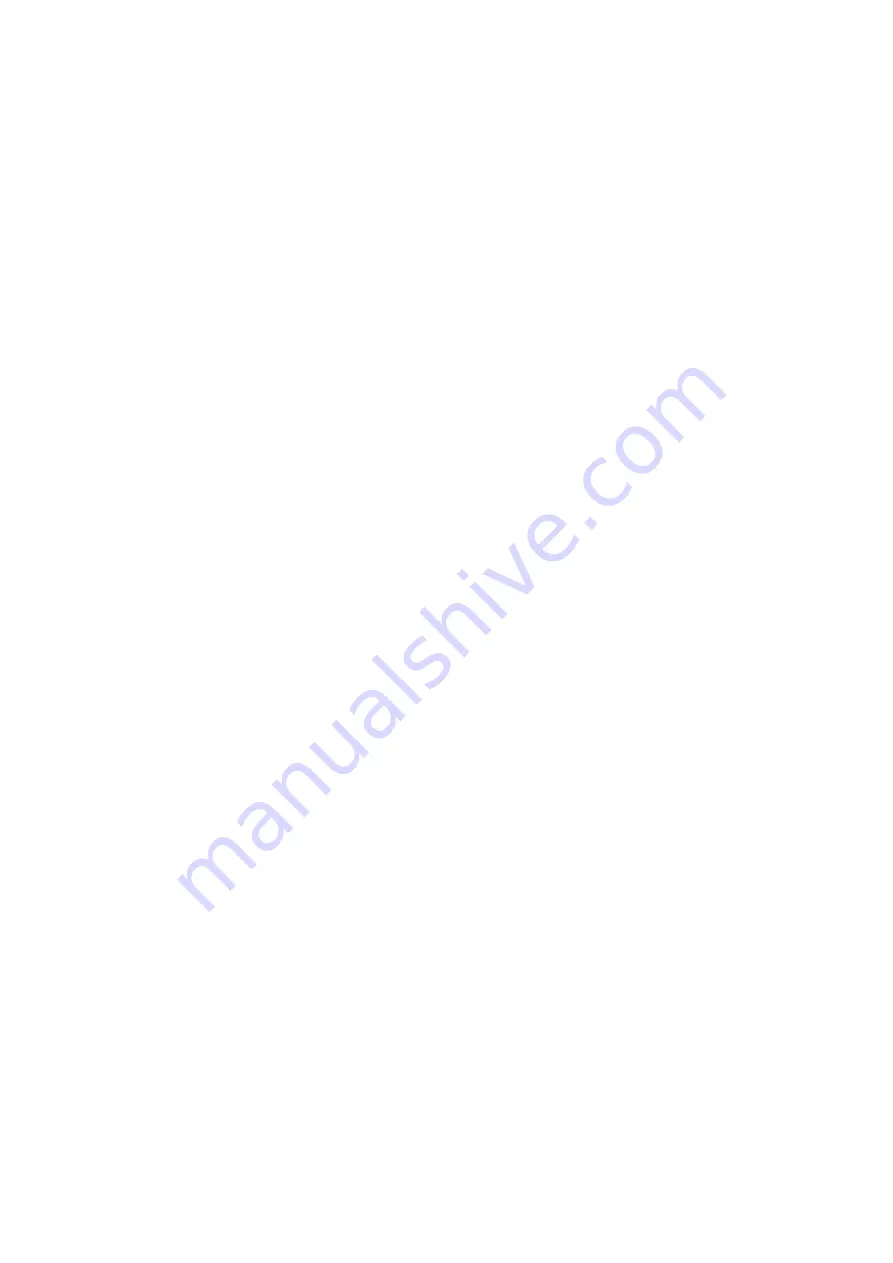
-19
-
■EPDT-292■
8.4.4 How to replace each part
How to replace gasket [3]
Disassemble the product according to procedure 4 in “8.4.2 Disassembly method”, and
replace and assemble the gasket according to procedure 6 and 7 in “8.4.3 Assembly
method”.
How to replace gasket [11]
Disassemble the product according to procedure 4 in “8.4.2 Disassembly method”, and
replace and assemble the gasket according to procedure 6 and 7 in “8.4.3 Assembly
method”.
How to replace gasket [7]
Disassemble the product according to procedures 3, 4, 6 and 7 in “8.4.2 Disassembly
method”, and replace and assemble the gasket according to procedures 1 to 6, 7 and 9
in “8.4.3 Assembly method”.
How to replace float [9]
Disassemble the product according to procedures 4 and 5 in “8.4.2 Disassembly
method”, and replace and assemble the gasket according to procedures 5 to 7 and 9 in
“8.4.3 Assembly method”.
How to replace inlet valve P [6]
Disassemble the product according to procedures 1 and 2 in “8.4.2 Disassembly
method”, and replace and assemble the inlet valve P according to procedures 8 to 10 in
“8.4.3 Assembly method”.
How to replace vent valve P [4] and vent valve seat [5]
Disassemble the product according to procedures 3 to 7 in “8.4.2 Disassembly method”,
and replace and assemble the gasket according to procedures 1 to 7 and 9 in “8.4.3
Assembly method”.
How to replace cover set
Disassemble the product according to procedures 4 in “8.4.2 Disassembly method”, and
replace and assemble the cover set according to procedures 5 to 7 in “8.4.3 Assembly
method”.