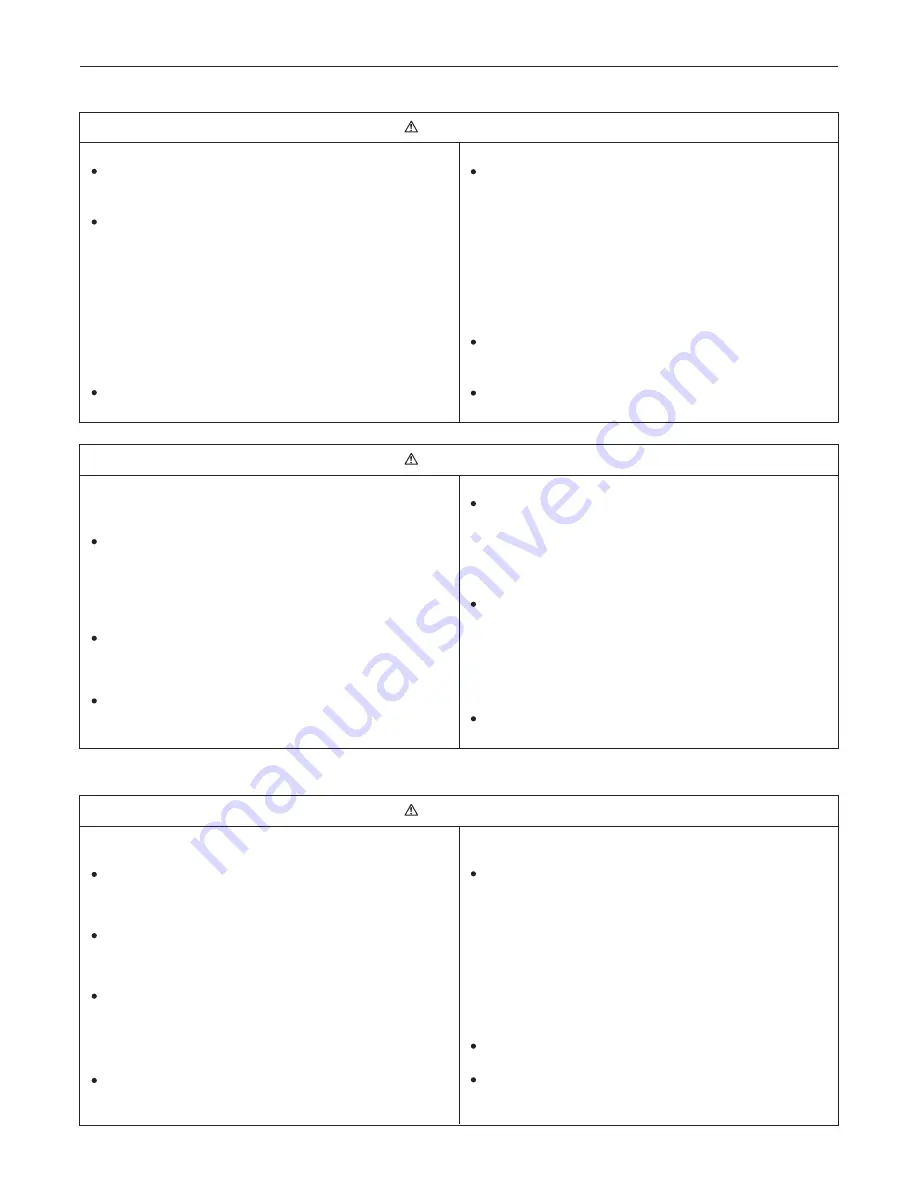
5
Safety Precautions
Precautions for Handling Units for Use with R410A
Do not use the existing refrigerant piping
The old refrigerant and refrigerator oil in the existing piping
contain a large amount of chlorine, which will cause the
refrigerator oil in the new unit to deteriorate.
R410A is a high-pressure refrigerant, and the use of the
existing piping may result in bursting.
Keep the inner and outer surfaces of the pipes clean and
free of contaminants such as sulfur, oxides, dust/dirt shaving
particles,oils,and moisture.
Contaminants inside the refrigerant piping will cause the
refrigerant oil to deteriorate.
Use a vacuum pump with a reverse-flow check valve.
If other types of valves are used, the vacuum pump oil will
flow back into the refrigerant cycle and cause the refrigerator
oil to deteriorate.
Do not use the following tools that have been used with the
conventional refrigerants. Prepare tools that are for exclusive
use with R410A.
(Gauge manifold, charging hose, gas leak detector,
reverse-flow check valve, refrigerant charge base,vacuum
gauge, and refrigerant recovery equipment.)
If refrigerant and/or refrigerant oil left on these tools are
mixed in with R410, or if water is mixed with R410A, it will
cause the refrigerant to deteriorate.
Since R410A does not contain chlorine, gas-leak detectors
for conventional refrigerators will not work.
Store the piping to be used during installation indoors, and
keep both ends of the piping sealed until immediately before
brazing.(keep elbows and other joints wrapped in plastic.)
If dust, dirt, or water enters the refrigerant cycle, it may
cause the oil in the unit to deteriorate or may cause the
compressor to malfunction.
A large amount of mineral oil will cause the refrigerating
machine oil to deteriorate.
Use a small amount of ester oil, ether oil, or alkylbenzene
to coat flares and flange connections.
Use liquid refrigerant to charge the system.
Charge the unit with gas refrigerant will cause the refrigerant
in the cylinder to change its composition and will lead to
a drop in performance
Do not use a charging cylinder.
The use of charging cylinder will change the composition
of the refrigerant and lead to power loss.
Exercise special care when handling the tools.
An introduction of foreign objects such as dust, dirt or
water into the refrigerant cycle will cause the refrigerating
machine oil to deteriorate.
Only use R410A refrigerant.
The use of refrigerants containing chlorine(i.e. R22) will
cause the refrigerant to deteriorate.
Before Installing the Unit
Do not install the unit in a place where there is a possibility
of flammable gas leak.
Leaked gas accumulated around the unit may start a fire.
Do not use the unit to preserve food, animals, plants, artifacts,
or for other special purposes.
The unit is not designed to provide adepuate conditions
to preserve the quality of these items.
Do not use the unit in an unusual environment
The use of the unit in the presence of a large amount of
oil, steam, acid, alkaline solvents or special types of sprays
may lead to a remarkable drop in performance and/or
malfunction and presents a risk of electric shock, smoke,
or fire.
The presence of organic solvents, corroded gas (such as
ammonia,sulfur compounds,and acid may cause gas or
water leak.)
When installing the unit in a hospital, take necessary measures
against noise.
High-frequency medical equipment may interfere with the
normal operation of the air conditioning unit or the air
conditioning unit may interfere with the normal operation
of the medical equipment
When humidity level exceeds 80% or when the drainage
system is clogged, indoor units may drip water.
Installation of a centralized drainage system for the outdoor
unit may also need to be considered to prevent water drips
from the outdoor units.
Do not place the unit on or over things that may not get wet.
Caution
Caution
Caution
Summary of Contents for YHUJYH(024-060)BAR(S)XA-X(Y)
Page 3: ......
Page 19: ...Troubleshooting 18 24K 28K 36K 48K R X 48K S X 48K S Y 60K ...