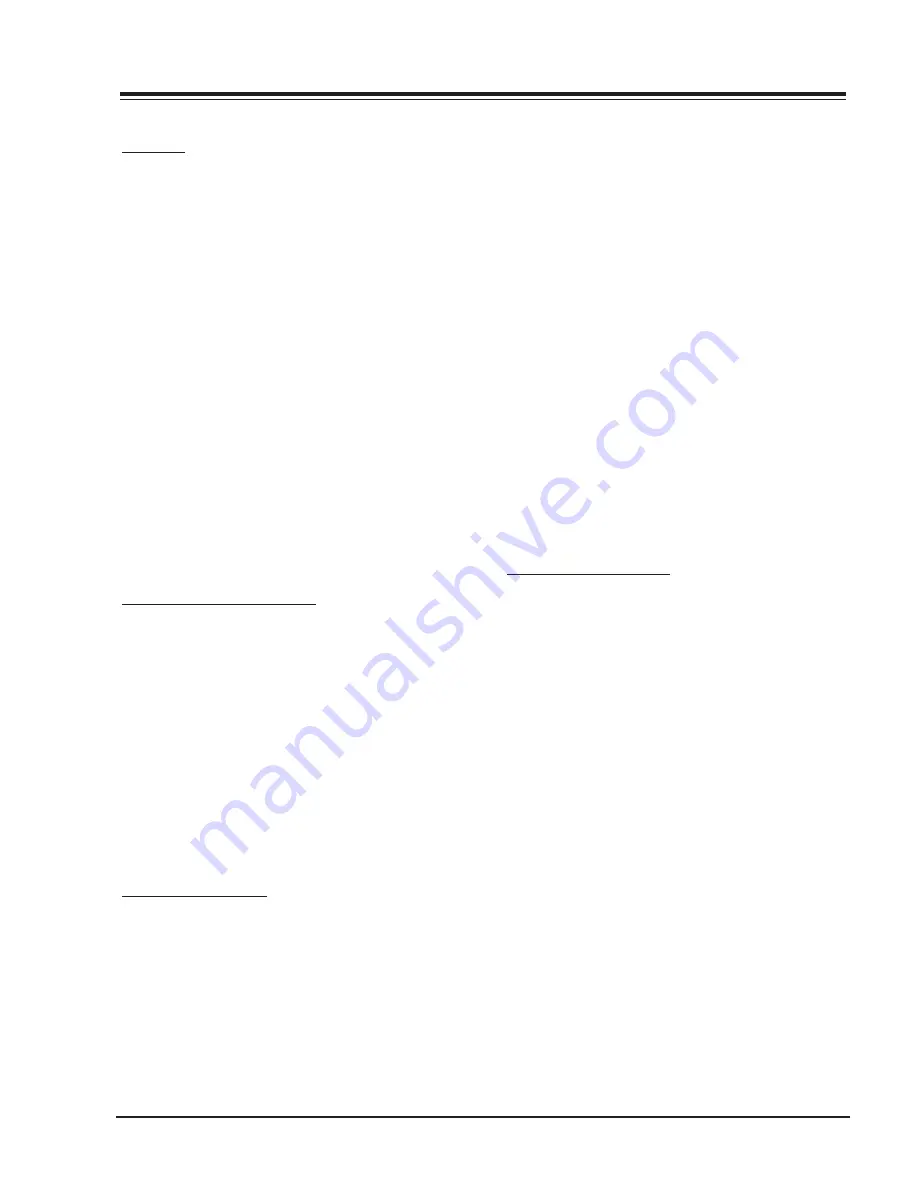
PV154 - 923-03499
9
P50W26 - SERVICING
SERVICING
SERVICING
OVERVIEW
Because this is not a hot chassis, it is not necessary to
use an isolation transformer. However, the use of isolation
transformer will help protect test instrument.
Adjustments must be done in the correct order. The
adjustment must be performed at 25±5
o
C of temperature
and 65±10% of relative humidity.
The input voltage of the receiver must maintain
110~240V, 50/60Hz while adjusting. Operate the receiver
for about 15 minutes prior to the adjustment with 100%
white pattern (06CH), or white condition in HEAT-RUN
mode.
Enter into HEAT-RUN mode. Press the POWER ON KEY on
R/C for adjustment. OSD display HEAT-RUN WHITE and
screen display 100% full WHITE PATTERN. Set is activated
HEAT-RUN without signal generator in this mode. Single
color pattern of HEAT-RUN mode uses to check the PANEL
(RED/BLUE/GREEN).
Caution: If you turn on a still screen more than 20 minutes,
an afterinage may occur in the black level part of
the screen. (Especially Digital Cross Hatch Pattern),
a afterimage may be occur in the black level part
of the screen.
RGB AUTO CUT-OFF & MIN BIAS
1) If the PDP Module or Power Board was replaced, ad-
just the Power PCB Assy Voltage prior to any other
adjustment.
2) Input Full Back (0 Gray) signal which generated from
Pattern Generator into Component input and RGB1
Input part.
3) Press POWER ON KEY on R/C for adjustment and select
AUTO-CUT(Cut-off Auto Adjustment).
4) Press Vol. + key.
5) Screen adjustment starts with Full Black screen. Origi-
nal Window screen will be presented about 5-6 sec-
onds later. And if (OK OSD) appears on the screen,
then the Auto Cut-off and Min-Bias adjustment will
have been completed.
MAX BIAS ADJUSTMENT
1) Input Full White (255 Gray) signal which generated
from Pattern Generator into Component input and
RGB1 Input.
2) Press POWER ON KEY on R/C for adjustment and select
MAX-BIAS.
3) Press Vol. + key.
4) Original Full White screen will be presented about
1-2 seconds later. And if (OK OSD) appears on the
screen then the Min-Bias adjustment will have been
completed.
(5) After adjustment, press ¥ key to save adjustment
and come out of the adjustment mode.
To check whether the circuit adjustment is operated well
or not:
1) Display RGB1 to the Main picture, Component
input to the Sub picture in the TWIN PICTURE.
2) To check the MIN-Bias, input Full Black (0 gray) sig-
nal into Component input and RGB1 input part at the
same time in the Pattern Generator.
3) To check the MAX-Bias, input Full White (255 gray)
signal into Component input and RGB1 input part
at the same time in the Pattern Generator.
4) Compare Black Level with White Level by eye. And
if there is no Level difference, the adjustment is
completed.
Data value, which adjusted in the board, is valid until
the VSC Board is dissued and must be protected. For the
protection of data, Micom does not permit any more
adjustment after completion.
In case of re-adjustment, operate First Value Setting.
Each PCB Assy must be checked by Check JIG Set before
assembly. (Especially, be careful Power PCB Assy which
can cause fatal Damage to PDP Module.)
POWER PCB ASSY VOLTAGE
VA ADJUSTMENT
1) Test Equipment : D.M.M 1EA
2) After receiving 100% white pattern, HEAT RUN.
3) Connect + terminal of D.M.M to Va pin of P805
and connect Ð terminal to GND pin of P805.
4) After turning the VR4, voltage of D.M.M adjust-
ment as same as Va voltage which on label of panel
Right/Top. (Deviation : ±0.5V)
VS ADJUSTMENT
1) Connect + terminal of the D.M.M to Vs pin of
P805 and connect - terminal to GND pin of P805.
2) After turning the VR1, voltage of D.M.M ad-
justment as same as Vs voltage which on label
of panel Right/Top. (Deviation : ±0.5V)
Summary of Contents for P50W26
Page 4: ......
Page 8: ......
Page 21: ......
Page 22: ......
Page 25: ...29 P50W26 DIAGRAMS PV154 923 03499 P50W26 Block Diagram...
Page 26: ...30 P50W26 DIAGRAMS PV154 923 03499 P50W26 Main PCB M A I N TOP...
Page 28: ...32 P50W26 DIAGRAMS PV154 923 03499 P50W26 Other PCBs...