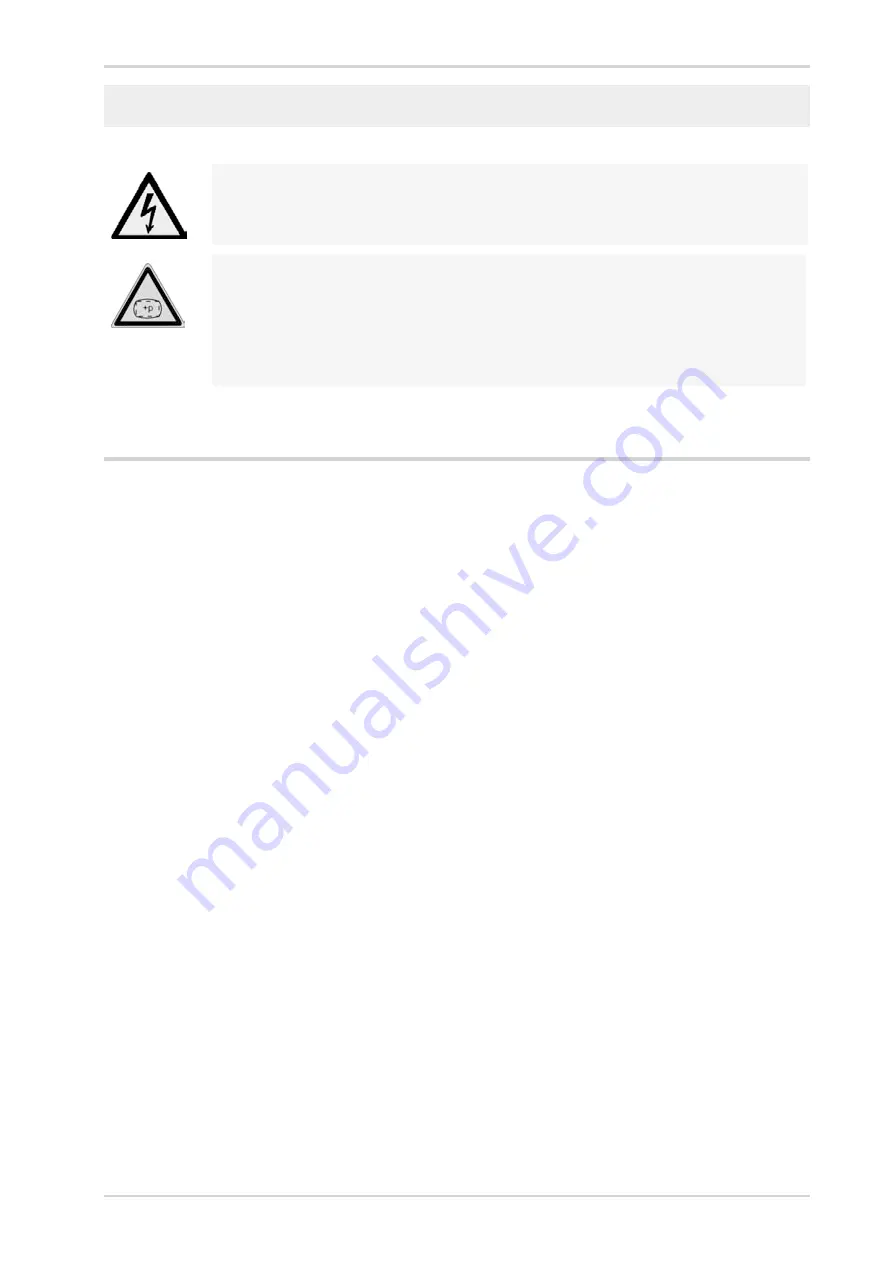
Installation
Multitronic-Retrofit Kit_01_2004-06-16
9
Installation
Only authorized and qualified specialist personnel may carry out work on
electrical systems.
Hazard due to a sudden release of pressure!
Never remove any parts of the dryer, or manipulate the same in any way,
for as long as the plant is still pressurised! A sudden escape of pressure
may cause serious injuries.
Before carrying out any work on the dryer, first depressurise the plant.
Preparation
Inspection of delivered goods
►
Inspect delivery for completeness.
►
Check the details regarding the power supply with the data on the original
type plate of the dryer to be retrofitted and ensure that the specifications are
matching.
Preparing the dryer
►
Release all pressure from the unit and disconnect it from the power supply.
►
Secure against inadvertent switching on.
►
Preparing mounting area. If necessary, dismantle existing control system and
remove cables.
►
Clean mounting surface and ensure that it is free from dust and grease; use
only solvent-free detergents.
►
Optional for
Retrofit Kit Plus
: For the installation of the sensor cell at the
compessed air outlet, you must mount a suitable branch fitting (T-piece) after
the dust filter. In large units, it is generally possible to install an additional
outlet line in the existing control air pipe.
Define the place at which you wish to mount the sensor cell; the cell's power
supply line should be from the side, while the sensor cell and the sensor are
mounted vertically.
►
Position the self-adhesive dots (not reusable) to mark the mounting position
of the switch box.
►
Remove the type plate and mark it as invalid.
►
Attach the new supplied type plate; add missing data using a water-proof felt
pen.