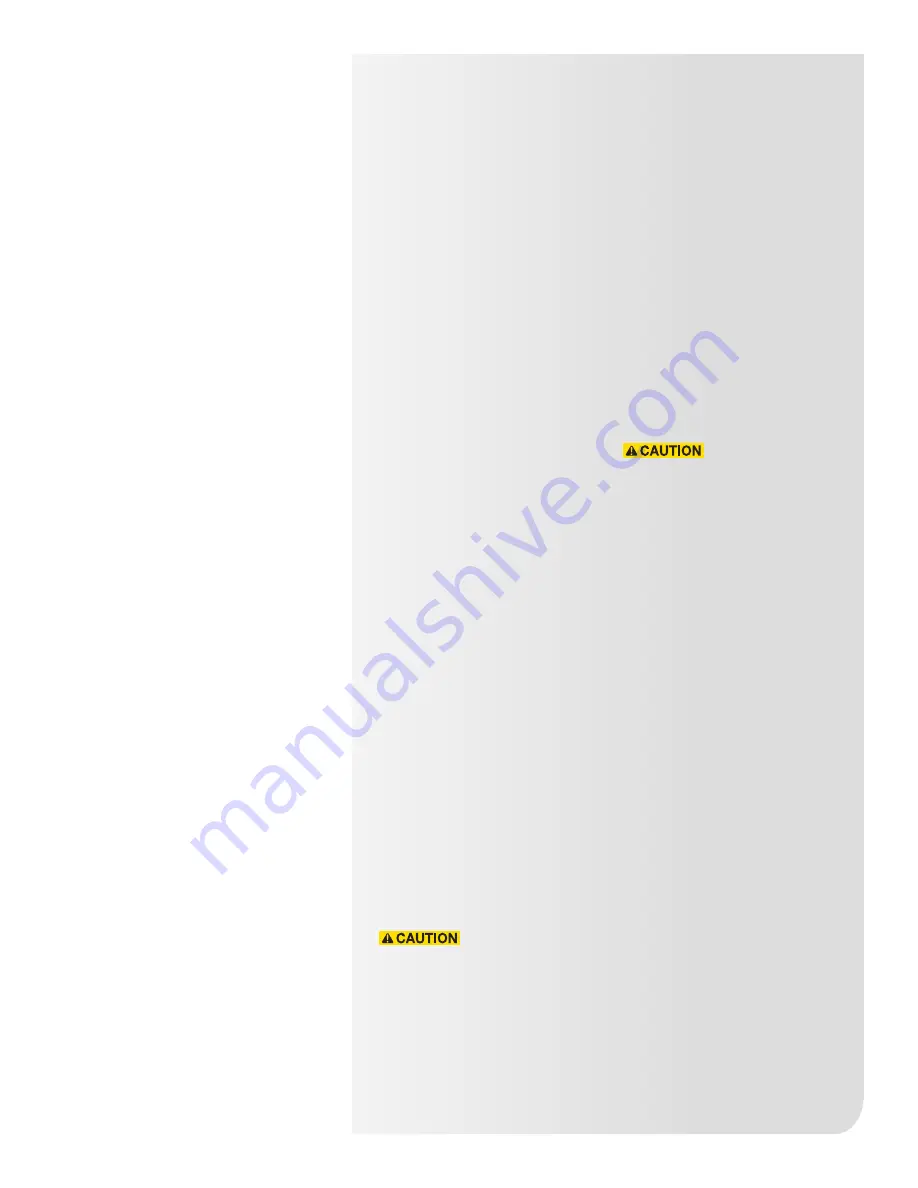
15
Hot water
connections
Submittals and product literature
detailing unit operation, controls
and connections should be
thoroughly reviewed before
beginning the connection of the
heating medium to the unit.
All shipped loose valve packages
should be installed as required
and all service valves should be
checked for proper operation.
All coil and valve package
connections are to be made
with a sweat or solder joint.
Care should be taken to assure
that no components in the valve
package are subjected to a high
temperature which may damage
seals or other materials. Many
two-position electric control
valves, depending on valve
operation, are provided with a
manual opening lever. This lever
should be placed in the “open”
position during all soldering
or brazing operations. In
accordance with good soldering
and brazing practices, valve
bodies should be wrapped with
a wet rag to help dissipate the
heat.
If the valve package connection
at the coil is made with a union,
the coil side of the union must be
prevented from twisting during
tightening to prevent damage to
the coil tubing. Over-tightening
must be avoided to prevent
distorting the union seal surface
and destroying the union,
ultimately causing a leak.
Secure the union nut hand-tight
and then tighten no more than an
additional 1/4 turn.
The inlet supply connection is
marked at the appropriate coil
stub-out with the other coil
stub-out being the outlet return
connection.
After the connections are
completed, the system should
be tested for leaks. Since
some components are not
designed to hold pressure with
a gas, hydronic systems should
be tested with water. Test
pressure must not exceed 250
psig. Pressure testing should
be completed prior to sheet
rocking, finished floors, painting,
caulking, etc.
All water coils must be protected
from freezing after initial filling
with water. Even if the system is
drained, unit coils may still hold
enough water to cause damage
when exposed to temperatures
below freezing.
In the event that leaking or
defective components are
discovered, the Zehnder Rittling
Sales Representative must be
notified before any repairs are
attempted. All leaks should be
repaired before proceeding with
the installation.
After system integrity has been
established, it is recommended
that the piping be insulated in
accordance with the project
specifications. This is the
responsibility of the installing
or the insulation contractor.
Zehnder Rittling will not accept
any charges associated with
re-insulating piping if the
installing contractor failed to
establish system integrity prior to
insulating.
Hot water connections