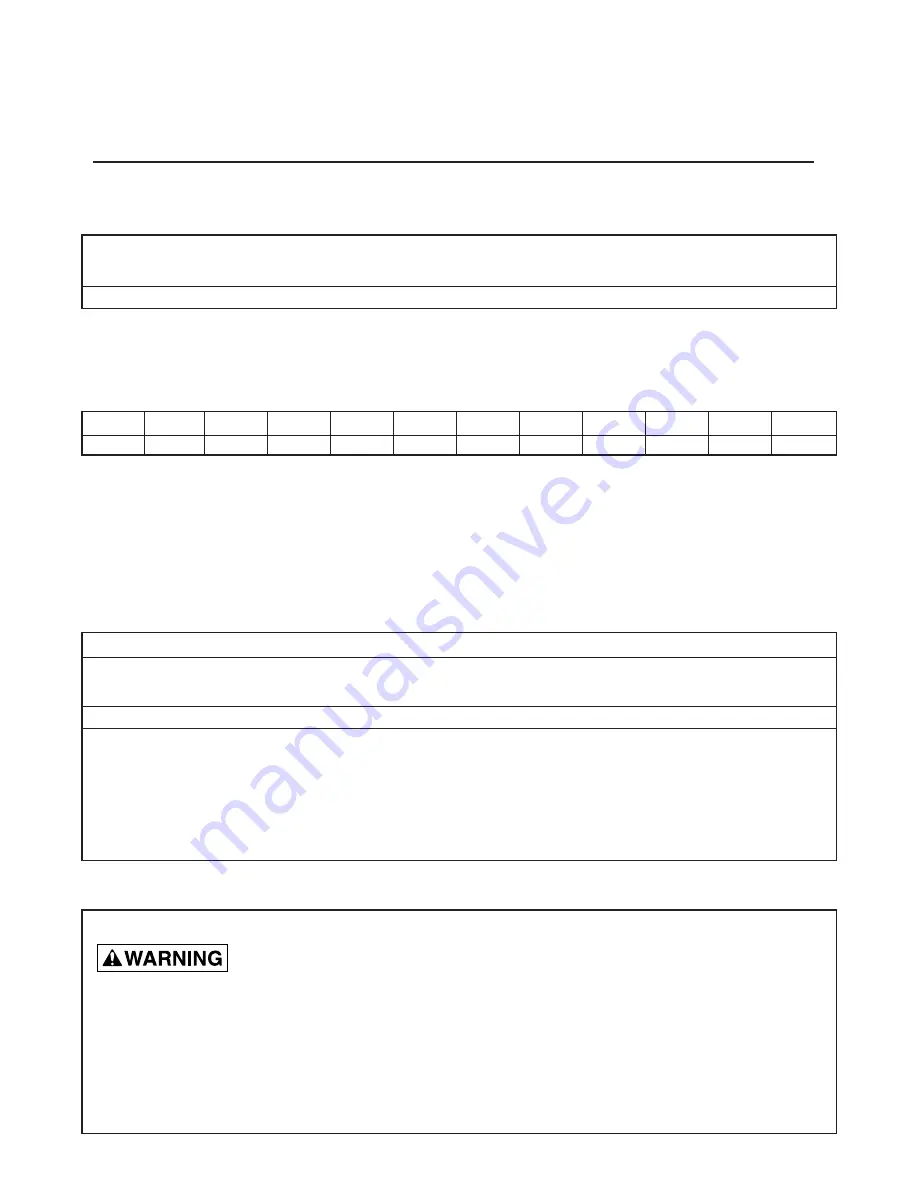
open. Start pump.
Slowly open valve until the desired flow rate is
reached. Final setting
must be within pump’s recommended oper-
ating range.
OPERATION
1. The pump must be submerged at all times during normal opera-
tion.
Do not run pump dry.
2. Make sure that the float switches are set so that the pump stops
before the pump runs dry or breaks suction. If necessary, adjust
float switches to achieve this.
3. The motor bearings are lubricated internally. No maintenance is
required or possible on the pump or the motor.
3
Volts
HP
14 AWG 12 AWG 10 AWG
8 AWG
6 AWG
4 AWG
3 AWG
2 AWG
1 AWG
0 AWG
115 1/2
99
158
247
387
603
921
1138
1403
1677
1893
Table 2: Power Supply Wire (Cable) Length in Feet
1 Phase, 2 Wire Cable, 60 Hz (Copper Wire Size - Service to motor)
Hazardous voltage. Can shock, burn,
or kill. To reduce the risk of electrical
shock during pump operation, ground and bond the pump and
motor as follows:
A. To reduce risk of electrical shock from metal parts of the assembly
other than the pump, bond together all metal parts accessible at the
tank top (including metal discharge pipe, metal tank top, and the
like). Use a metal bonding conductor at least as large as the power
cable conductors running down the well to the pump's motor.
B. Clamp or weld (or both if necessary) this bonding conductor to the
grounding means provided with the pump, which will be the equip
ment-grounding terminal, the grounding conductor on the pump
housing, or an equipment-grounding lead. The equipment-grounding
lead, when provided, will be the conductor having green insulation; it
may also have one or more yellow stripes.
C. Ground the pump, motor, and any metallic conduit that carries power
cable conductors. Ground these back to the service by connecting a
copper conductor from the pump, motor, and conduit to the ground-
ing screw provided within the supply-connection box wiring compart-
ment. This conductor must be at least as large as the circuit conduc-
tors supplying the pump.
Save these instructions.
NOTE:
Sizes given are for copper wire. For aluminum wire go two
sizes larger (i.e., if table lists #12 copper wire, use #10 aluminum
wire.)
Condition of Motor and Leads
Ohm Value
Megohm Value
New motor, without power cable
20,000,000 (or more)
20.0
Used motor, which can be reinstalled in tank
10,000,000 (or more)
10.0
Motor in Tank – Readings are Power Cable plus Motor
Do not pull pump for these reasons:
New Motor
2,000,000 (or more)
2.0
Motor in reasonably good condition
500,000 to 2,000,000
0.5–2.0
Motor which may be damaged or have damaged power cable
20,000 to 500,000
0.02–0.5
Pull pump; replace pump or cable:
Motor definitely damaged or with damaged power cable
10,000 to 20,000
0.01–0.02
Failed motor or power cable
Less than 10,000
0–0.01
Motor Insulation Resistance Readings
Normal Ohm/Megohm readings for all motors, between all leads and ground. Set ohmmmeter to 100K scale.
Table 1: Recommended Fusing Data
60 Hz/1 Phase 2-Wire Cable
Motor Winding
Max
Locked
Fuse Size
Voltz/Hz/
Resistance
Load
Rotor
Standard/
HP
Phase
Ohms
Amps
Amps
Dual Element
1/2 115/60/1
1.0-1.3
12.0
64.8
30/15
Important Electrical Grounding Information