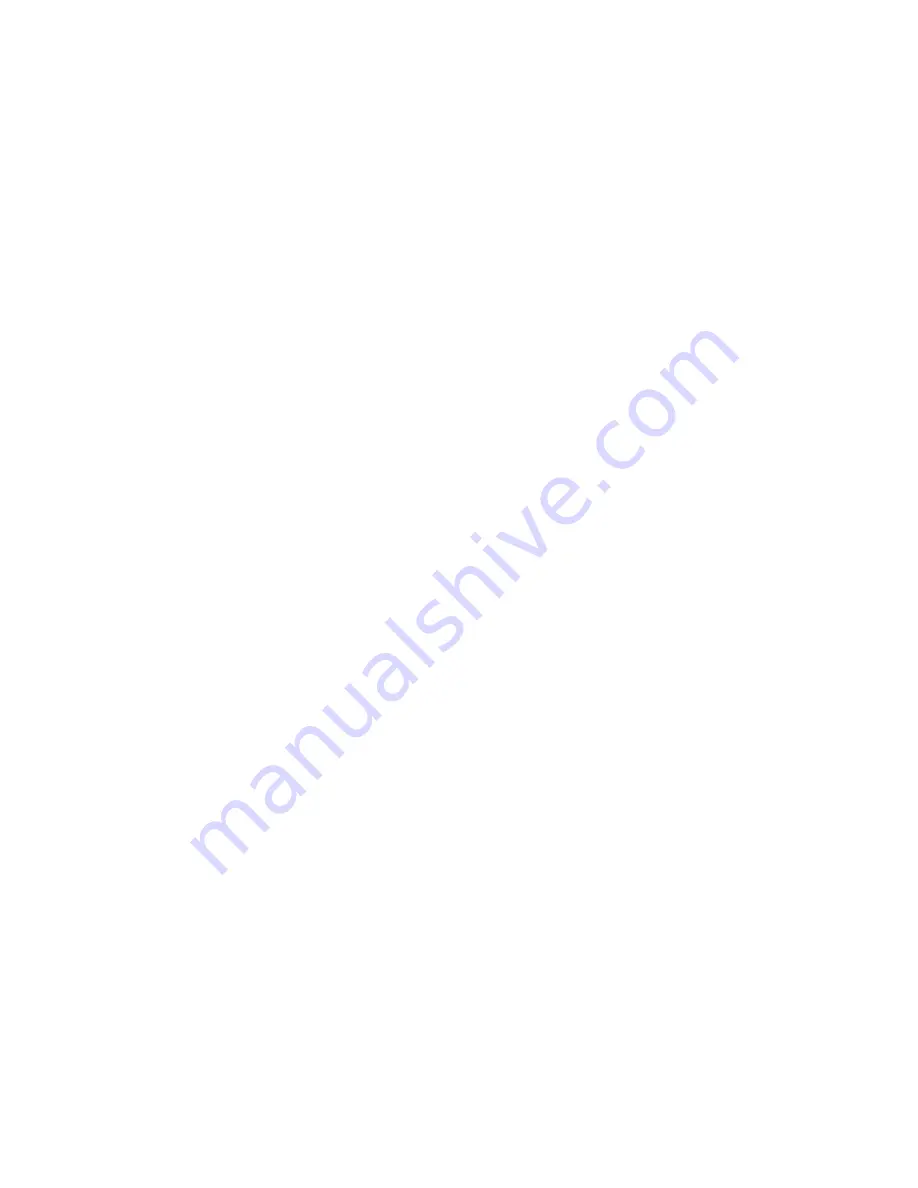
8
6.3 MOISTURE REMOVAL SYSTEM
Liquid droplets are removed from the air stream in the separator. As the air and
liquid mixture passes through the separator it spins, slows down and then changes
direction. This causes the condensate to fall out of the air stream and collect in the
bottom of the separator. The collected liquid is removed from the separator by a
solenoid valve. The solenoid valve is controlled by the microprocessor controller as
described in Section 6. For adjustment please note the following:
•
To obtain the optimum time values for operation of the solenoid drain valve, set
the off-time to five minutes and the on-time five seconds via the controller. Refer to
Section 6 for details.
•
After running the unit under full rated flow for approximately 30 minutes, verify that
when the solenoid drain opens, all of the accumulated liquid is discharged and then
a small burst of air.
•
If a small amount of liquid and a large amount of air is discharged, decrease the on-
time setting or increase the off-time setting. If there is all liquid and no air has been
discharged, increase the on-time setting or decrease the off-time setting.
•
The on/off time settings will vary according to seasonal operating conditions. During
the summer when more moisture is present in the air system a shorter on-time,
increasing the valve opening frequency, is required. A longer valve off-time may be
used during the winter months when moisture levels are lower.
6.4 REFRIGERATION SYSTEM
The Refrigeration System consists of all the components which handle refrigerant
R404A. This is a hermetically sealed closed-loop system. Referring to Figure 1 and
following the dot-dash “
REFRIGERANT FLOW
,” refrigerant is shown leaving the chiller
evaporator section, which in the process of removing heat is changed from a low
pressure liquid to a low pressure gas. This gas enters the suction side of the
compressor where it is compressed into a high pressure gas. The high pressure gas
is cooled in the air or water cooled condenser section becoming a high pressure
liquid. It then goes through a permanent filter-dryer that ensures the refrigerant
system is free of contaminants. A thermostatic expansion valve meters the refrig-
erant into the chiller’s evaporator. The pressure is reduced upon entering the chiller
evaporator where it removes heat from the air system. When there are low loads
(low air flow rate or inlet temperature), a hot gas valve by-passes the condenser and
throttling device (capillary tube). This valve maintains a minimum evaporator
pressure of 76 psig, which corresponds to a chiller temperature of 34°F, thus
preventing freeze-up.
6.5
CONTROLS
ZEKS’ 500-800NCE Refrigerated Compressed Air Dryers are equipped with the
Digital Performance Controller (DPC™). This advanced microprocessor-based
controller has been engineered by ZEKS exclusively for use with ZEKS’ Compressed
Air Dryers.
Summary of Contents for CFX NC Series
Page 28: ...27 11 WIRING DIAGRAMS...
Page 29: ...28...
Page 30: ...29...
Page 31: ...30...
Page 32: ...31 12 GENERAL ARRANGEMENT...
Page 34: ...33...
Page 35: ...34...
Page 36: ...35...