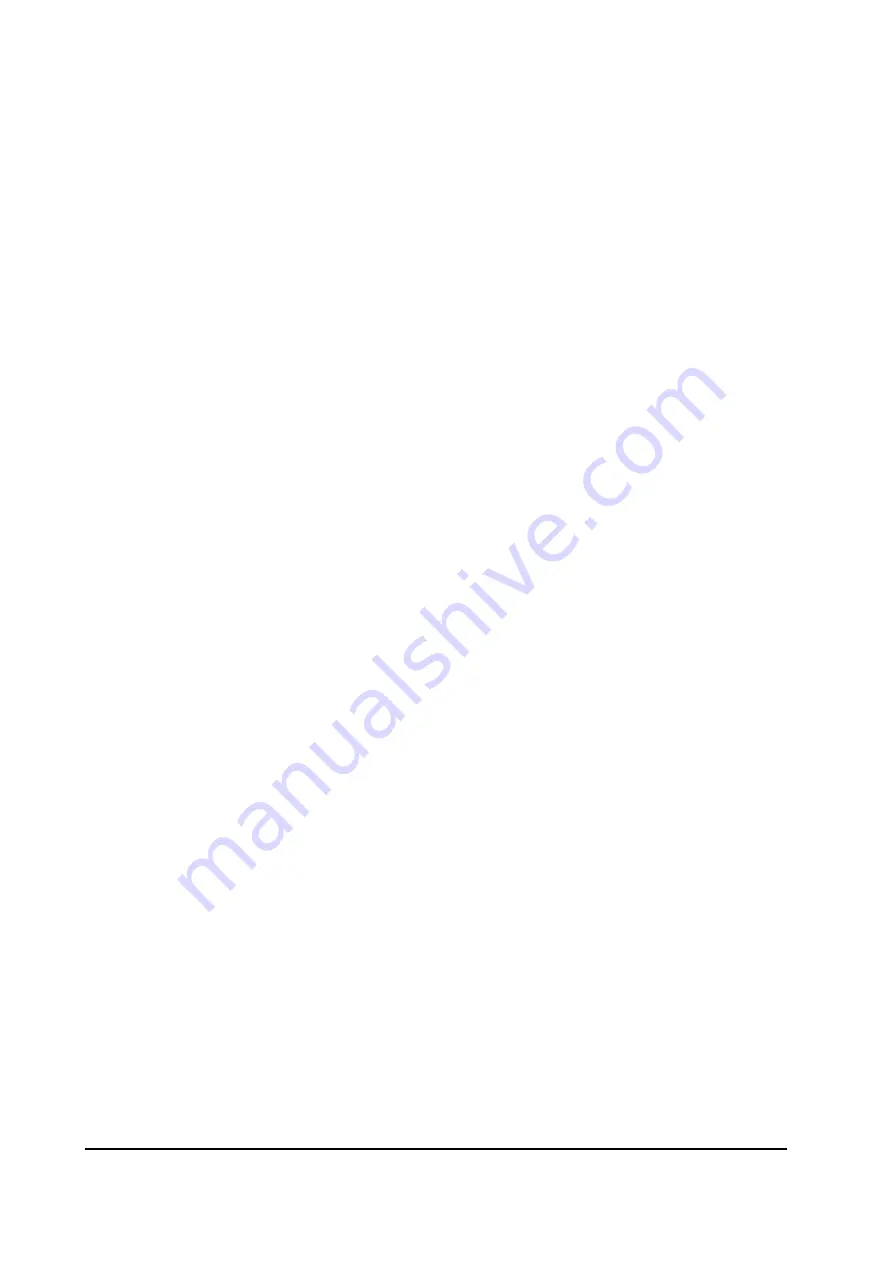
Page 56
6 AC INVERTER DIAGNOSTIC - TRACTION CONFIGURATION
The alarms are signalled by a diagnostic LED.
1 blink:
logic failure ("WATCHDOG", "EEPROM KO", "LOGIC FAILURE #1",
"LOGIC FAILURE #2", "LOGIC FAILURE #3", "CHECK UP NEEDED").
2 blinks:
running request on start-up or error in seat sequence or double direction
request ("INCORRECT START", "HANDBRAKE", "FORW + BACK").
3 blinks:
phase voltage or capacitor charge failure
("CAPACITOR CHARGE", "VMN LOW", "VMN HIGH").
4 blinks:
failure in accelerator ("VACC NOT OK", "PEDAL WIRE KO").
5 blinks:
failure of current sensor
("STBY I HIGH").
6 blinks:
failure of contactor driver
("COIL SHORTED", "DRIVER SHORTED", "CONTACTOR DRIVER", "AUX OUTPUT
KO", "CONTACTOR OPEN").
7 blinks:
excessive temperature ("HIGH TEMPERATURE", "MOTOR TEMPERA-
TURE", "THERMIC SENSOR KO").
8 blinks:
failure detection from can-bus ("WAITING PUMP", "CAN-BUS KO").
long blink: discharge battery ("LOW BATTERY")
6.1 ANALYSIS OF ALARMS DISPLAYED ON CONSOLE
1. WATCH DOG
The test is made in both running and standby. It is a self-diagnosing test within the
logic. If an alarm should occur, replace the logic.
2. EEPROM KO
Fault in the area of memory in which the adjustment parameters are stored; this alarm
inhibits machine operation. If the defect persists when the key is switched OFF and
ON again, replace the logic. If the alarm disappears, remember that the parameters
stored previously have been cancelled and replaced by the default values.
3. LOGIC FAILURE #1
This alarm signals that an undervoltage / overvoltage protection operation has oc-
curred. Two possible reasons:
a. A real undervoltage / overvoltage situation happened.
b. Fault in the hardware section of the logic board which manages the overvoltage
protection. Replace the logic card.
4. LOGIC FAILURE #2
Fault in the hardware section of the logic board which manages the phase' s voltage
feedback. Replace the logic board.
5. LOGIC FAILURE #3
Fault in the hardware section of the logic board which manages the hardware current
Summary of Contents for ZAPIMOS Series
Page 21: ...Page 21 3 8 AC3 MECHANICAL DRAWING...
Page 22: ...Page 22 3 9 AC4 MECHANICAL DRAWING...
Page 23: ...Page 23 3 10 CONNECTION DRAWING TRACTION CONFIGURATION 3 10 a Amp Saab connector...
Page 24: ...Page 24 3 10 b Molex Minifit connectors...
Page 25: ...Page 25 3 11 CONNECTION DRAWING PUMP CONFIGURATION 3 11 a Amp Saab connector...
Page 26: ...Page 26 3 11 b Molex Minifit connectors...
Page 27: ...Page 27 3 12 CONNECTION DRAWING COMBI CONFIGURATION 3 12 a Amp Saab connector...
Page 28: ...Page 28 3 12 b Molex Minifit connectors...
Page 30: ...Page 30 4 3 DESCRIPTION OF STANDARD CONSOLE MENU 4 3 a Traction configuration...