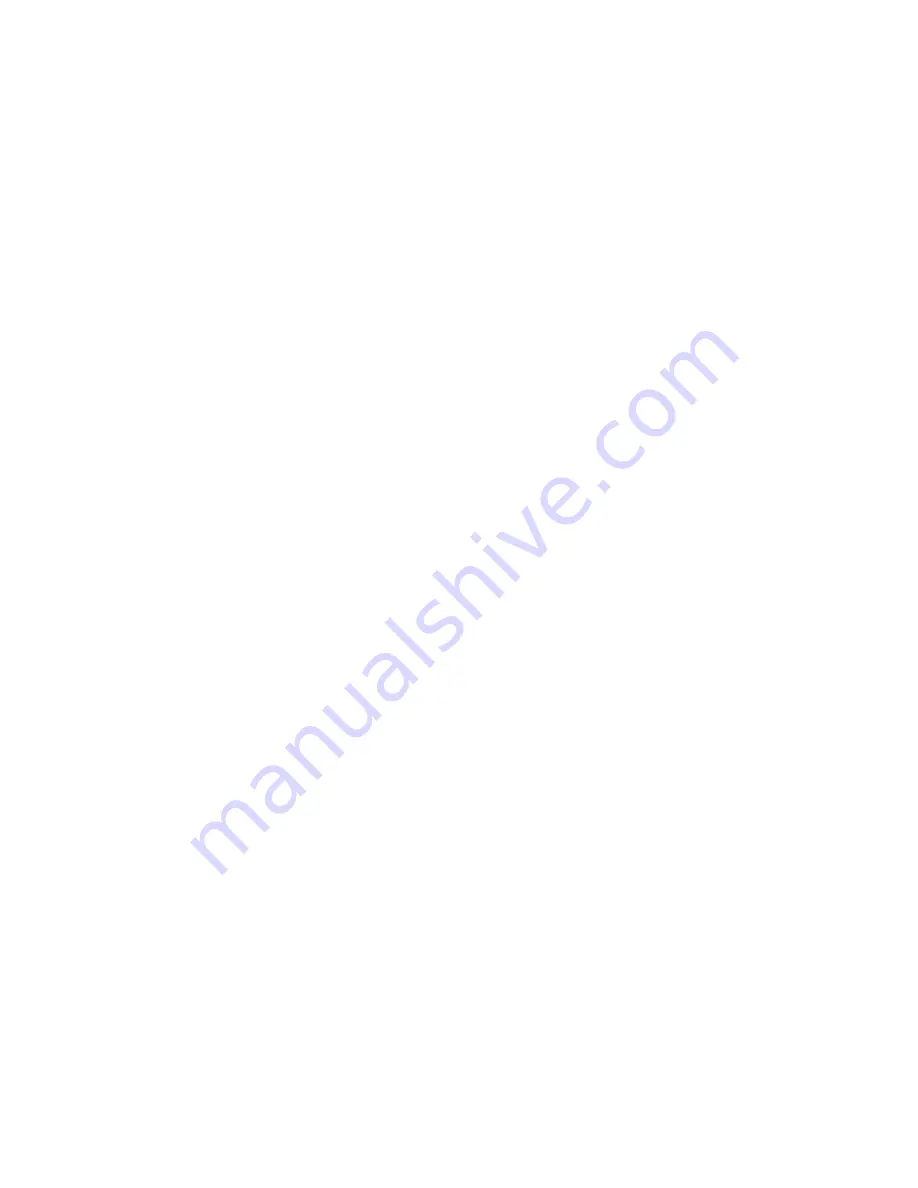
Johnson Controls
178
Form 150.72-ICOM6
Issue date: 12/19/2023
Section 8: Unit operation
Leaving chilled liquid system lead/lag
and compressor sequencing
A Lead/Lag option may be selected to help equalize
average run hours between systems with 2 refriger-
ant systems. This may be programmed under the OP-
TIONS key. Auto Lead/Lag allows automatic Lead/
Lag of the two systems based on average run hours of
the compressors in each system. Manual Lead/Lag se-
lects specifically the sequence which the microproces-
sor starts systems.
On a hot water start, once a system starts, it will turn
ON all compressors before the next system starts a
compressor. The microprocessor will sequence com-
pressors within each circuit to maximize individual
compressor run time on individual compressors within
a system to prevent short cycling.
Each compressor in a system will be assigned an arbi-
trary priority number 1, 2, or 1, 2, 3. The non-running
compressor within a system with the lowest priority
number will always be the next compressor to start.
The running compressor with priority number 1 will al-
ways be the next to shut OFF. Whenever a compressor
is shut OFF, the priority numbers of all compressors
will be decreased by 1 with wrap-around. This control
scheme ensures the same compressor does not repeat-
edly cycle ON and OFF.
Once the second system starts a compressor on a 2 sys-
tem chillers, the microprocessor will attempt to equally
load each system as long as the system is not limit-
ing or pumping down. Once this occurs, loading and
unloading will alternate between systems, loading the
lead system first or unloading the lag system first.
Return chilled liquid system lead/lag
and compressor sequencing
A Lead/Lag option may be selected to help equalize
average run hours between systems with 2 refriger-
ant systems. This may be programmed under the OP-
TIONS key. Auto Lead/Lag of the 2 systems based on
average run hours of the compressors in each system.
Manual Lead/Lag selects specifically the sequence
which the microprocessor starts the systems.
The microprocessor will sequence compressors load and
unload systems. The microprocessor will lead/lag com-
pressors within each circuit to maximize individual com-
pressor run time for the purpose of lubrication. It will also
prevent the same compressor from starting 2 times in a
row. The microprocessor will not attempt to equalize run
time on individual compressors within a system.
Each compressor in a system will be assigned an ar-
bitrary number 1, or 2. The non-running compressor
within a system with the lowest priority number will
always be the next compressor to start. The running
compressor with priority number 1 will always be the
next compressor to shut OFF. Whenever a compressor
is shut OFF, the priority numbers of all compressors
in each system will be decreased by 1 with the wrap
around. This control scheme ensures the same com-
pressor does not repeatedly cycle ON and OFF.
Anti-recycle timer
The programmable anti-recycle timer ensures that sys-
tems do not cycle. This timer is programmable under
the PROGRAM key between 300 and 600 seconds.
Whenever possible, to reduce cycling and motor heat-
ing, the anti-recycle timer should be adjusted to 600
seconds. The programmable anti-recycle timer starts
the timer when the first compressor in a system starts.
The timer begins to count down. If all of the compres-
sors in a circuit cycle OFF, a compressor within the cir-
cuit will not be permitted to start until the anti-recycle
timer has timed out. If the lead system has run for less
than 5 minutes, 3 times in a row, the anti-recycle timer
will be extended to 10 minutes.
Anti-Coincidence Timer
This timer is not present on single-system units. Two
timing controls are present in software to ensure com-
pressors within a circuit or between systems, do not
start simultaneously. The anti-coincidence timer en-
sures there is at least a one minute delay between sys-
tem starts on 2-circuit systems. This timer is NOT pro-
grammable. The load timers further ensure that there
is a minimum time between compressor starts within
a system.
Evaporator pump control and YORK
hydro kit pump control
The evaporator pump dry contacts (XTBC2 – Termi-
nals 23 and 24) are energized when any of the follow-
ing conditions are true:
1. Low Leaving Chilled Liquid Fault
2. Any compressor is running
3. Daily Schedule is ON, Unit Switch is ON and Re-
mote Stop is closed