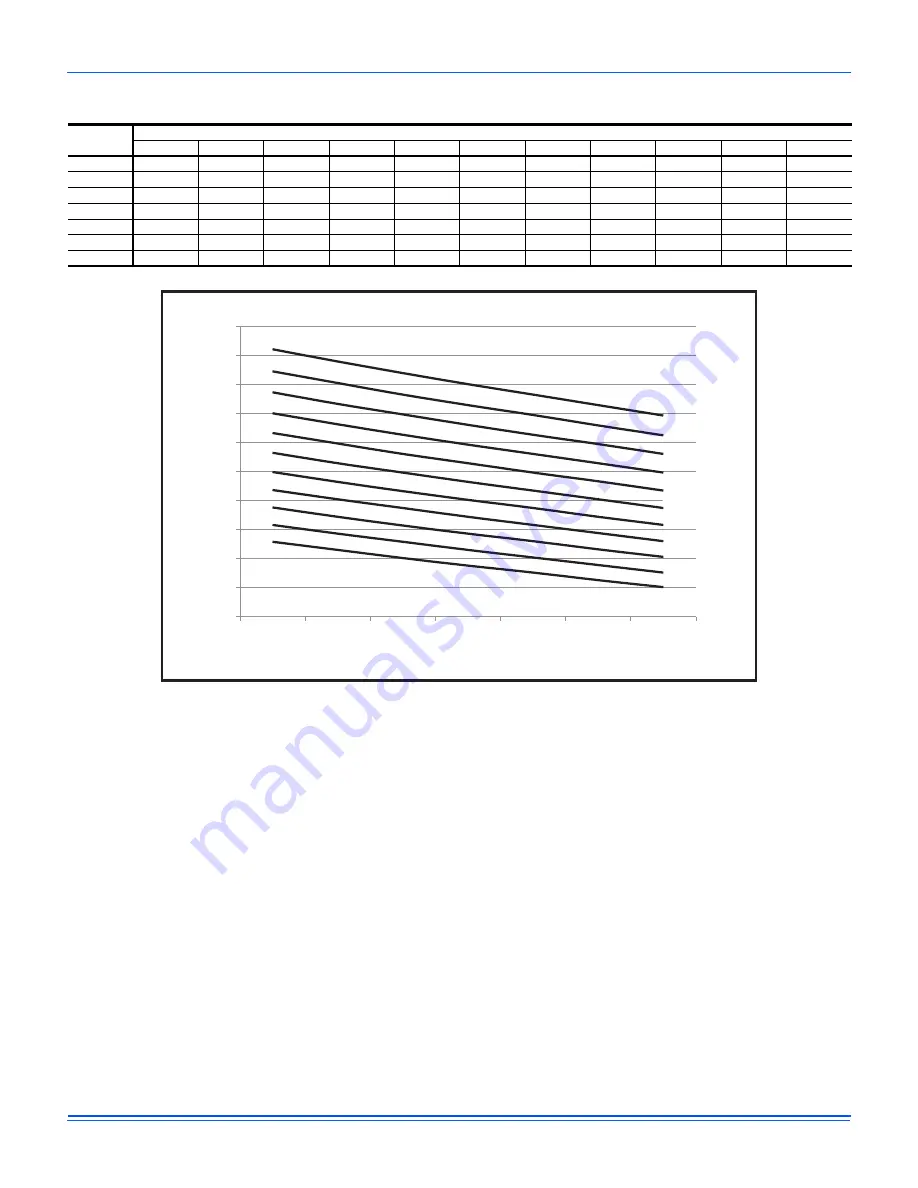
518676-BIM-C-0610
40
Johnson Controls Unitary Products
Figure 30: Altitude/Temperature Correction Factors
The examples below will assist in determining the airflow
performance of the product at altitude.
Example 1:
What are the corrected CFM, static pressure, and
BHP at an elevation of 5,000 ft. if the blower performance data
is 6,000 CFM, 1.5 IWC and 4.0 BHP?
Solution:
At an elevation of 5,000 ft. the indoor blower will still
deliver 6,000 CFM if the rpm is unchanged. However, Table 13
must be used to determine the static pressure and BHP. Since
no temperature data is given, we will assume an air temperature
of 70°F. Table 15 shows the correction factor to be 0.832.
Corrected static pressure = 1.5 x 0.832 = 1.248 IWC
Corrected BHP = 4.0 x 0.832 = 3.328
Example 2:
A system, located at 5,000 feet of elevation, is to
deliver 6,000 CFM at a static pressure of 1.5". Use the unit
blower tables to select the blower speed and the BHP
requirement.
Solution:
As in the example above, no temperature
information is given so 70°F is assumed.
The 1.5" static pressure given is at an elevation of 5,000 ft. The
first step is to convert this static pressure to equivalent sea level
conditions.
Sea level static pressure = 1.5 / .832 = 1.80"
Enter the blower table at 6000 sCFM and static pressure of
1.8". The rpm listed will be the same rpm needed at 5,000 ft.
Suppose that the corresponding BHP listed in the table is 3.2.
This value must be corrected for elevation.
BHP at 5,000 ft. = 3.2 x .832 = 2.66
Table 14: Altitude/Temperature Correction Factors
Air
Temp.
Altitude (Ft.)
0
1000
2000
3000
4000
5000
6000
7000
8000
9000
10000
40
1.060
1.022
0.986
0.950
0.916
0.882
0.849
0.818
0.788
0.758
0.729
50
1.039
1.002
0.966
0.931
0.898
0.864
0.832
0.802
0.772
0.743
0.715
60
1.019
0.982
0.948
0.913
0.880
0.848
0.816
0.787
0.757
0.729
0.701
70
1.000
0.964
0.930
0.896
0.864
0.832
0.801
0.772
0.743
0.715
0.688
80
0.982
0.947
0.913
0.880
0.848
0.817
0.787
0.758
0.730
0.702
0.676
90
0.964
0.929
0.897
0.864
0.833
0.802
0.772
0.744
0.716
0.689
0.663
100
0.946
0.912
0.880
0.848
0.817
0.787
0.758
0.730
0.703
0.676
0.651
0.600
0.650
0.700
0.750
0.800
0.850
0.900
0.950
1.000
1.050
1.100
40
50
60
70
80
90
100
Air Temperature (ºF)
Correction Factor
Sea Level
1000 ft
2000 ft
3000 ft
4000 ft
6000 ft
7000 ft
8000 ft
9000 ft
10000 ft
5000 ft