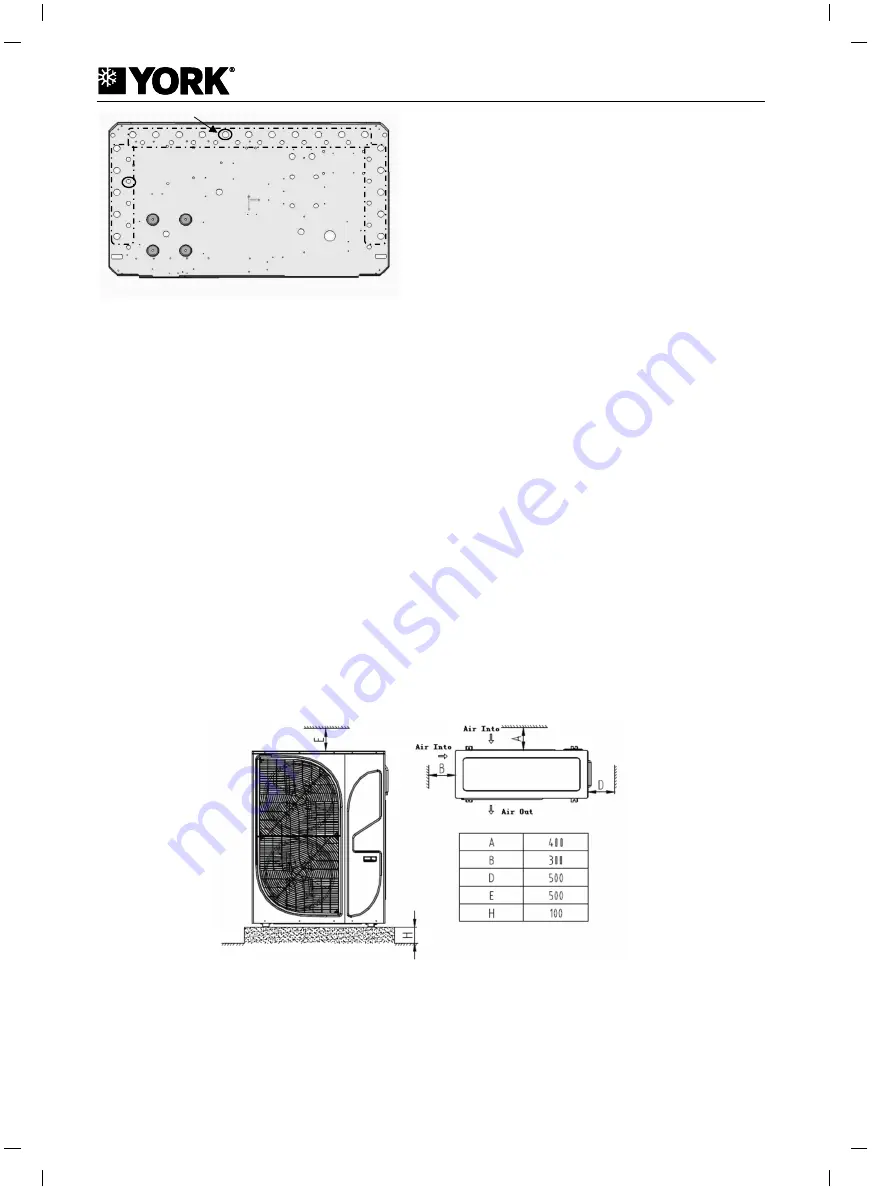
FORM NO.:
6U5M-A11M-N
B
-
EN
JOHNSON CONTROLS
13
FIGURE
7
-BACKPLANE SCHEMATIC
(040)
Compressor mounting
The compressor is mounted on four (4) rubber or steel
isolators. The mounting bolts should not be loosened or
adjusted during installation of the unit.
INSTALL
SPACING
Placement on a level surface of free of obstructions
(including snow, for winter operation) or air circulation
ensures rated performance, reliable operation, and ease
of maintenance. Site restrictions may compromise
minimum clearances indicated above, resulting in
unpredictable airflow patterns and possible diminished
performance. YORK’s unit control will optimize
operation without nuisance high-pressure safety
cutouts; however, the system designer must consider
potential performance degradation.
The influence of downward flow caused by tall
buildings around the unit toward the exhaust air of the
unit shall also be taken into consideration in installation.
If the unit is installed at a place with violent airflow,
such as exposed roof, measures including parapet or
blinds shall be taken to prevent turbulent flow from
interfering the air flow into the unit. If the unit needs to
set parapet, the height shall not be taller than the unit
and the clearance between the unit and the parapet or
the blinds shall also satisfy the minimum clearance
requirement for unit installation.
When the unit is placed on a snow covered surface, the
bottom face of the unit should be at least 100mm higher
than the surface of the snow cover to guarantee the air
successfully flow through the coil exchanger.
No obstructions allowed in front of the airflow outlet
except grilling of blinds. The effective aperture
opening ratio of the grating shall be over 80% and the
angle of inclination of the grating blades shall be over
20°, and the blade pitch shall be over 100mm
INSTALLATION CLEARANCES
Units are surrounded by walls or other obstacles, installation spacing, referring to the following figure.
YVAG012~033
21*Φ30mm
20*Φ20mm
Cooke Industries - Phone: +64 9 579 2185 Email: [email protected] Web: www.cookeindustries.co.nz