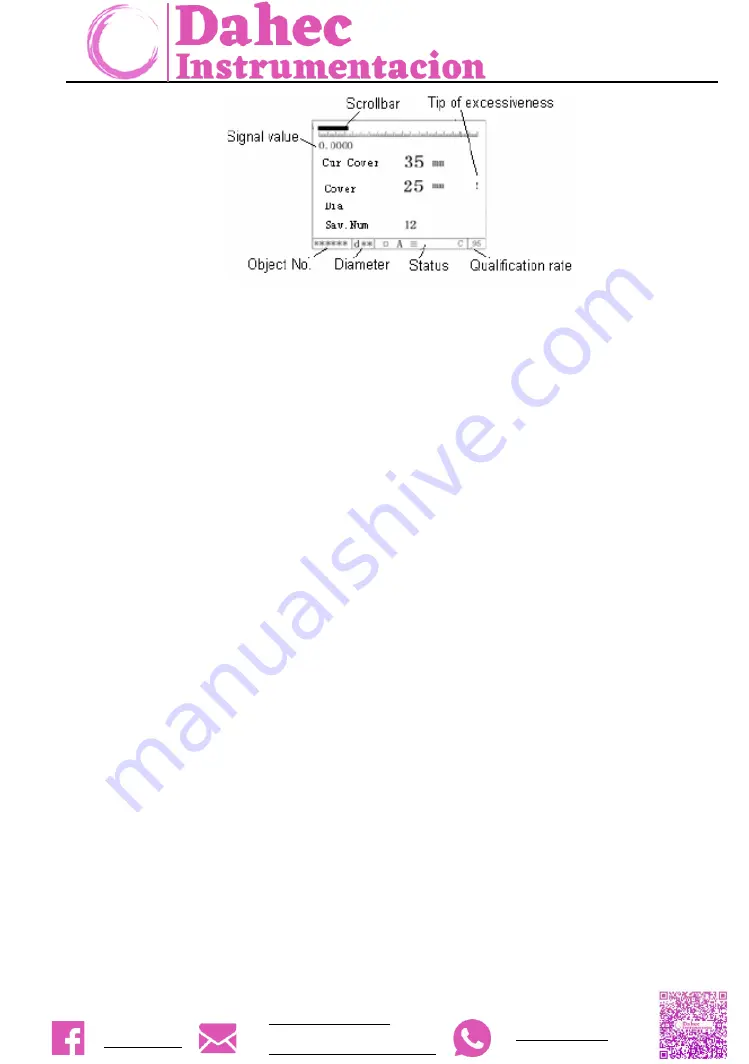
ZBL-R630A Rebar Detector
+52 5586114372
+52 7791340470
Figure 3-7Test interface of General-scan
3.1.2.1
Introduction of the interface
➢
Scrollbar
—show the relative distance between sensor and rebar.
Blank—no rebar in sensing range of sensor
Increase—sensor is moving towards rebar
Decrease—sensor is moving away from rebar
➢
Signal value
— the larger present sensor receiving signal amplitude, the closer to rebar.
➢
Cur. Cover
—the current thickness of cover, the equivalent distance (unit, mm) between sensor and
rebar, the larger the equivalent value, the farther it is. When equivalent value exceeding
measurement ranges of sensor, it is 0 and the minimum value of current thickness is the thickness
of cover. (If users used data correction, it only shows measurement value not corrected one)
➢
Cover
—display of measurement value (unit, mm) of thickness of concrete cover automatically (If
users used data correction, it shows the corrected value).
➢
Dia.
—
display of measurement diameter of tested rebar (unit, mm). pressing
【
▲
】
key for
measurement of diameter and thickness of cover (There is no need for the input of the diameter of
tested rebar), please see detail description in chapter 3.4.1.3. After testing the diameter, it will
display as follows:
Cover:
▶
*** ( measurement of the thickness of cover of rebar)
Dia.: *** (measurement of rebar diameter)
➢
Sav. Num
— it is the stored amount of thickness of cover for present object.
➢
Qualification rate
—the rate of qualified points of all the stored thickness values in current object
according to the specification of GB50204-2002.