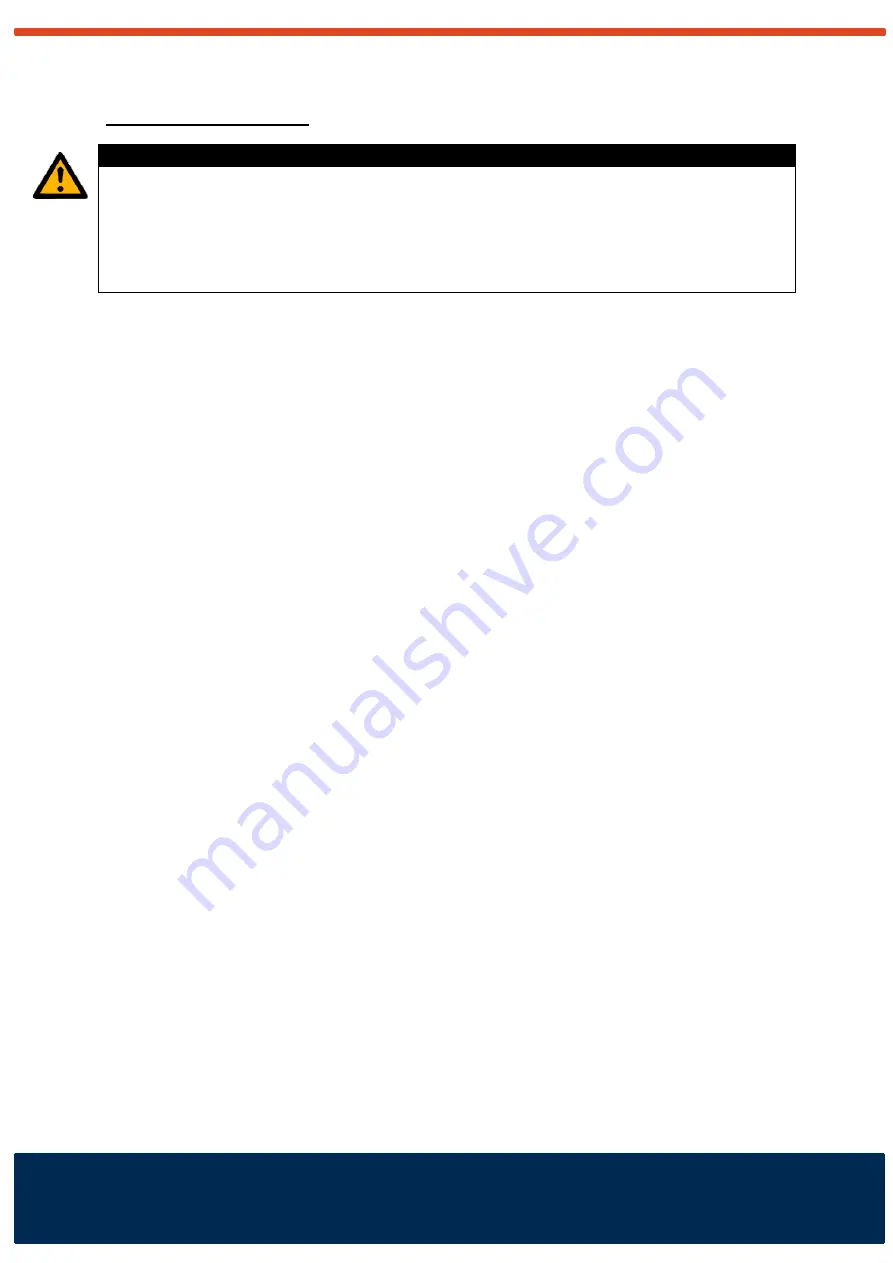
Page. 26
LMV5000.EN202001V6
8. TROUBLESHOOTING
WARNING:
Set the main switch on the burner panel to “OFF” before performing any
maintenance work. Lock the switch to ensure nobody can set the main switch
to “ON” when performing the maintenance work. Never work on the system if
the control panel is live (energized).
When switching off the main burner control panel switch also switch off the power of
any connected CO
2
dosing unit control panel.
All safety devices have a signal light on the control panel. At every lockout of a safety
device the corresponding signal light will be on. To reset the system press the reset
button on the switch panel door. The burner will attempt to restart.
Note:
The maximum thermostat and the low water protection device may be
mechanically locked. The reset button on the safety device itself should be pressed
first, before resetting the whole system. If the burner does not start a failure of the
CO
2
-dosing unit and/or CO-detector may have been triggered.
Keep a close eye on parts which may not operate appropriately when restarting. If
the same error occurs again:
•
Write down the text/code which appears in the display of the AZL unit. See
“Display and error messages” (separate AZL manual).
•
Write down the system number, burner type and manufacturing year (refer
to the label on the burner control panel).
•
Contact our local service department. They will first attempt to solve the
problem via the telephone call.
Summary of Contents for RKB
Page 29: ...Page 29 LMV5000 EN202001V6...