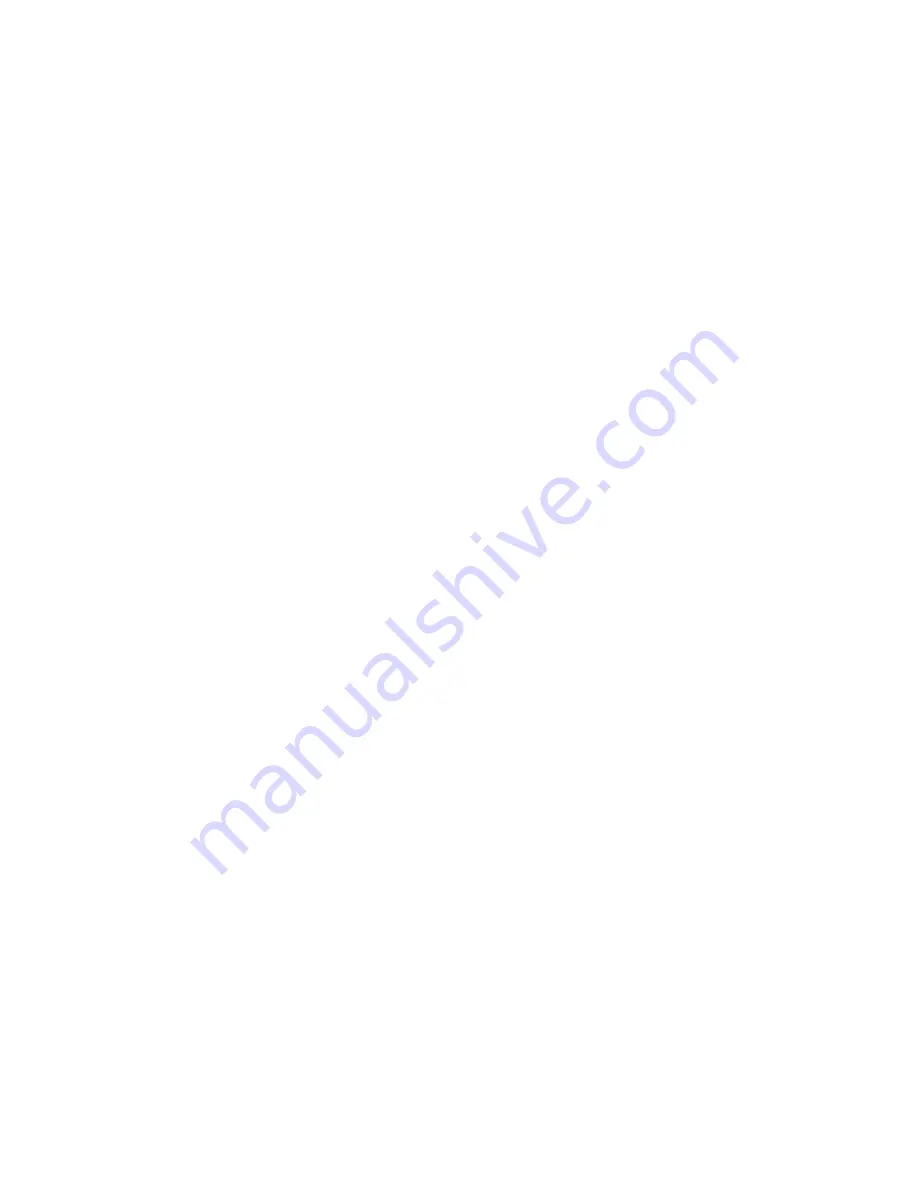
2. It is important to first determine the amount of refrigerant required for the system, the unit nameplate normally identify
the weight of the refrigerant required.
3. The refrigerant should be added in small amounts allowing sufficient time for the unit pressure to equalize each time.
WIRING
All wiring must comply with the "National Electric Code" and local electrical standards. The power supply, voltage,
frequency and phase must coincide with the unit nameplate.
Power wiring to the equipment must be adequately sized for maximum ampacity as shown on unit name plate. The unit
wiring diagram, completely illustrates the internal wiring and field connection needed for power supply and control wiring.
The power supply should be run through the sized shielded cable or rigid conduit and through a separate fused disconnect
switch/circuit breaker. For control wiring, use approved thermostat wire (minimum 18 gauge). Never use telephone wire for this
purpose. A sized circuit breaker/fused disconnect switch should be located adjacent to the unit for safety & servicing purposes.
Wiring connection to the unit must have insulation suitable for temperatures of a minimum of 60
0
C.
Minimum circuit ampacity for each model is shown on the name plate and product catalog. Equipment wiring diagram
should be examined and thoroughly understood before field wiring connections are made.
Power supply should be checked to be certain that supply voltage agrees with equipment nameplate. Serious damage to
compressors and motors can occur, if improper voltage is applied.
START-UP INSPECTION & CHECK LIST
After the installation is completed in all respect, the following points should be covered before the system is switched on for operation.
1. Remove or loosen shipping retainers under motor compressors. Make sure the hold down nuts on spring mounted
compressors are not touching the compressor feet.
2. Make sure all electrical fasteners/connections are tight and clean.
3. All controls are set according to manufacturer's instructions (low & high pressure switch, pump down pressure switch,
fan cycling switch, etc...)
4. Make sure all valves are open (compressor suction & discharge service valves, liquid line, etc.).
5. Follow all the instructions from the warning tags and stickers.
6. Compressor crankcase heater should be energized for 12 hours (special attention should be taken to disable com-
pressor contactor before energizing the unit fitted with pump down controls. If not, compressor may operate for few
minutes to pumpdown the system, even the thermostat is OFF).
7. Thorough inspection on evaporator coil, condenser coil and other components for any physical damage.
8. Expansion valve bulb is strapped properly at correct location.
9. Circuit breaker/fused disconnect switch.
10. Blower fan belt is properly tightened and pulleys are properly aligned.
11. Blower fan & condenser fans are at correct rotation and their mountings are properly tightened.
12. All refrigerant service valve caps are installed.
13. All piping, piping insulation and piping supports are properly installed.
14. Thermostat is the right one and installed properly.
15. Duct work and accessories (check the following list and select whichever applicable to each jobs).
•
Flexible Connection
•
Air Filters Clean
•
Air Filter Access Door Gasket
•
Sound Attenuators (If Applicable)
•
Fresh Air Intake
•
Ductwork Caulking Inside/Outside Building
•
Ductwork Supports Inside/Outside Building
28