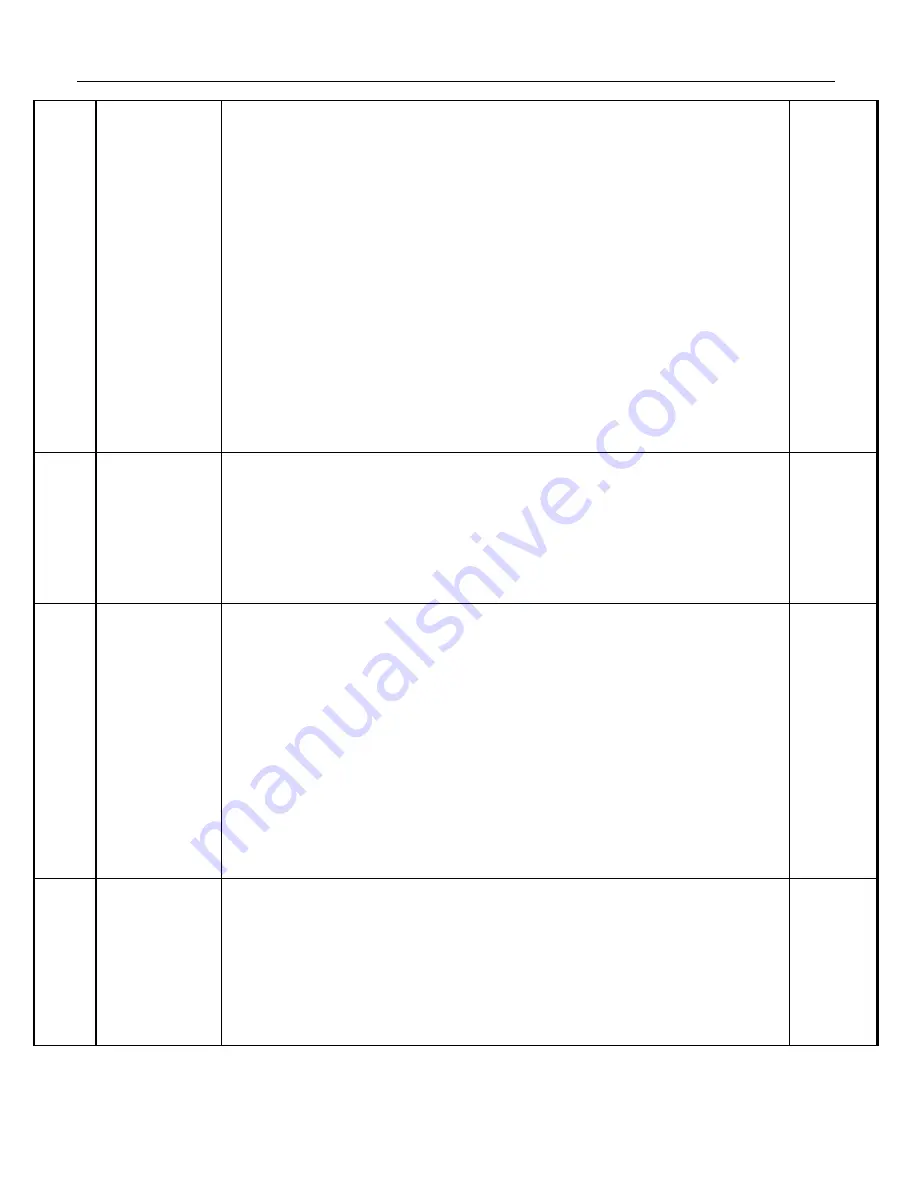
13
M5
Hold parameter
Parameter M5, P, t, CtI etc. are only for AI MPt control, and have no effect
to on-off control.
M5 is defined as measurement variation after output is changed by 5%
(0.5mA if OP1=1) and when controlled process is basically stabilized. "5"
indicates that output variation is 5 (5% or 0.5mA). Generally M5 parameter of
the same system will changes with measurement value, and so M5 parameter
should be configured with process value around operating point.
Take temperature control of electric furnace as an example, the operating
point is 700
℃
. To find out optimum M5 parameter, assuming that when out
remains 50%, the temperature of electric furnace will finally be stabilized at
700
℃
, and when output changes to 55%, the temperature will final be at 750.
Then M5 (optimum parameter)=750-700=50
℃
. M5 parameter mainly
determines the degree of integral function, similar as integral time of PID
control. The smaller M5 parameter is, the greater integral function is; where the
larger M5 parameter is, the smaller integral function is (integral time is
increased). But if M=0, then integral function an artificial intelligence control
function will be removed and the instrument is turned to be an PD adjustment
that used as a secondary controller during cascade control.
0
~
9999
units or
0
~
999.9
℃
P
rate parameter
P is in reverse proportion to measurement variations caused by output
changes by 100% in one second. It is defined as the following: if CtrL=1 or 3,
then P=1000/measurement variation per second, the unit is 0.1
℃
or 1 defined
unit .
Ex., instrument use 100% power to heat and there is no heat loss, if
temperature in crease 1
℃
each second, then P=1000/10=100. If CtrL=4, then
P parameter will be configured by increasing 10 times. Ex., P should be set to
1000 in the above example.
1
~
9999
seconds
t
Lag time
parameter
Parameter t is applied as one of the important parameters of AI artificial
intelligence control algorithm. "t" is defined as follows: time needed for a
electric furnace from the beginning of elevating temperature to get to 63.5%
against the final speed of temperature elevating, provided there is no heat loss.
The unit of parameter “t” is second.
For industrial control, hysteresis effect of the controlled process is an
important factor impairing control effect. The longer is system lag time, the
more difficult to get ideal control effect. Lag time parameter “t” is a new
introduced important parameter for AI artificial intelligence algorithm. AI series
instrument can use parameter “t” to do fuzzy calculation, and therefore
overshoot and hunting do not easily occurs and the control have the best
responsibility at the time.
The optimal t equals to derivative time in PID control. Parameter “t” gives
effect on proportional, integral and derivative function. If t
≤
CtI, derivative
function of system will be eliminated.
0
~
2000
seconds
CtI
Control period
The higher Ctl,the stronger ratio.Smaller value can improve control accuracy.
1)For SSR, thyristor or linear current output, generally 0.5
~
3 seconds.For
Relay output or in a heating/refrigerating dual output control system, generally
15 to 40 seconds, because small value will cause the frequent on-off action of
mechanical switch or frequent heating/refrigerating switch, and shorten its
service life. CtI is recommended to be 1/4 – 1/10 of lag time t, and not greater
than 60 seconds.
2)For current output, the smaller value can make quicker response,better
control result.
0
~
125
seconds