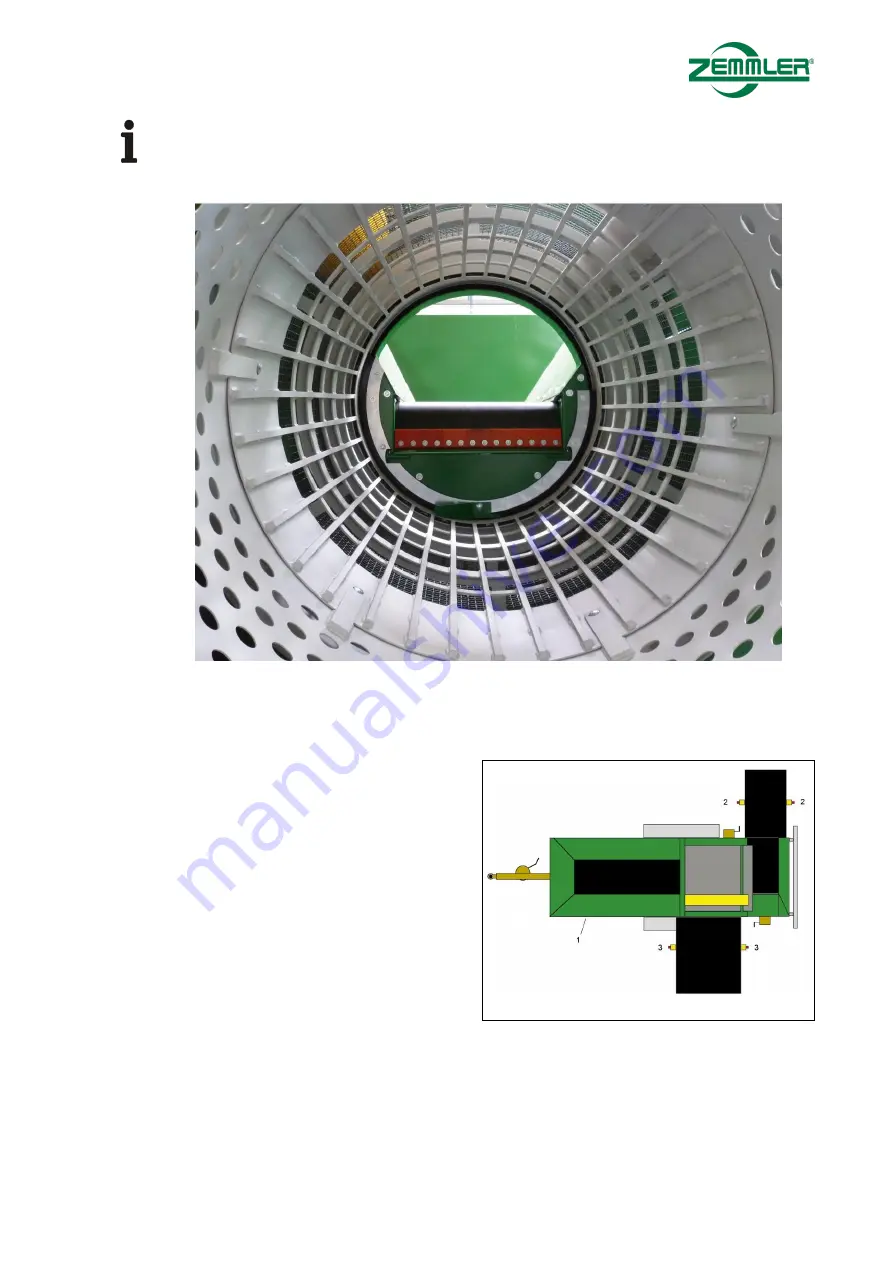
Operating Manual ZEMMLER MULTI SCREEN MS 1600
Service and maintenance
MS1600.153.19
Page
43
Notice!
The machine must always be run empty. The visual check is to be done from the review
of the double trommel and conveyor belts.
fig. 11-: Visual check of double trommel
11.4
Securing the machine
1.
Turn off engine.
2.
Press emergency stop and
pull out the key.
3.
Main switch on “OFF”. The
control unit has to be
secured by a padlock for
accidental restart.
fig. 11-1: Safeguard devices
11.5
Maintenance after initial operation
The first maintenance after initial operation occurs exclusively by specialists of Zemmler
Siebanlagen GmbH. Subsequent maintenances can be seen from maintenance
schedule.